Download PDF
Making the perfect game possible: Revolutionizing the baseball glove with industrial-grade additive manufacturing
Technology Category
- Other - Additive Manufacturing
Applicable Industries
- Consumer Goods
Applicable Functions
- Product Research & Development
Use Cases
- Additive Manufacturing
- Rapid Prototyping
Services
- Cloud Planning, Design & Implementation Services
- Hardware Design & Engineering Services
The Challenge
Rawlings, a company with over 150 years of experience in the baseball industry, aimed to revolutionize the baseball glove by developing the REV1X. The glove leverages the Carbon Digital Light Synthesis (DLS) process to improve gameplay and speed up reaction times. The traditional foam or wool parts in the glove’s thumb and pinky were replaced with latticed pieces, made from FPU 50, that are lighter and thinner. The REV1X lattices are tuned with variable stiffness that better conforms to the player’s hand, leading to better control of the ball. Additionally, the REV1X is ready for gameplay immediately, and it’s more durable and long-lasting than traditional gloves. Once Rawlings perfected the design for the REV1X, they needed to mass produce a glove that would meet their exacting standards for performance and durability on the field.
About The Customer
Rawlings is a company with a long history in the baseball business, having been in operation for more than 150 years. They are known for outfitting both amateurs and professionals with their high-quality baseball equipment. Their expertise and reputation for quality are unmatched in the industry. Rawlings is committed to innovation and is always looking for ways to improve their products. Their latest project, the REV1X baseball glove, represents a major transformation in an industry that has been slow to innovate. The REV1X glove is designed to improve gameplay and speed up reaction times, making it a game-changer in the world of baseball.
The Solution
Rawlings partnered with Fast Radius to scale up production of the REV1X glove. Fast Radius had the expansive production capacity and skilled manufacturing engineers who were able to adjust the inserts for manufacturability. This expertise was especially valuable in dealing with FPU 50, which provides the perfect level of stiffness for the glove but presents challenges with yield on the finely tuned latticed parts. The experts at Fast Radius developed a solution to make sure the parts printed reliably every time. Every piece of information needed to make the parts — from the design files, to custom post-processing methods, to fulfillment instructions — is stored in a build package in the Fast Radius Cloud Manufacturing Platform so the parts can be made perfectly today, next week, next year, and beyond. Fast Radius was able to dial in the printing process and develop specific post-processing methods that preserve the tight tolerances needed for the inserts’ finely tuned lattice structures. Ultimately, they improved part yield by more than 4x from initial tests.
Operational Impact
Quantitative Benefit
Related Case Studies.
.png)
Case Study
Improving Vending Machine Profitability with the Internet of Things (IoT)
The vending industry is undergoing a sea change, taking advantage of new technologies to go beyond just delivering snacks to creating a new retail location. Intelligent vending machines can be found in many public locations as well as company facilities, selling different types of goods and services, including even computer accessories, gold bars, tickets, and office supplies. With increasing sophistication, they may also provide time- and location-based data pertaining to sales, inventory, and customer preferences. But at the end of the day, vending machine operators know greater profitability is driven by higher sales and lower operating costs.
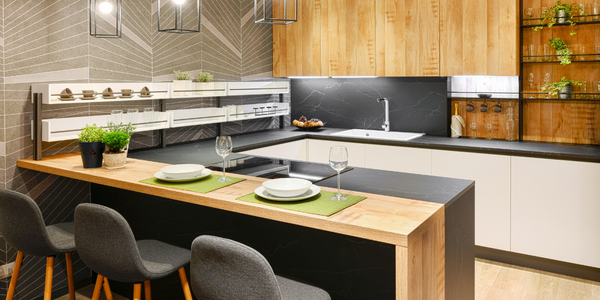
Case Study
Series Production with Lot-size-1 Flexibility
Nobilia manufactures customized fitted kitchens with a lot size of 1. They require maximum transparency of tracking design data and individual processing steps so that they can locate a particular piece of kitchen furniture in the sequence of processes.
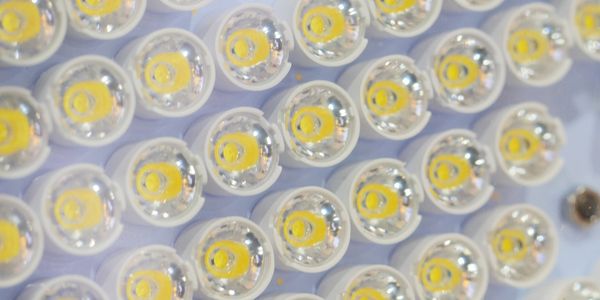
Case Study
American Eagle Achieves LEED with GE LED Lighting Fixtures
American Eagle Outfitters (AEO) was in the process of building a new distribution center. The AEO facility management team decided to look at alternate options for lighting layout that could provide energy and maintenance savings. AEO would need a full-time maintenance employee just to replace burned-out fluorescent tubes.
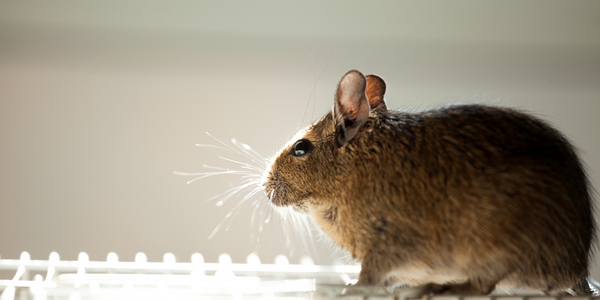
Case Study
Revolutionizing Rodent Control
From pet- and child-safe traps, to touch-free and live-catch rodent control solutions, Victor continues to stay committed to producing superior products that meet the varying needs of today’s pest control professionals. And, with a long standing history supporting customers in the food processing, service, and retail settings, Victor knew that strict regulations were costing organizations thousands of dollars in excess overhead trying to manage their rodent-control solutions. Trap inspections in these environments are often difficult and time consuming, requiring personnel to manually check a trap’s status multiple times per day, amounting to over six hours of manual labor. Victor is looking for an innovative way to increase operational efficiencies with the use of technology.