Download PDF
Leading Motorsport Team Leverages IoT for Efficient Racecar Design
Technology Category
- Cybersecurity & Privacy - Intrusion Detection
- Sensors - Autonomous Driving Sensors
Applicable Industries
- Automotive
- Chemicals
Applicable Functions
- Product Research & Development
- Quality Assurance
Use Cases
- Smart Parking
- Vehicle-to-Infrastructure
Services
- Testing & Certification
The Challenge
Team Penske, a leading name in American motorsports, faced a significant challenge when they decided to enter the Indy Racing League (IRL) on a full-time basis. The IRL has stringent rules that govern the construction of cars competing in the league. The design team, led by Technical Director Nigel Beresford, had to work within very tight body-design criteria and were limited in what they could change. Major alterations were impossible as competing cars had to use chassis from one of three manufacturers and the same gearbox. Adding to the complexity was the time factor. There was only a five-month window between seasons, and the car had to arrive at the first race tested and ready to win. The design changes were also very restricted during the off-season, and the cars had to be ready by January for testing. The team had no time for back-up plans or mistakes and had to get the design right the first time to give the team optimum performance.
About The Customer
Team Penske is a renowned name in American motorsports, racing and winning in the U.S. since 1958. After 45 years of racing, with 115 Indy car wins, including a record 12 Indy 500 victories, Team Penske embarked on a new and exciting challenge of entering the Indy Racing League (IRL) on a full-time basis. This meant competing with different equipment on 15 different tracks. The design team, led by Technical Director Nigel Beresford, is an eight-strong team that combines a healthy mix of recent graduates and experienced racecar designers. The team operates under a new set of stringent rules that govern the construction of cars competing in the IRL.
The Solution
To overcome these challenges, the design team used Pro/ENGINEER as their primary design program running on HP C3700 hardware with ANSYS finite element analysis (FEA) for testing design changes. ANSYS significantly shortened time-to-market by allowing engineers to utilize basic analysis capabilities during the design phase of product or part development. The program provided designers with access to the same underlying analysis techniques that would be deployed later for detailed product certification, enabling them to make early, intelligent decisions about design, materials, and manufacturing. Using ANSYS, the racecar was broken down into many small simple blocks known as elements. The behavior of each individual element was described with a relatively simple set of equations. The software was then used to solve this large set of simultaneous equations. From this solution, FEA software could extract the behavior of the individual elements. This method was the only proven way to deal with complex boundaries and provided efficient solutions to “real world” physics-based problems.
Operational Impact
Quantitative Benefit
Related Case Studies.
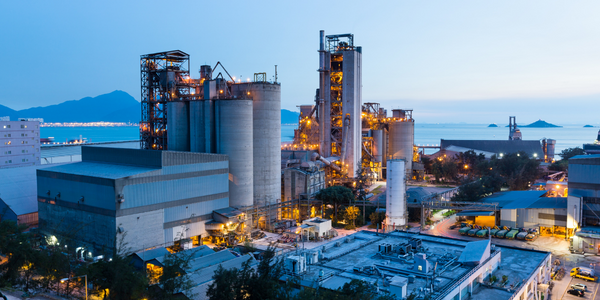
Case Study
Honeywell - Tata Chemicals Improves Data Accessibility with OneWireless
Tata was facing data accessibility challenges in the cement plant control room tapping signals from remote process control areas and other distant locations, including the gas scrubber. Tata needed a wireless solution to extend its control network securely to remote locations that would also provide seamless communication with existing control applications.
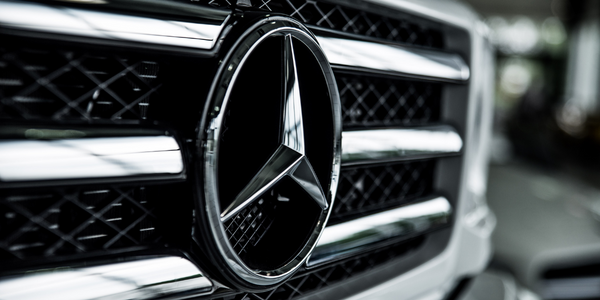
Case Study
Integral Plant Maintenance
Mercedes-Benz and his partner GAZ chose Siemens to be its maintenance partner at a new engine plant in Yaroslavl, Russia. The new plant offers a capacity to manufacture diesel engines for the Russian market, for locally produced Sprinter Classic. In addition to engines for the local market, the Yaroslavl plant will also produce spare parts. Mercedes-Benz Russia and his partner needed a service partner in order to ensure the operation of these lines in a maintenance partnership arrangement. The challenges included coordinating the entire maintenance management operation, in particular inspections, corrective and predictive maintenance activities, and the optimizing spare parts management. Siemens developed a customized maintenance solution that includes all electronic and mechanical maintenance activities (Integral Plant Maintenance).
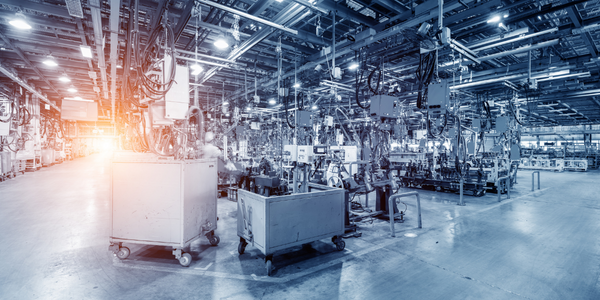
Case Study
Advanced Elastomer Systems Upgrades Production
In order to maintain its share of the international market for thermoplastic elastomers AES recently expanded its Florida plant by adding a new production line. While the existing lines were operating satisfactorily using a PROVOX distributed control system with traditional analog I/O, AES wanted advanced technology on the new line for greater economy, efficiency, and reliability. AES officials were anxious to get this line into production to meet incoming orders, but two hurricanes slowed construction.