Download PDF
Nabtesco Corporation Industrial Equipment Case Study
Technology Category
- Analytics & Modeling - Digital Twin / Simulation
Applicable Industries
- Renewable Energy
- Equipment & Machinery
Applicable Functions
- Product Research & Development
- Discrete Manufacturing
Use Cases
- Predictive Maintenance
- Digital Twin
Services
- Software Design & Engineering Services
The Challenge
Nabtesco Corporation, a Japanese company known for its unique technology in robotic reduction gears, faced a challenge when expanding into energy harvesting equipment such as wind turbines and solar energy collector trackers. The company needed to ensure sufficient gear strength and long-term endurance in gusty conditions for their wind turbines. The yaw and pitch drives in a wind turbine engage with a pinion gear, which transmits power from the drive to the nacelle or blade. The rotation angle between drive and pinion gear teeth is particularly small, so repeated contact over time, particularly under the stresses of high winds and tower vibration, has the potential to damage tooth surfaces and cause assembly breakdowns. The engineers at Nabtesco needed to balance the contact between ring and pinion teeth to reduce the 'normal' stress of rotation and the sheer stress of the teeth against each other. Decreasing the stress on teeth improves their durability and that of the entire assembly as well.
About The Customer
Nabtesco Corporation is a Japanese company known worldwide for its unique technology that allows robotic reduction gears to be smaller and lighter than many conventional robotic drives. The company specializes in precision yaw and pitch drives for robotic reduction gears. However, when the company expanded into energy harvesting equipment, such as wind turbines and solar energy collector trackers, they realized that 'smaller and lighter' have their limits in large industrial structures. Particularly in the wind industry, their biggest challenges are ensuring sufficient gear strength and long-term endurance in gusty conditions. Their reduction gears are made up of a lot of very complicated assemblies, with many parts that come in contact with one another. For each wind turbine configuration, they have to provide their customers with the best possible design that minimizes overall stress while maintaining durability.
The Solution
The engineers at Nabtesco used Abaqus finite element analysis (FEA) software to calculate the contact area and stress of various pinion gear designs. With the help of their own subroutine, the engineers were able to model both contact area and stress history for easier design evaluation. Isight was also utilized for post-processing automation and design optimization. The engineers started from a global Abaqus/CAE model based on imported CAD geometries of rig, drive, and pinion. The bottom surface of the test apparatus was modeled as fixed. Resistance was applied to the reduction gear shaft, and the pinion was rotated at a prescribed angle. This allowed the team to see when and where the opposing teeth engaged as the gears rotated, and what the resulting stresses were. For a deeper understanding of what happens when the teeth interact, the engineers created a sub model that contained only those areas of acute interest. When compared against the painted gear rig tests, the FEA results showed good agreement.
Operational Impact
Quantitative Benefit
Related Case Studies.
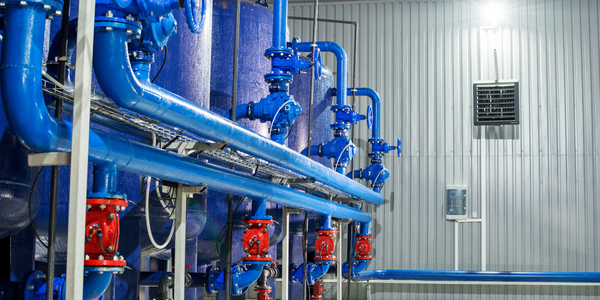
Case Study
Smart Water Filtration Systems
Before working with Ayla Networks, Ozner was already using cloud connectivity to identify and solve water-filtration system malfunctions as well as to monitor filter cartridges for replacements.But, in June 2015, Ozner executives talked with Ayla about how the company might further improve its water systems with IoT technology. They liked what they heard from Ayla, but the executives needed to be sure that Ayla’s Agile IoT Platform provided the security and reliability Ozner required.
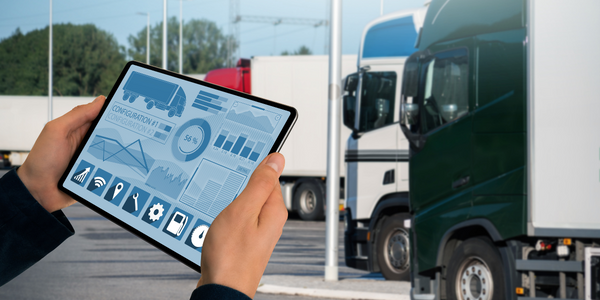
Case Study
IoT enabled Fleet Management with MindSphere
In view of growing competition, Gämmerler had a strong need to remain competitive via process optimization, reliability and gentle handling of printed products, even at highest press speeds. In addition, a digitalization initiative also included developing a key differentiation via data-driven services offers.
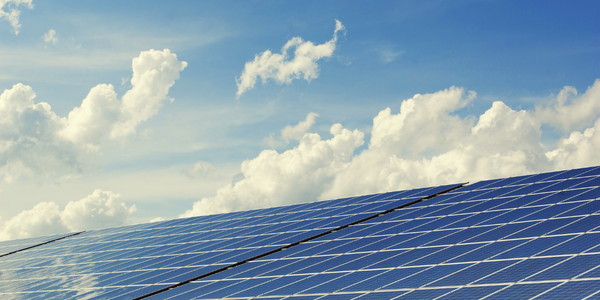
Case Study
Remote Monitoring & Predictive Maintenance App for a Solar Energy System
The maintenance & tracking of various modules was an overhead for the customer due to the huge labor costs involved. Being an advanced solar solutions provider, they wanted to ensure early detection of issues and provide the best-in-class customer experience. Hence they wanted to automate the whole process.
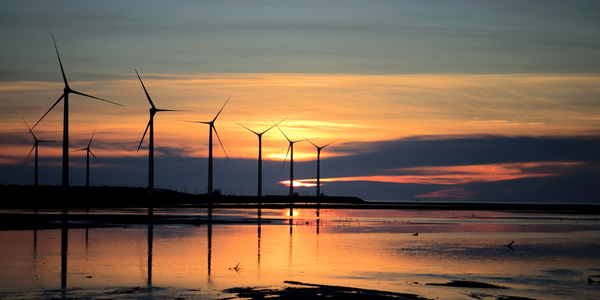
Case Study
Vestas: Turning Climate into Capital with Big Data
Making wind a reliable source of energy depends greatly on the placement of the wind turbines used to produce electricity. Turbulence is a significant factor as it strains turbine components, making them more likely to fail. Vestas wanted to pinpoint the optimal location for wind turbines to maximize power generation and reduce energy costs.
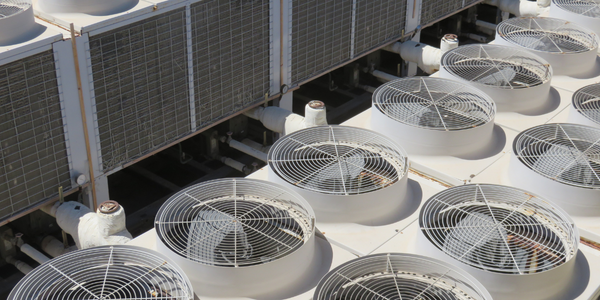
Case Study
Predictive Maintenance for Industrial Chillers
For global leaders in the industrial chiller manufacturing, reliability of the entire production process is of the utmost importance. Chillers are refrigeration systems that produce ice water to provide cooling for a process or industrial application. One of those leaders sought a way to respond to asset performance issues, even before they occur. The intelligence to guarantee maximum reliability of cooling devices is embedded (pre-alarming). A pre-alarming phase means that the cooling device still works, but symptoms may appear, telling manufacturers that a failure is likely to occur in the near future. Chillers who are not internet connected at that moment, provide little insight in this pre-alarming phase.
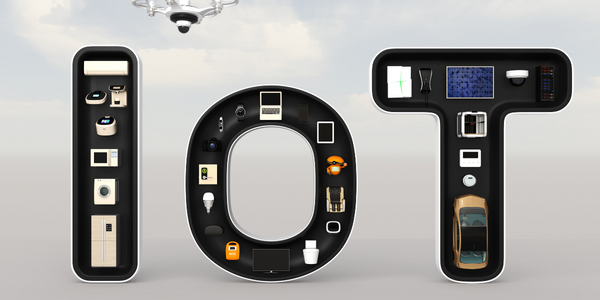
Case Study
Premium Appliance Producer Innovates with Internet of Everything
Sub-Zero faced the largest product launch in the company’s history:It wanted to launch 60 new products as scheduled while simultaneously opening a new “greenfield” production facility, yet still adhering to stringent quality requirements and manage issues from new supply-chain partners. A the same time, it wanted to increase staff productivity time and collaboration while reducing travel and costs.