Download PDF
Multi-plant Packaging Company Drives Revenue Improvement by Boosting Line Speeds 15-20% Over Name Plate Capacity
Technology Category
- Analytics & Modeling - Real Time Analytics
- Application Infrastructure & Middleware - Data Visualization
- Functional Applications - Enterprise Resource Planning Systems (ERP)
Applicable Industries
- Packaging
Applicable Functions
- Business Operation
- Quality Assurance
Use Cases
- Predictive Maintenance
- Process Control & Optimization
- Real-Time Location System (RTLS)
Services
- Software Design & Engineering Services
- System Integration
The Challenge
The Senior Quality Manager for a multi-plant packaging company faced a significant performance gap between plants, with lower-performing facilities lagging by as much as 20% on key indicators such as line speed and quality levels. This disparity made it difficult to support the company's drive for a more flexible supply chain, as disparate systems hindered the ability to move products between plants to handle urgent orders. The underlying cause was identified as the use of different quality software systems and a lack of necessary infrastructure in poorer-performing facilities. The Chief Information Officer also recognized the need to standardize quality systems across newly acquired plants to minimize the cost of ownership and streamline support, despite anticipated resistance from staff.
About The Customer
The customer is a multi-plant packaging company that operates several manufacturing facilities. The company aims to harmonize quality and productivity across all its plants to create a more flexible supply chain capable of handling fluctuating demand. The Senior Quality Manager and Chief Information Officer play crucial roles in driving this initiative. The company has recently acquired six new plants, which are using different quality software systems, leading to performance gaps and inefficiencies. The company is committed to improving its operational efficiency, customer service, and overall productivity by standardizing its quality systems and leveraging real-time data collection and analysis.
The Solution
The solution involved deploying the GainSeeker Suite across all plants to standardize quality systems and enable real-time data collection. GainSeeker connects directly to digital equipment, saving time and eliminating clerical errors. Customized alarms and dashboards were implemented to help operators manage production quality and material use more effectively. The system provides color-coded alerts to guide operators on necessary actions and ties this information to employee performance bonuses. The deployment also included customized dashboards for weight tracking to compare material use against specifications, ensuring compliance and cost management. The CIO and Quality Manager leveraged their past successes with GainSeeker Suite to drive the adoption of the system across all plants, despite initial resistance from staff.
Operational Impact
Quantitative Benefit
Related Case Studies.
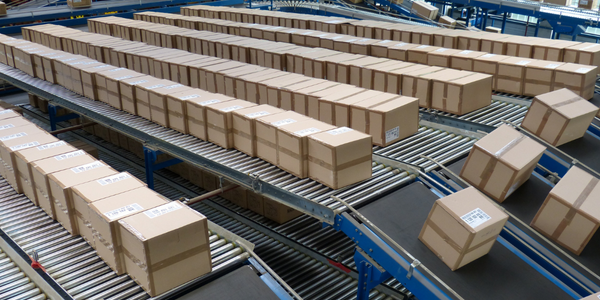
Case Study
IoT Data Analytics Case Study - Packaging Films Manufacturer
The company manufactures packaging films on made to order or configure to order basis. Every order has a different set of requirements from the product characteristics perspective and hence requires machine’s settings to be adjusted accordingly. If the film quality does not meet the required standards, the degraded quality impacts customer delivery causes customer dissatisfaction and results in lower margins. The biggest challenge was to identify the real root cause and devise a remedy for that.
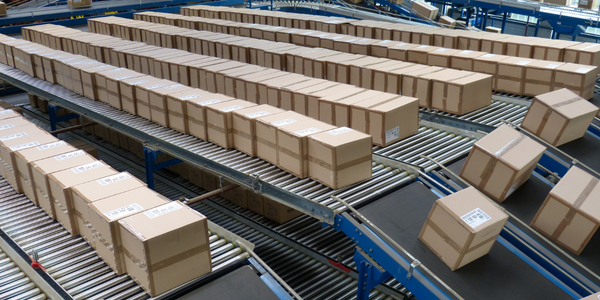
Case Study
Zenon the Ideal Basis for An Ergonomic HMI
KHS develops and produces machines and equipment for filling and packaging in the drinks industry. Because drinks manufacturing, filling and packaging consist of a number of highly complex processes, the user-friendly and intuitive operation of equipment is increasingly gaining in significance. In order to design these processes as simple as possible for the user, KHS decided to introduce a uniform, transparent and standardized solution to the company. The HMI interface should meet the requirement for people with different qualifications and enable them to work on a standard platform.
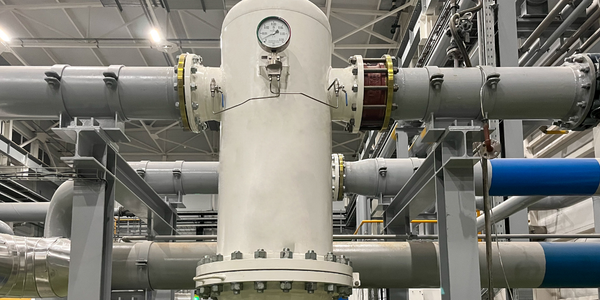
Case Study
Sparks Dynamics Assists Atlas Container Secure a $15,000 BGE Energy Rebate
The ReMASTER Compressed Air Monitoring system was installed in 2015. This system is capable of monitoring compressed air system parameters on a continuous basis and transferring that information to a cloud server which can be accessed by Atlas Container personnel, Industrial Diagnostics and Sparks Dynamics. This information was collected into a database which can be exported to an Excel spreadsheet or displayed graphically using Sparks Dynamics ViewMaster Software. The average annual compressed air electricity expense was estimated to be approximately $116,000. This is based on an incremental $/KWh electric rate of $.091 per KWh and an estimated compressed air energy consumption of 1,279,200 KWH. The implementation phase of Energy Conservation Measures (ECMs) for the Compressed Air System included: • Identification and repair of compressed air leaks • Understanding of compressed air usage per manufacturing machine and installation of shut off valves when the machines are no longer in production mode • Identification of misapplications of compressed air to include blow offs, venturis, and cooling scenarios • Understand system pressure requirements and potential installation of point of use pressure regulation.
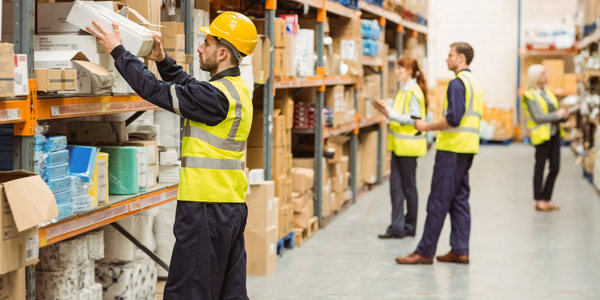
Case Study
Automated Pallet Labeling Solution for SPR Packaging
SPR Packaging, an American supplier of packaging solutions, was in search of an automated pallet labeling solution that could meet their immediate and future needs. They aimed to equip their lines with automatic printer applicators, but also required a solution that could interface with their accounting software. The challenge was to find a system that could read a 2D code on pallets at the stretch wrapper, track the pallet, and flag any pallets with unread barcodes for inspection. The pallets could be single or double stacked, and the system needed to be able to differentiate between the two. SPR Packaging sought a system integrator with extensive experience in advanced printing and tracking solutions to provide a complete traceability system.
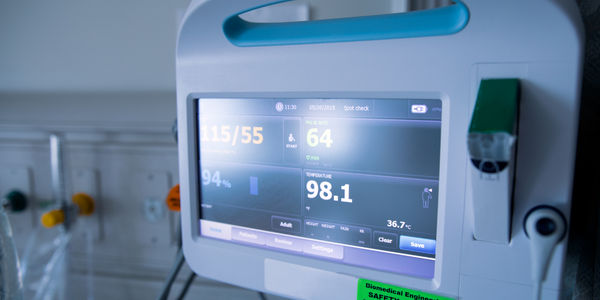
Case Study
Mondi Implements Statistics-Based Health Monitoring and Predictive Maintenance
The extrusion and other machines at Mondi’s plant are large and complex, measuring up to 50 meters long and 15 meters high. Each machine is controlled by up to five programmable logic controllers (PLCs), which log temperature, pressure, velocity, and other performance parameters from the machine’s sensors. Each machine records 300–400 parameter values every minute, generating 7 gigabytes of data daily.Mondi faced several challenges in using this data for predictive maintenance. First, the plant personnel had limited experience with statistical analysis and machine learning. They needed to evaluate a variety of machine learning approaches to identify which produced the most accurate results for their data. They also needed to develop an application that presented the results clearly and immediately to machine operators. Lastly, they needed to package this application for continuous use in a production environment.
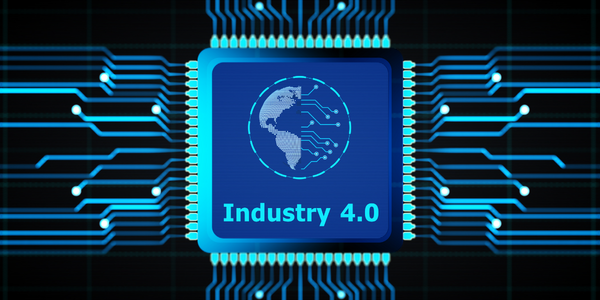
Case Study
Industry 4.0 at ALPLA: Enhancing Factory Efficiency with IoT
ALPLA, a global leader in packaging solutions, faced several challenges as the complexity of their production machinery increased. The need for highly trained specialists in each factory led to higher personnel costs, difficulties in recruiting experienced talent at each location, and costly personnel turnover. Furthermore, less experienced operators running the machines sub-optimally impacted resource consumption and overall equipment effectiveness (OEE). ALPLA also faced the challenge of monitoring visual inspection systems in every line of their plants, which was almost impossible to do manually. In 2016, ALPLA decided to use data from the 900 different types of embedded sensors in each factory to address these issues. However, their initial choice of SQL Server as the data store for the sensor data proved inadequate, as it was unable to cope with their data requirements.