Download PDF
Mirage Machines Enhances Simulation Capability with ANSYS
Technology Category
- Analytics & Modeling - Digital Twin / Simulation
- Robots - Gantry Robots
Applicable Industries
- Construction & Infrastructure
- Mining
Applicable Functions
- Product Research & Development
Use Cases
- Digital Twin
- Virtual Reality
The Challenge
Mirage Machines, a manufacturer of portable machines for various industries, was facing a challenge in their design process. They were using detailed structural simulation at the front end of the design process to ensure the robustness and risk-free nature of their solutions. However, the Finite Element Analysis (FEA) simulation they were using, SolidWorks® Professional and Premium packages, had limitations. These packages only allowed Mirage to conduct FEA on single parts and small assembly models. A recent project required the development of a gantry that used a series of magnets to attach steel rails. The initial design was to be base metal, but the requirement changed to include a layer of paint. This change introduced an air gap, reducing the magnets' pull force by 40 percent. Mirage needed to understand the impact of the paint thickness on the pull force of the magnets and the integrity of the structure as the arms moved along the base rail.
About The Customer
Mirage Machines is a manufacturer of a wide variety of portable machines. They cater to several industries including oil, gas, power generation, ship build and repair, mining, and construction. Their machines cover a range of applications such as hot tapping, drilling, tapping, milling, pipe and casing cutting, line boring, and bespoke requirements. They are known for their commitment to providing robust and risk-free solutions to their clients, using detailed structural simulation at the front end of the design process.
The Solution
To overcome the limitations of their existing FEA software, Mirage Machines turned to ANSYS® Professional™ NLS, ANSYS geometry interface for SolidWorks, and ANSYS® DesignModeler™. The first step was to import the geometry for the gantry assembly from Solidworks into ANSYS DesignModeler. Then, DesignModeler was employed to prepare the geometry for simulation. Finally, the simulation was performed on the assembly of mixed materials, body types, and mesh types using ANSYS structural dynamics software. This solution greatly improved both the accuracy and the performance of the simulation, allowing the company to increase throughput and reduce risk in the design of the gantry.
Operational Impact
Quantitative Benefit
Related Case Studies.
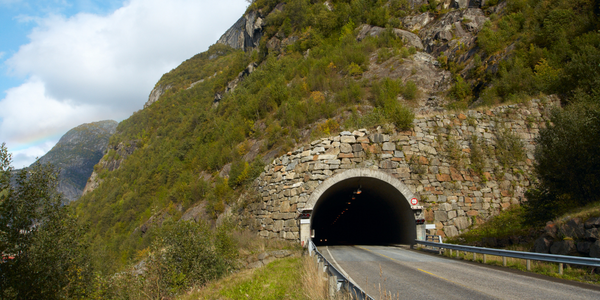
Case Study
IoT System for Tunnel Construction
The Zenitaka Corporation ('Zenitaka') has two major business areas: its architectural business focuses on structures such as government buildings, office buildings, and commercial facilities, while its civil engineering business is targeted at structures such as tunnels, bridges and dams. Within these areas, there presented two issues that have always persisted in regard to the construction of mountain tunnels. These issues are 'improving safety" and "reducing energy consumption". Mountain tunnels construction requires a massive amount of electricity. This is because there are many kinds of electrical equipment being used day and night, including construction machinery, construction lighting, and ventilating fan. Despite this, the amount of power consumption is generally not tightly managed. In many cases, the exact amount of power consumption is only ascertained when the bill from the power company becomes available. Sometimes, corporations install demand-monitoring equipment to help curb the maximum power demanded. However, even in these cases, the devices only allow the total volume of power consumption to be ascertained, or they may issue warnings to prevent the contracted volume of power from being exceeded. In order to tackle the issue of reducing power consumption, it was first necessary to obtain an accurate breakdown of how much power was being used in each particular area. In other words, we needed to be able to visualize the amount of power being consumed. Safety, was also not being managed very rigorously. Even now, tunnel construction sites often use a 'name label' system for managing entry into the work site. Specifically, red labels with white reverse sides that bear the workers' names on both sides are displayed at the tunnel work site entrance. The workers themselves then flip the name label to the appropriate side when entering or exiting from the work site to indicate whether or not they are working inside the tunnel at any given time. If a worker forgets to flip his or her name label when entering or exiting from the tunnel, management cannot be performed effectively. In order to tackle the challenges mentioned above, Zenitaka decided to build a system that could improve the safety of tunnel construction as well as reduce the amount of power consumed. In other words, this new system would facilitate a clear picture of which workers were working in each location at the mountain tunnel construction site, as well as which processes were being carried out at those respective locations at any given time. The system would maintain the safety of all workers while also carefully controlling the electrical equipment to reduce unnecessary power consumption. Having decided on the concept, our next concern was whether there existed any kind of robust hardware that would not break down at the construction work site, that could move freely in response to changes in the working environment, and that could accurately detect workers and vehicles using radio frequency identification (RFID). Given that this system would involve many components that were new to Zenitaka, we decided to enlist the cooperation of E.I.Sol Co., Ltd. ('E.I.Sol') as our joint development partner, as they had provided us with a highly practical proposal.
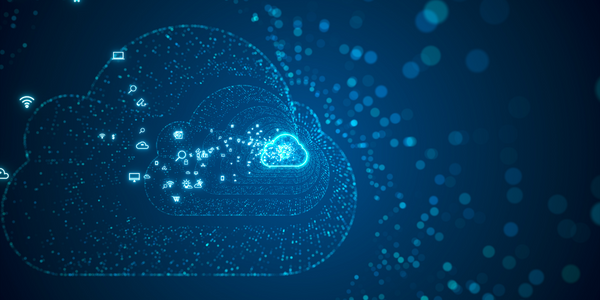
Case Study
Splunk Partnership Ties Together Big Data & IoT Services
Splunk was faced with the need to meet emerging customer demands for interfacing IoT projects to its suite of services. The company required an IoT partner that would be able to easily and quickly integrate with its Splunk Enterprise platform, rather than allocating development resources and time to building out an IoT interface and application platform.
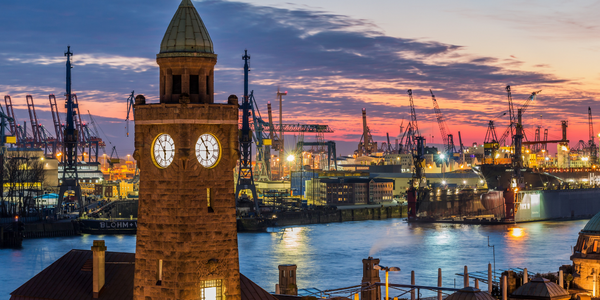
Case Study
Bridge monitoring in Hamburg Port
Kattwyk Bridge is used for both rail and road transport, and it has played an important role in the Port of Hamburg since 1973. However, the increasing pressure from traffic requires a monitoring solution. The goal of the project is to assess in real-time the bridge's status and dynamic responses to traffic and lift processes.
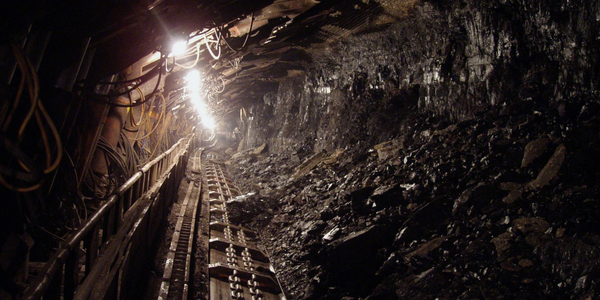
Case Study
Underground Mining Safety
The goal was to produce a safety system to monitor and support underground mining operations; existing systems were either too simple (i.e. phone line) or overly complex and expensive, inhibiting deployment, and providing little-to-no support in event of an accident. Given the dangerous nature of the mining work environment and the strict regulations placed on the industry, the solution would have to comply with Mine Safety and Health Administration (MSHA) regulations. Yet the product needed to allow for simple deployment to truly be a groundbreaking solution - increasing miner safety and changing daily operations for the better.
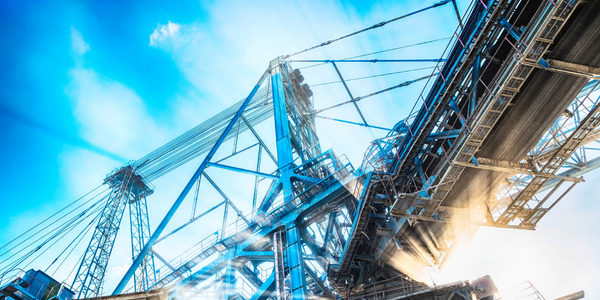
Case Study
Mining Firm Quadruples Production, with Internet of Everything
Dundee Precious Metal’s flagship mine, in Chelopech, Bulgaria, produces a gold, copper, and silver concentrate set a goal to increase production by 30%. Dundee wanted to increase production quality and output without increasing headcount and resources, improve miner safety, and minimize cost.
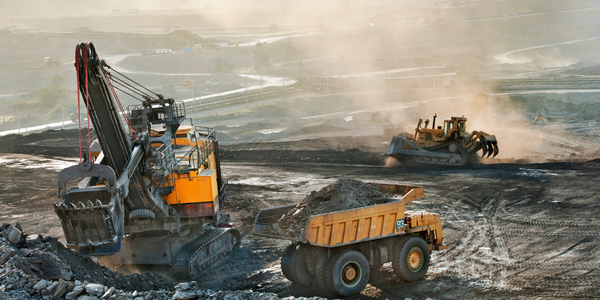
Case Study
Fastenal Builds the Future of Manufacturing with MachineMetrics
Fastenal's objective was to better understand their machine downtime, utilization, quality issues, and to embrace cutting-edge manufacturing technology/process improvement capabilities to bring their team to the next level. However, there was a lack of real-time data, visualization, and actionable insights made this transition impossible.