Download PDF
Iowa State University's Cyclone Racing Team Leverages IoT for Enhanced Vehicle Performance
Technology Category
- Drones - Fixed-Wing Drones
- Sensors - Autonomous Driving Sensors
Applicable Industries
- Automotive
- Equipment & Machinery
Applicable Functions
- Product Research & Development
- Quality Assurance
Use Cases
- Smart Parking
- Vehicle-to-Infrastructure
The Challenge
Cyclone Racing, Iowa State University’s Formula SAE team, was faced with the challenge of reducing the weight of their latest vehicle, CR22, specifically the vehicle's rear aerodynamic wing. The previous year's car had a heavy internal wing structure that led to excessive roll and instability during races. The team aimed to design a lightweight yet extremely stiff modified swan neck wing mount for the Formula SAE vehicle. The challenge was to ensure that the new design would not only reduce the weight of the entire wing package but also ensure that it was very strong and stiff to withstand the rigors of racing.
About The Customer
Cyclone Racing is Iowa State University’s Formula SAE team, consisting of over 40 active members who design, build, test, and race a formula style race car each year. The team competes with approximately 80 teams from seven different countries at the Formula Lincoln event and about 30 different teams at the Formula North event. Cyclone racing is currently ranked 4th in the United States and 14th in the world out of 550 teams. The team operates largely from private sponsorship with support from Iowa State University. They are evaluated and judged on most aspects of being a professional racing team, including their working knowledge in engineering and marketing through a series of presentation events.
The Solution
The team turned to solidThinking Inspire, a simulation tool, to generate a new design concept for the mount in the initial phases of the concept design process. The tool was used to create an initial design space for the brackets in an external CAD tool. After running through a number of different iterations in Inspire, the team was able to select a final optimized design for the bracket. The design was then simulated and analyzed using Inspire and third-party analysis and verification tools to ensure the performance of the part. Once the design was verified, the team moved into the manufacturing process where the new brackets were manufactured using waterjet cutting, a quick and cost-effective method.
Operational Impact
Quantitative Benefit
Related Case Studies.
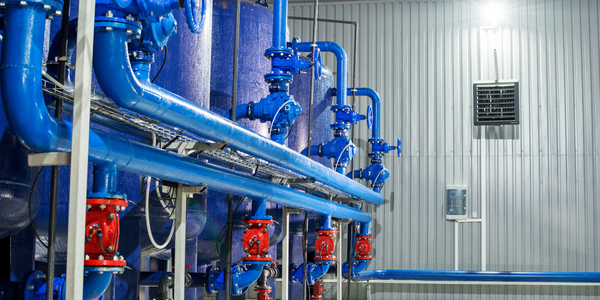
Case Study
Smart Water Filtration Systems
Before working with Ayla Networks, Ozner was already using cloud connectivity to identify and solve water-filtration system malfunctions as well as to monitor filter cartridges for replacements.But, in June 2015, Ozner executives talked with Ayla about how the company might further improve its water systems with IoT technology. They liked what they heard from Ayla, but the executives needed to be sure that Ayla’s Agile IoT Platform provided the security and reliability Ozner required.
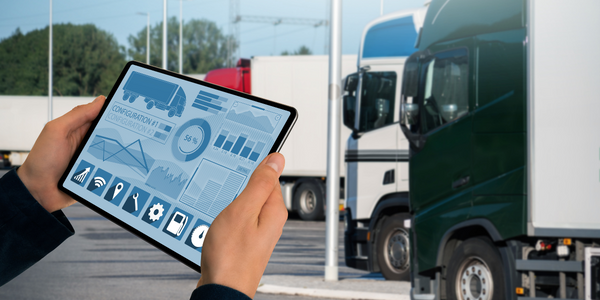
Case Study
IoT enabled Fleet Management with MindSphere
In view of growing competition, Gämmerler had a strong need to remain competitive via process optimization, reliability and gentle handling of printed products, even at highest press speeds. In addition, a digitalization initiative also included developing a key differentiation via data-driven services offers.
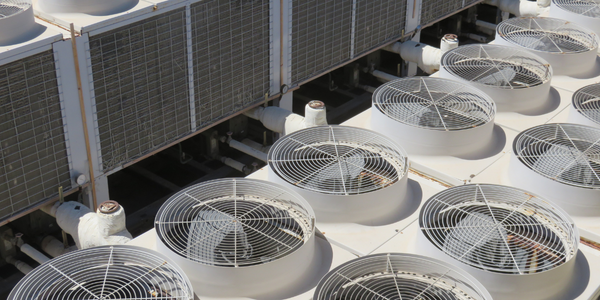
Case Study
Predictive Maintenance for Industrial Chillers
For global leaders in the industrial chiller manufacturing, reliability of the entire production process is of the utmost importance. Chillers are refrigeration systems that produce ice water to provide cooling for a process or industrial application. One of those leaders sought a way to respond to asset performance issues, even before they occur. The intelligence to guarantee maximum reliability of cooling devices is embedded (pre-alarming). A pre-alarming phase means that the cooling device still works, but symptoms may appear, telling manufacturers that a failure is likely to occur in the near future. Chillers who are not internet connected at that moment, provide little insight in this pre-alarming phase.
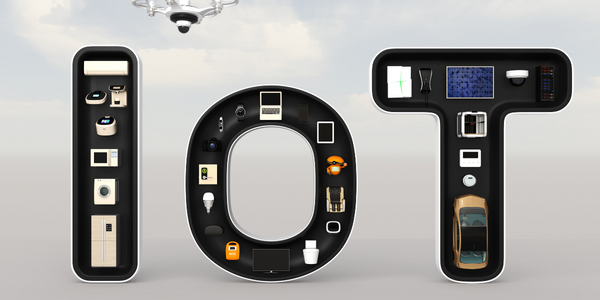
Case Study
Premium Appliance Producer Innovates with Internet of Everything
Sub-Zero faced the largest product launch in the company’s history:It wanted to launch 60 new products as scheduled while simultaneously opening a new “greenfield” production facility, yet still adhering to stringent quality requirements and manage issues from new supply-chain partners. A the same time, it wanted to increase staff productivity time and collaboration while reducing travel and costs.
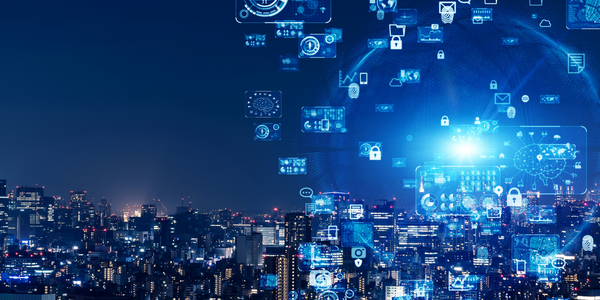
Case Study
Integration of PLC with IoT for Bosch Rexroth
The application arises from the need to monitor and anticipate the problems of one or more machines managed by a PLC. These problems, often resulting from the accumulation over time of small discrepancies, require, when they occur, ex post technical operations maintenance.
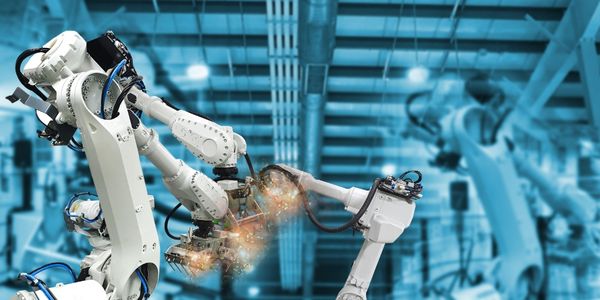
Case Study
Robot Saves Money and Time for US Custom Molding Company
Injection Technology (Itech) is a custom molder for a variety of clients that require precision plastic parts for such products as electric meter covers, dental appliance cases and spools. With 95 employees operating 23 molding machines in a 30,000 square foot plant, Itech wanted to reduce man hours and increase efficiency.