Download PDF
Isitu: Simplifying Financial Reporting for SMEs with IoT
Applicable Industries
- Cement
- Finance & Insurance
Use Cases
- Leasing Finance Automation
The Challenge
The founder of Isitu, Thomas Yeddou, identified a significant challenge faced by small and medium enterprises (SMEs) - understanding their financial situation. Many SMEs struggle to get a clear and precise vision of their finances, which can lead to uncertainty and lack of confidence with financial partners. This lack of clarity can also hinder the ability to plan and prepare for the future. The process of obtaining a complete financial statement of a company can be time-consuming and complex. Furthermore, Thomas, an ex-corporate banker, wanted to start his business and launch an app but had no knowledge about coding.
About The Customer
Isitu's primary customers are small and medium enterprises (SMEs). These businesses often struggle with understanding their financial situation, which can lead to uncertainty and lack of confidence with financial partners. They need a quick and easy way to get a clear and precise vision of their finances. Isitu provides this service, offering a complete financial statement in under 48 hours. The app is designed to be user-friendly, with clear explanations of what the service is, why it's beneficial, how it works, and how much it costs. The app also offers free content to help users understand corporate finance better.
The Solution
Thomas discovered Bubble, a no-code tool, and used it to create Isitu. Isitu is an app that simplifies the process of obtaining a financial statement for a company. Users simply need to provide their contact information and an accounting document, and Isitu will provide a complete financial statement in under 48 hours. The app is designed to provide a user-friendly experience with three main parts on the website that explain what the service is, why it's beneficial, how it works, and how much it costs. The app also offers free content to help users understand corporate finance better. Thomas plans to automate all the analysis on the website and create a profile for customers, so they can simply log in and automatically get their financial situation.
Operational Impact
Quantitative Benefit
Related Case Studies.
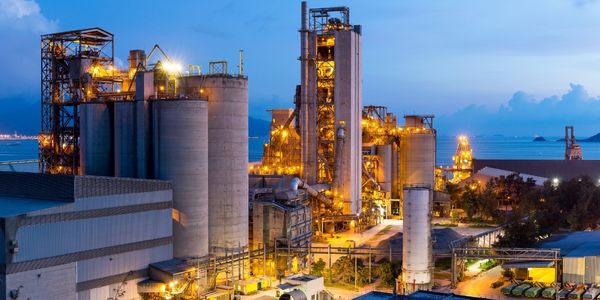
Case Study
System 800xA at Indian Cement Plants
Chettinad Cement recognized that further efficiencies could be achieved in its cement manufacturing process. It looked to investing in comprehensive operational and control technologies to manage and derive productivity and energy efficiency gains from the assets on Line 2, their second plant in India.

Case Study
Real-time In-vehicle Monitoring
The telematic solution provides this vital premium-adjusting information. The solution also helps detect and deter vehicle or trailer theft – as soon as a theft occurs, monitoring personnel can alert the appropriate authorities, providing an exact location.“With more and more insurance companies and major fleet operators interested in monitoring driver behaviour on the grounds of road safety, efficient logistics and costs, the market for this type of device and associated e-business services is growing rapidly within Italy and the rest of Europe,” says Franco.“The insurance companies are especially interested in the pay-per-use and pay-as-you-drive applications while other organisations employ the technology for road user charging.”“One million vehicles in Italy currently carry such devices and forecasts indicate that the European market will increase tenfold by 2014.However, for our technology to work effectively, we needed a highly reliable wireless data network to carry the information between the vehicles and monitoring stations.”

Case Study
Safety First with Folksam
The competitiveness of the car insurance market is driving UBI growth as a means for insurance companies to differentiate their customer propositions as well as improving operational efficiency. An insurance model - usage-based insurance ("UBI") - offers possibilities for insurers to do more efficient market segmentation and accurate risk assessment and pricing. Insurers require an IoT solution for the purpose of data collection and performance analysis

Case Study
Smooth Transition to Energy Savings
The building was equipped with four end-of-life Trane water cooled chillers, located in the basement. Johnson Controls installed four York water cooled centrifugal chillers with unit mounted variable speed drives and a total installed cooling capacity of 6,8 MW. Each chiller has a capacity of 1,6 MW (variable to 1.9MW depending upon condenser water temperatures). Johnson Controls needed to design the equipment in such way that it would fit the dimensional constraints of the existing plant area and plant access route but also the specific performance requirements of the client. Morgan Stanley required the chiller plant to match the building load profile, turn down to match the low load requirement when needed and provide an improvement in the Energy Efficiency Ratio across the entire operating range. Other requirements were a reduction in the chiller noise level to improve the working environment in the plant room and a wide operating envelope coupled with intelligent controls to allow possible variation in both flow rate and temperature. The latter was needed to leverage increased capacity from a reduced number of machines during the different installation phases and allow future enhancement to a variable primary flow system.
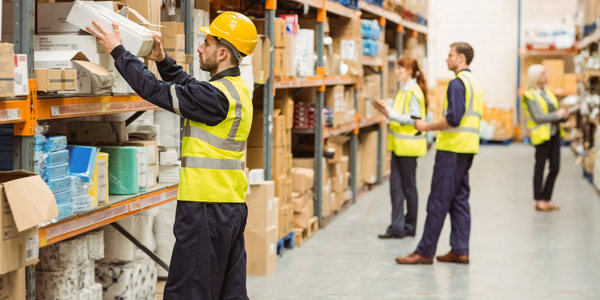
Case Study
Automated Pallet Labeling Solution for SPR Packaging
SPR Packaging, an American supplier of packaging solutions, was in search of an automated pallet labeling solution that could meet their immediate and future needs. They aimed to equip their lines with automatic printer applicators, but also required a solution that could interface with their accounting software. The challenge was to find a system that could read a 2D code on pallets at the stretch wrapper, track the pallet, and flag any pallets with unread barcodes for inspection. The pallets could be single or double stacked, and the system needed to be able to differentiate between the two. SPR Packaging sought a system integrator with extensive experience in advanced printing and tracking solutions to provide a complete traceability system.