How to Connect & Take Control
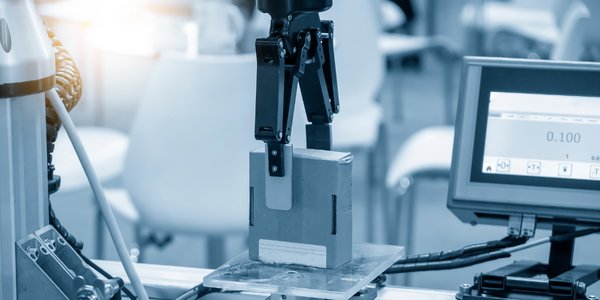
- Networks & Connectivity - RFID
- Construction & Infrastructure
- Logistics & Transportation
- Fleet Management
Customers have very similar challenges nowadays. Cost saving is high on the agenda as is safety. Common themes under customers with Materials Handling Equipment are; how to make sure that they stay within contracted hours but not under use the equipment. Another point is out of contract cost caused by misuse of equipment. We from Hyster like to help our customers to find a solution that fits your organization. With Hyster Tracker we are able to track your trucks and help to save you money. General savings can be up to 20% spread across different parts of the business. For example with the digital operator checklists which saves time and reduces the paper hassle. Or with the rotation of equipment when we see underutilization in one place and over usage in another, based on the telemetry data.
The first level of Hyster Tracker technology includes all of the essential tracking capabilities that help to effectively manage fleets of trucks and operators. This data can help to identify equipment that may be over-utilised, which may otherwise lead to increased maintenance and service costs. It can also identify under-used equipment. Operator access control works with RFID cards to ensure that specific equipment is used only by authorised or appropriately trained operators. It also helps to manage incidents and improve driver accountability by identifying who was operating a truck in the event of a recorded incident. To drive down fuel or power costs, the idle shutdown function can also be set. Operator Pre-shift Checklist Tracking forces the operator to complete a series of verifications before the equipment can be operated
Related Case Studies.
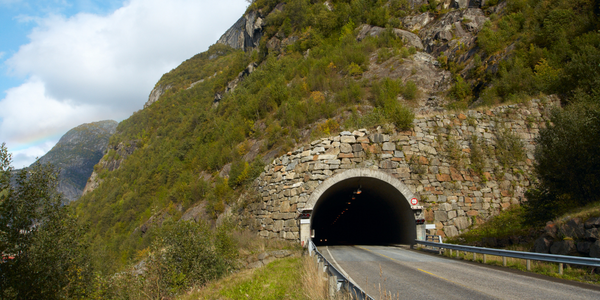
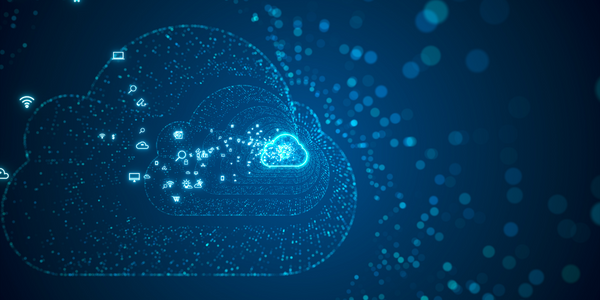
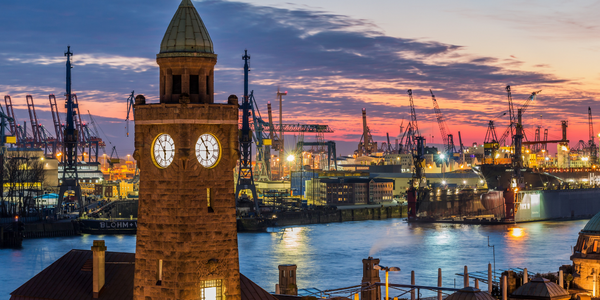
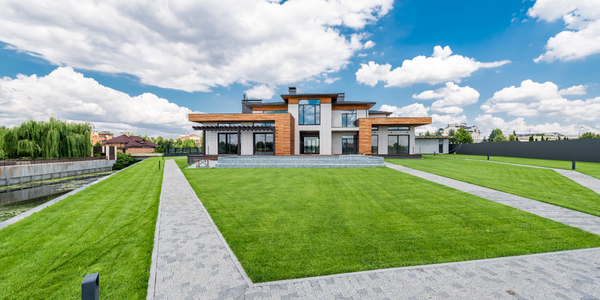
