Download PDF
Not Sitting Still
Technology Category
- Functional Applications - Enterprise Resource Planning Systems (ERP)
- Functional Applications - Warehouse Management Systems (WMS)
- Automation & Control - Automation & Process Control Systems
Applicable Functions
- Warehouse & Inventory Management
- Logistics & Transportation
Use Cases
- Warehouse Automation
- Inventory Management
- Process Control & Optimization
Services
- System Integration
- Hardware Design & Engineering Services
The Challenge
In building a new warehouse and production facility, 9 to 5 Seating aimed to create capacity to quadruple production in a new production and warehouse facility that is LEED Gold® certified. The company needed an innovative material handling scheme to achieve this goal. The challenge was to design a system that could handle increased production while maintaining efficiency and reducing the number of touches per product. The company partnered with Raymond Handling Solutions to design and implement the new facility, leveraging their expertise in storage and material handling.
About The Customer
9 to 5 Seating specializes in the design and manufacture of office seating for a diverse range of customers, including major companies, schools, hospitals, and small businesses. The company offers a wide selection of product designs and upholstery materials through a combination of global and domestic production. All products are made to order and ship within 48 hours. The company is committed to increasing production capacity and efficiency, which led to the collaboration with Raymond Handling Solutions for the new facility.
The Solution
Raymond Handling Solutions, a Sales and Service Center of The Raymond Corporation, designed a U-shaped material flow for the new facility. The system includes automated conveyors, a sophisticated order-picking system, and a very narrow aisle (VNA) raw material storage system. The circulation consists of lift trucks receiving incoming raw materials and components, feeding the VNA racking system, delivering components to the pick module, and moving finished goods to shipping. The handling process interfaces with the Enterprise Resource Planning (ERP) system, allowing company personnel to track the status of orders from assembly through shipping. The system also includes Raymond® Model 4250 stand-up counterbalanced electric lift trucks, Raymond Swing-Reach® trucks, Raymond Model 8400 pallet trucks, and Raymond Model 7400 Reach-Fork® trucks.
Operational Impact
Quantitative Benefit
Related Case Studies.
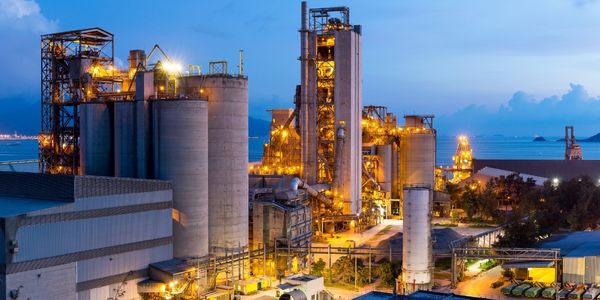
Case Study
System 800xA at Indian Cement Plants
Chettinad Cement recognized that further efficiencies could be achieved in its cement manufacturing process. It looked to investing in comprehensive operational and control technologies to manage and derive productivity and energy efficiency gains from the assets on Line 2, their second plant in India.
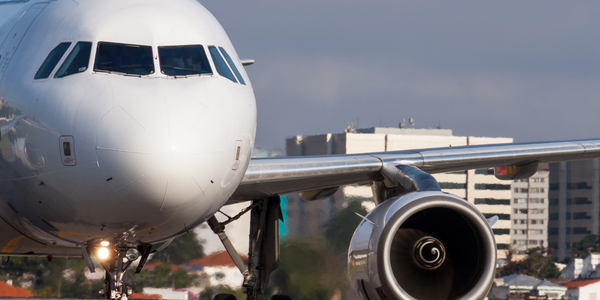
Case Study
Airbus Soars with Wearable Technology
Building an Airbus aircraft involves complex manufacturing processes consisting of thousands of moving parts. Speed and accuracy are critical to business and competitive advantage. Improvements in both would have high impact on Airbus’ bottom line. Airbus wanted to help operators reduce the complexity of assembling cabin seats and decrease the time required to complete this task.
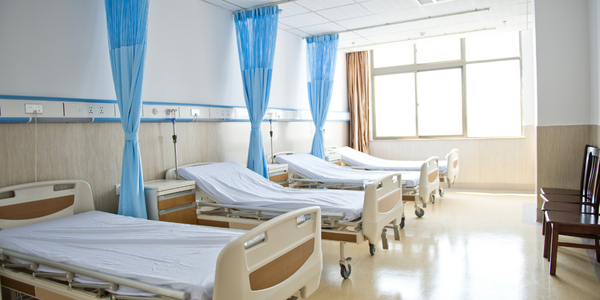
Case Study
Hospital Inventory Management
The hospital supply chain team is responsible for ensuring that the right medical supplies are readily available to clinicians when and where needed, and to do so in the most efficient manner possible. However, many of the systems and processes in use at the cancer center for supply chain management were not best suited to support these goals. Barcoding technology, a commonly used method for inventory management of medical supplies, is labor intensive, time consuming, does not provide real-time visibility into inventory levels and can be prone to error. Consequently, the lack of accurate and real-time visibility into inventory levels across multiple supply rooms in multiple hospital facilities creates additional inefficiency in the system causing over-ordering, hoarding, and wasted supplies. Other sources of waste and cost were also identified as candidates for improvement. Existing systems and processes did not provide adequate security for high-cost inventory within the hospital, which was another driver of cost. A lack of visibility into expiration dates for supplies resulted in supplies being wasted due to past expiry dates. Storage of supplies was also a key consideration given the location of the cancer center’s facilities in a dense urban setting, where space is always at a premium. In order to address the challenges outlined above, the hospital sought a solution that would provide real-time inventory information with high levels of accuracy, reduce the level of manual effort required and enable data driven decision making to ensure that the right supplies were readily available to clinicians in the right location at the right time.

Case Study
IoT Solution for Cold Chain
Most of the customer's warehouses run on utility and generator power. Since these warehouses are in remote locations, power outages are a very common scenario. Diesel fuel, thereby, becomes a significant cost for these warehouses. Energy consumption was also very high due to the lack of a consistent temperature throughout the facility. This lack of a consistent temperature in all areas and no way to control it, resulted in the customer losing a significant amount of their temperature sensitive goods due to spoilage.