Download PDF
Increasing Engineering Productivity through Smart Deployment of Simulation: A Case Study on Oticon
Technology Category
- Analytics & Modeling - Digital Twin / Simulation
- Platform as a Service (PaaS) - Device Management Platforms
Applicable Industries
- Electronics
- Equipment & Machinery
Applicable Functions
- Product Research & Development
- Quality Assurance
Use Cases
- Manufacturing Process Simulation
- Virtual Training
Services
- System Integration
- Training
The Challenge
The global hearing aid market is becoming increasingly competitive due to an aging population and higher life expectancy. In this environment, medical device manufacturers need to bring advanced products to market quickly and without incurring additional costs late in the development cycle. However, many companies deploy their engineering resources late in the development process to address design and manufacturing problems prior to product rollout. This approach often results in vital engineering resources being used to fix design problems rather than designing products that better meet customer needs and critical design requirements the first time. Oticon, a manufacturer of hearing aids, realized the value of engineering simulation and used it to design and validate key components of its devices. However, to become a global leader in innovation and stay ahead of the competition, Oticon needed to apply simulation to all the components interacting in the product, requiring a scalable, systems-level approach to design.
About The Customer
Oticon is a business unit of the William Demant company that manufactures hearing aids. The company recognized the value of engineering simulation and used it to design and validate key components of its devices. However, to become a true global leader in innovation and stay ahead of the competition, Oticon realized it needed to apply simulation not just to key parts of the hearing aid, but to all the components interacting in the product. This required a scalable, systems-level approach to design with senior management buy-in to re-allocate engineering resources and a customized simulation workflow.
The Solution
Oticon leveraged the ANSYS® Application Customization Toolkit (ACT), a development tool that uses a common language to configure and customize the simulation user interface, simulation workflow, and solver extensions. This allowed Oticon to scale its product development process across the engineering staff and efficiently design the entire hearing aid system virtually. The implementation involved three steps: gaining executive support for the systematic deployment of simulation in the early stages of the design process, customizing the workflow to increase CAE accessibility to design engineers with little to no formal CAE training or experience, and validating a computer model that accurately predicts the performance of the entire hearing aid system. Oticon's CAE experts developed advanced computer-based models of critical hearing aid components, which were extensively authenticated and became an accepted tool for validating designs prior to the final prototyping/testing phase of the product development process.
Operational Impact
Quantitative Benefit
Related Case Studies.
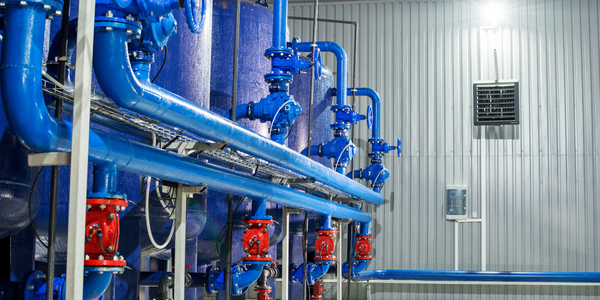
Case Study
Smart Water Filtration Systems
Before working with Ayla Networks, Ozner was already using cloud connectivity to identify and solve water-filtration system malfunctions as well as to monitor filter cartridges for replacements.But, in June 2015, Ozner executives talked with Ayla about how the company might further improve its water systems with IoT technology. They liked what they heard from Ayla, but the executives needed to be sure that Ayla’s Agile IoT Platform provided the security and reliability Ozner required.
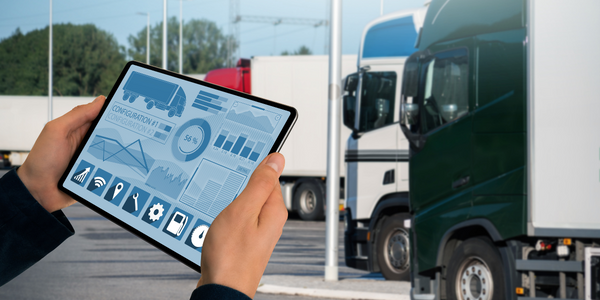
Case Study
IoT enabled Fleet Management with MindSphere
In view of growing competition, Gämmerler had a strong need to remain competitive via process optimization, reliability and gentle handling of printed products, even at highest press speeds. In addition, a digitalization initiative also included developing a key differentiation via data-driven services offers.
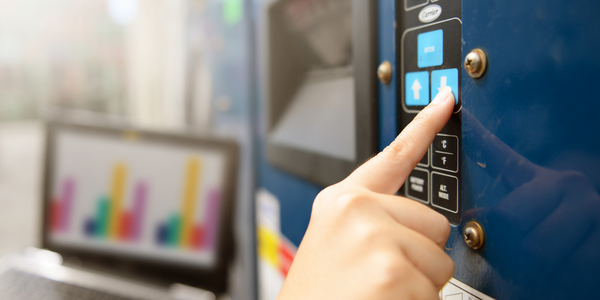
Case Study
Remote Temperature Monitoring of Perishable Goods Saves Money
RMONI was facing temperature monitoring challenges in a cold chain business. A cold chain must be established and maintained to ensure goods have been properly refrigerated during every step of the process, making temperature monitoring a critical business function. Manual registration practice can be very costly, labor intensive and prone to mistakes.
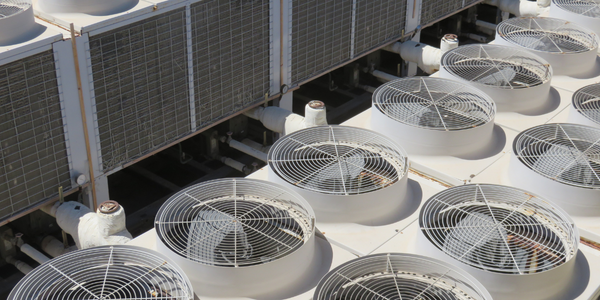
Case Study
Predictive Maintenance for Industrial Chillers
For global leaders in the industrial chiller manufacturing, reliability of the entire production process is of the utmost importance. Chillers are refrigeration systems that produce ice water to provide cooling for a process or industrial application. One of those leaders sought a way to respond to asset performance issues, even before they occur. The intelligence to guarantee maximum reliability of cooling devices is embedded (pre-alarming). A pre-alarming phase means that the cooling device still works, but symptoms may appear, telling manufacturers that a failure is likely to occur in the near future. Chillers who are not internet connected at that moment, provide little insight in this pre-alarming phase.
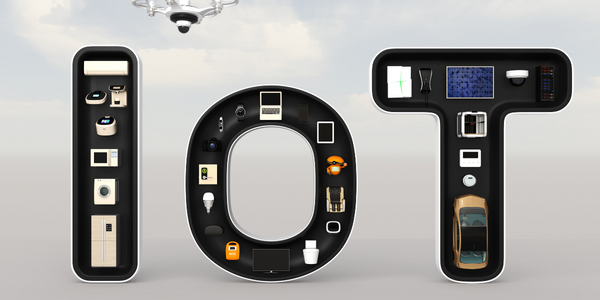
Case Study
Premium Appliance Producer Innovates with Internet of Everything
Sub-Zero faced the largest product launch in the company’s history:It wanted to launch 60 new products as scheduled while simultaneously opening a new “greenfield” production facility, yet still adhering to stringent quality requirements and manage issues from new supply-chain partners. A the same time, it wanted to increase staff productivity time and collaboration while reducing travel and costs.