Download PDF
Miti takes control of leather cutting with Lectra’s Versalis
Technology Category
- Automation & Control - Automation & Process Control Systems
- Functional Applications - Manufacturing Execution Systems (MES)
Applicable Functions
- Quality Assurance
Use Cases
- Manufacturing System Automation
- Process Control & Optimization
Services
- System Integration
- Training
The Challenge
Miti wanted to gain control over hide consumption, reduce operational costs, and ensure the quality of cut pieces by incorporating leather cutting into the in-house production process. Previously, Miti designed and assembled products in-house and subcontracted the leather cutting. However, outsourcing leather cutting resulted in a loss of control over quality and material consumption which, given the high quality of the hides, was very costly. These issues spurred Miti’s management team to consider overhauling its production processes to include leather cutting.
About The Customer
Since its founding in 1992, Miti has risen to become the manufacturer of choice for premium furniture brands around the world thanks to its combination of craftsmanship and innovative design. Combining creativity, passion, and innovative design techniques, Miti provides high quality, elegant upholstered furnishings to some of the world’s most famous, high-end brands. As a furniture supplier to the world’s top brands, Miti cannot compromise on quality standards or compliance with delivery times. The company prides itself on offering products that provide excellent value for money.
The Solution
Lectra proposed the Versalis® automated leather-cutting solution, which enables the company to meet tight deadlines, ensure maximum hide efficiency, and high-quality cut pieces. Lectra carried out a careful analysis of the impact in-house cutting would have for Miti in terms of hides cut per day, cut quality, and running costs. A visit to Lectra’s International Advanced Technology Center also allowed the opportunity to run cutting tests on Versalis® using Miti’s own hides. The results of automatic nesting tests and Versalis’ high cut quality convinced Miti executives of the value a Versalis cutting room would bring. Lectra experts will support Miti for the duration of this important project to ensure that the company maintains its results over the long term.
Operational Impact
Quantitative Benefit
Related Case Studies.
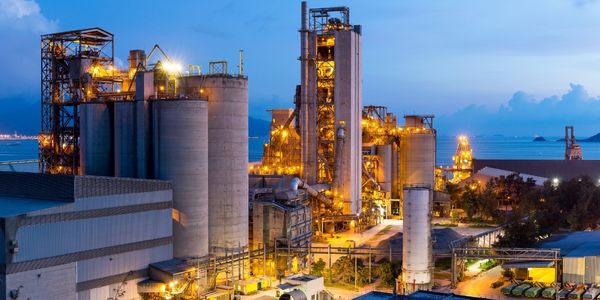
Case Study
System 800xA at Indian Cement Plants
Chettinad Cement recognized that further efficiencies could be achieved in its cement manufacturing process. It looked to investing in comprehensive operational and control technologies to manage and derive productivity and energy efficiency gains from the assets on Line 2, their second plant in India.
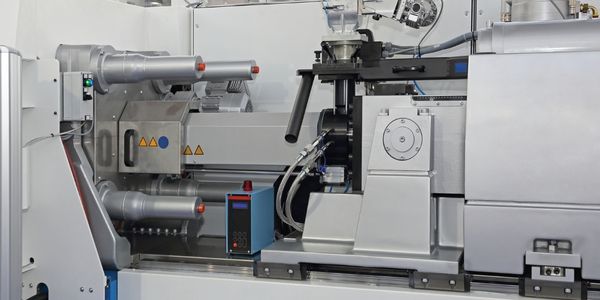
Case Study
Plastic Spoons Case study: Injection Moulding
In order to meet customer expectations by supplying a wide variety of packaging units, from 36 to 1000 spoons per package, a new production and packaging line needed to be built. DeSter wanted to achieve higher production capacity, lower cycle time and a high degree of operator friendliness with this new production line.
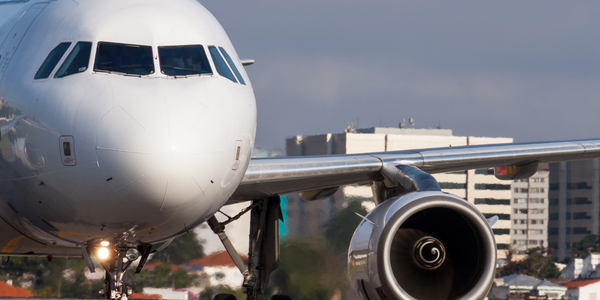
Case Study
Airbus Soars with Wearable Technology
Building an Airbus aircraft involves complex manufacturing processes consisting of thousands of moving parts. Speed and accuracy are critical to business and competitive advantage. Improvements in both would have high impact on Airbus’ bottom line. Airbus wanted to help operators reduce the complexity of assembling cabin seats and decrease the time required to complete this task.
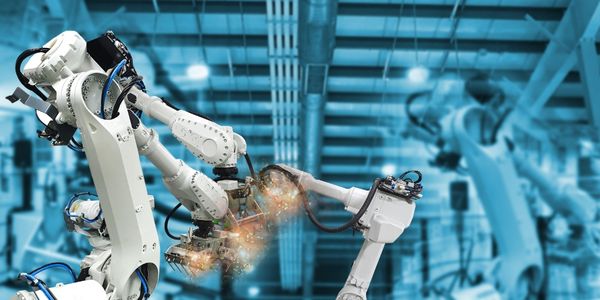
Case Study
Robot Saves Money and Time for US Custom Molding Company
Injection Technology (Itech) is a custom molder for a variety of clients that require precision plastic parts for such products as electric meter covers, dental appliance cases and spools. With 95 employees operating 23 molding machines in a 30,000 square foot plant, Itech wanted to reduce man hours and increase efficiency.
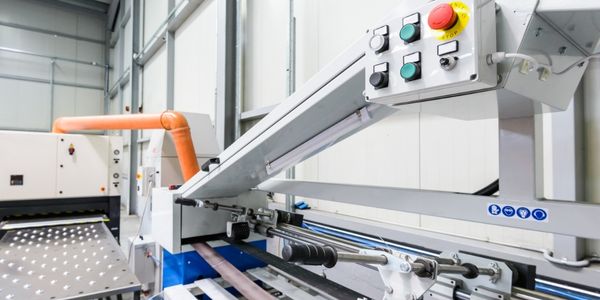
Case Study
Fully Automated Visual Inspection System
Tofflon has developed a fully automatic machine that uses light to inspect vials, medicine bottles, or infusion containers for glass fragments, aluminum particles, rubber grains, hairs, fibers, or other contaminants. It also detects damaged containers with cracks or inclusions (microscopic imperfections), automatically removing faulty or contaminated products. In order to cover all production processes for freeze-dried pharmaceuticals, Tofflon needed to create an open, consistent, and module-based automation concept.