Download PDF
Innovative Plastech, Inc. Ramping up Thermoformed Product Design Throughput with Solidworks
Technology Category
- Functional Applications - Product Lifecycle Management Systems (PLM)
- Analytics & Modeling - Predictive Analytics
- Functional Applications - Manufacturing Execution Systems (MES)
Applicable Industries
- Consumer Goods
- Packaging
Applicable Functions
- Product Research & Development
- Quality Assurance
Use Cases
- Predictive Maintenance
- Manufacturing System Automation
Services
- Software Design & Engineering Services
- System Integration
The Challenge
Maximize thermoformed product design throughput by improving quality, streamlining processes, and leveraging surfacing tools.
About The Customer
Many consumer product manufacturers depend on custom, thermoformed product solutions from Innovative Plastech, Inc. (IPI). The Illinois-based custom thermoformer of plastic vacuum-formed products also provides custom packaging solutions to many other industries. From customized shipping trays, form-fit clamshells, and anti-static packaging to trifolds and blister packs for hardware, electrical components, toys, food, tools, and cosmetics, IPI is a major supplier of superior thermoformed products and tooling. IPI is committed to leveraging the latest technology to develop the tooling it uses to produce custom thermoformed products.
The Solution
After evaluating 3D packages, IPI chose SOLIDWORKS solutions, implementing SOLIDWORKS Professional and SOLIDWORKS Premium design software. The thermoformer selected SOLIDWORKS software because it’s easy to learn and use, provides robust surface modeling and mold development tools, and integrates well with the SOLIDWORKS Gold Partner applications MasterCAM® for manufacturing and DezignWorks® for reverse engineering. IPI moved to 3D to automate processes and reuse existing data, believing SOLIDWORKS provided the best collection of tools to support their needs. The implementation of SOLIDWORKS has enabled IPI to boost productivity, improve design accuracy, and reduce material usage and rework.
Operational Impact
Quantitative Benefit
Related Case Studies.
.png)
Case Study
Improving Vending Machine Profitability with the Internet of Things (IoT)
The vending industry is undergoing a sea change, taking advantage of new technologies to go beyond just delivering snacks to creating a new retail location. Intelligent vending machines can be found in many public locations as well as company facilities, selling different types of goods and services, including even computer accessories, gold bars, tickets, and office supplies. With increasing sophistication, they may also provide time- and location-based data pertaining to sales, inventory, and customer preferences. But at the end of the day, vending machine operators know greater profitability is driven by higher sales and lower operating costs.
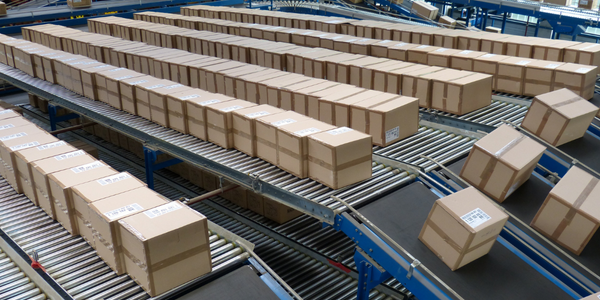
Case Study
IoT Data Analytics Case Study - Packaging Films Manufacturer
The company manufactures packaging films on made to order or configure to order basis. Every order has a different set of requirements from the product characteristics perspective and hence requires machine’s settings to be adjusted accordingly. If the film quality does not meet the required standards, the degraded quality impacts customer delivery causes customer dissatisfaction and results in lower margins. The biggest challenge was to identify the real root cause and devise a remedy for that.
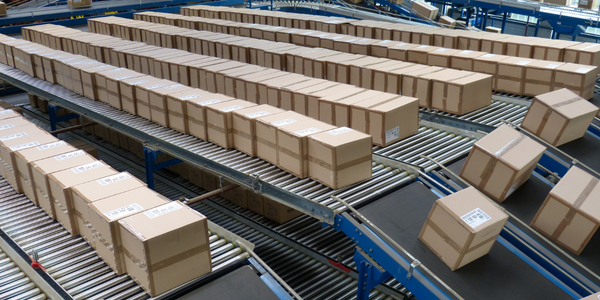
Case Study
Zenon the Ideal Basis for An Ergonomic HMI
KHS develops and produces machines and equipment for filling and packaging in the drinks industry. Because drinks manufacturing, filling and packaging consist of a number of highly complex processes, the user-friendly and intuitive operation of equipment is increasingly gaining in significance. In order to design these processes as simple as possible for the user, KHS decided to introduce a uniform, transparent and standardized solution to the company. The HMI interface should meet the requirement for people with different qualifications and enable them to work on a standard platform.
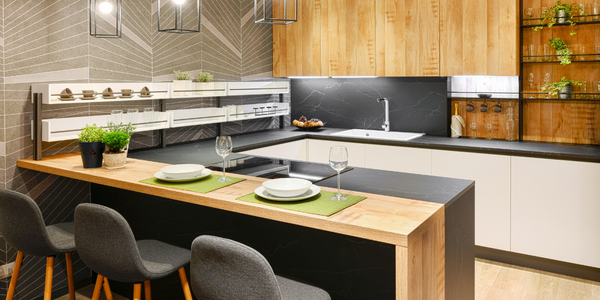
Case Study
Series Production with Lot-size-1 Flexibility
Nobilia manufactures customized fitted kitchens with a lot size of 1. They require maximum transparency of tracking design data and individual processing steps so that they can locate a particular piece of kitchen furniture in the sequence of processes.