Download PDF
How Henkel Uses FourKites Supply Chain Visibility to Improve the Customer Experience and Company Operations
Technology Category
- Functional Applications - Fleet Management Systems (FMS)
- Analytics & Modeling - Predictive Analytics
- Sensors - GPS
Applicable Industries
- Consumer Goods
- Automotive
- Healthcare & Hospitals
Applicable Functions
- Logistics & Transportation
- Warehouse & Inventory Management
Use Cases
- Fleet Management
- Supply Chain Visibility
- Track & Trace of Assets
Services
- System Integration
- Software Design & Engineering Services
The Challenge
Henkel faced challenges with visibility into the location of its in-transit shipments, which affected efficiency and customer satisfaction. The company needed to improve supply chain visibility to better monitor and benchmark logistics service providers (LSPs), track and troubleshoot late shipments, and minimize associated fees and penalties. Henkel also aimed to eliminate manual processes for tracking shipments, which placed a significant burden on customer service teams.
About The Customer
Henkel AG & Co. KGaA is a multinational industrial and consumer goods company headquartered in Düsseldorf, Germany. The company operates in various sectors, including aerospace, automotive, technology, healthcare, food and beverage, and consumer goods. Henkel's Adhesive Technologies business unit is a global leader in adhesives, sealants, and functional coatings. With a diverse team of over 50,000 employees worldwide, Henkel is committed to sustainability and innovation. The company reported sales of more than 22 billion euros in fiscal 2022 and is listed in the German stock index DAX.
The Solution
Henkel partnered with FourKites to enhance supply chain visibility and improve customer experience. The FourKites platform provided real-time visibility into shipments, enabling Henkel to monitor and benchmark LSP performance, track and troubleshoot late shipments, and reduce manual tracking processes. The implementation was staged, with dedicated project managers demonstrating the benefits to LSPs and securing buy-in from internal stakeholders. The platform allowed customer service representatives to access real-time visibility and up-to-date ETAs, improving their ability to track shipments and proactively share updates with customers. Sales reps and finance teams also benefited from the accurate delivery data provided by FourKites.
Operational Impact
Quantitative Benefit
Related Case Studies.
.png)
Case Study
Improving Vending Machine Profitability with the Internet of Things (IoT)
The vending industry is undergoing a sea change, taking advantage of new technologies to go beyond just delivering snacks to creating a new retail location. Intelligent vending machines can be found in many public locations as well as company facilities, selling different types of goods and services, including even computer accessories, gold bars, tickets, and office supplies. With increasing sophistication, they may also provide time- and location-based data pertaining to sales, inventory, and customer preferences. But at the end of the day, vending machine operators know greater profitability is driven by higher sales and lower operating costs.
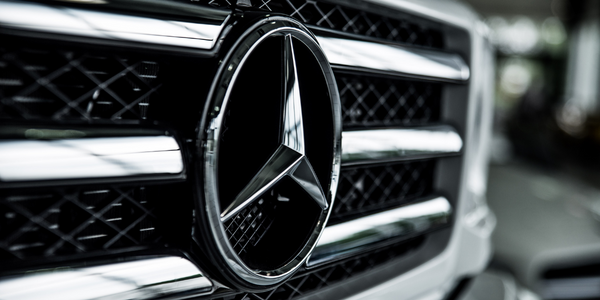
Case Study
Integral Plant Maintenance
Mercedes-Benz and his partner GAZ chose Siemens to be its maintenance partner at a new engine plant in Yaroslavl, Russia. The new plant offers a capacity to manufacture diesel engines for the Russian market, for locally produced Sprinter Classic. In addition to engines for the local market, the Yaroslavl plant will also produce spare parts. Mercedes-Benz Russia and his partner needed a service partner in order to ensure the operation of these lines in a maintenance partnership arrangement. The challenges included coordinating the entire maintenance management operation, in particular inspections, corrective and predictive maintenance activities, and the optimizing spare parts management. Siemens developed a customized maintenance solution that includes all electronic and mechanical maintenance activities (Integral Plant Maintenance).
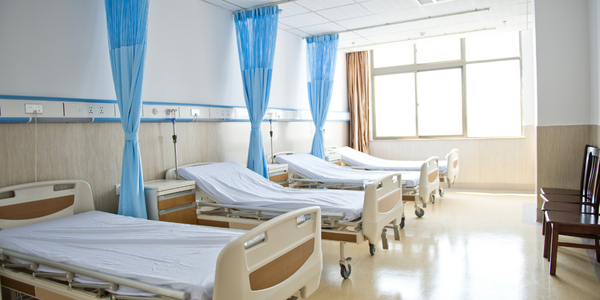
Case Study
Hospital Inventory Management
The hospital supply chain team is responsible for ensuring that the right medical supplies are readily available to clinicians when and where needed, and to do so in the most efficient manner possible. However, many of the systems and processes in use at the cancer center for supply chain management were not best suited to support these goals. Barcoding technology, a commonly used method for inventory management of medical supplies, is labor intensive, time consuming, does not provide real-time visibility into inventory levels and can be prone to error. Consequently, the lack of accurate and real-time visibility into inventory levels across multiple supply rooms in multiple hospital facilities creates additional inefficiency in the system causing over-ordering, hoarding, and wasted supplies. Other sources of waste and cost were also identified as candidates for improvement. Existing systems and processes did not provide adequate security for high-cost inventory within the hospital, which was another driver of cost. A lack of visibility into expiration dates for supplies resulted in supplies being wasted due to past expiry dates. Storage of supplies was also a key consideration given the location of the cancer center’s facilities in a dense urban setting, where space is always at a premium. In order to address the challenges outlined above, the hospital sought a solution that would provide real-time inventory information with high levels of accuracy, reduce the level of manual effort required and enable data driven decision making to ensure that the right supplies were readily available to clinicians in the right location at the right time.