Download PDF
OEC Group Automates Logistics With iWay
Technology Category
- Application Infrastructure & Middleware - Data Exchange & Integration
- Application Infrastructure & Middleware - Middleware, SDKs & Libraries
Applicable Industries
- Retail
- Automotive
Applicable Functions
- Logistics & Transportation
- Procurement
Use Cases
- Supply Chain Visibility
- Track & Trace of Assets
- Fleet Management
Services
- System Integration
- Software Design & Engineering Services
The Challenge
OEC Group, a global leader in the logistics and supply-chain industry, needed to expand its basic EDI integration infrastructure to include many types of electronic messages and formats including Adobe PDF, Microsoft Word, e-mail, Fax, XML, JSON, Excel, and other structured and unstructured data formats, as well as paper documents of all types. Prior to implementing iWay, developers at OEC Group hard-coded individual interfaces for each customer and supplier. This was laborious and expensive to develop new integrations. The company also needed to comply with the Canadian e-manifest program, which requires all carriers, freight forwarders, and importers to send advance commercial information about their shipments electronically to the Canada Border Services Agency. The data has to be processed before a shipment is ever loaded onto boats or planes, meaning the documents must be present at the port of departure before the government will allow goods to be loaded.
About The Customer
OEC Group is a global leader in the logistics and supply-chain industry. The Montreal, Canada-based company provides integrated logistics services and solutions to manufacturers, retailers, and other types of companies. Its global network is known for providing logistics intelligence and performance-driven, cost-effective freight forwarding strategies that help its clients respond quickly to market demands. With a specialization in ocean and air shipments throughout Asia and Europe, OEC Group’s worldwide infrastructure improves freight visibility and accuracy for many types of transactions. From aerospace to healthcare, retail to automotive manufacturing, OEC Group’s clients gain a more competitive and streamlined supply chain thanks to Information Builders’ iWay integration technology.
The Solution
OEC Group implemented iWay, a general-purpose service bus that can create reusable interfaces that accommodate EDI, web services, document management, ERP integration, and workflow automation. iWay became the backbone of OEC Group’s document management strategy. It uses OCR technology to process documents, as well as add metadata that makes these documents more relevant and valuable. iWay also automates more than 40 different workflows for OEC Group, dramatically reducing manual effort. Users previously had to wait for e-mail verifications before processing freight forwarding jobs. Using iWay, OEC Group now processes e-mails, identifies them, classifies them, and adds additional scanned documents if a second level of identification is required. iWay also detects errors, events, and milestones, and then alerts users of specific actions as part of a structured workflow.
Operational Impact
Quantitative Benefit
Related Case Studies.
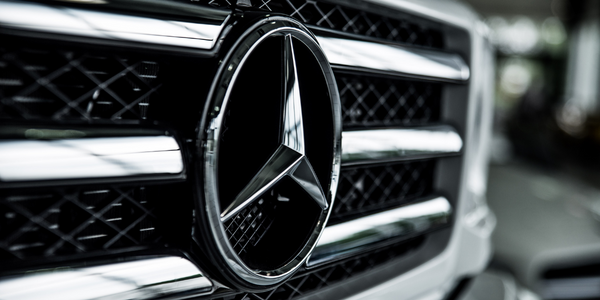
Case Study
Integral Plant Maintenance
Mercedes-Benz and his partner GAZ chose Siemens to be its maintenance partner at a new engine plant in Yaroslavl, Russia. The new plant offers a capacity to manufacture diesel engines for the Russian market, for locally produced Sprinter Classic. In addition to engines for the local market, the Yaroslavl plant will also produce spare parts. Mercedes-Benz Russia and his partner needed a service partner in order to ensure the operation of these lines in a maintenance partnership arrangement. The challenges included coordinating the entire maintenance management operation, in particular inspections, corrective and predictive maintenance activities, and the optimizing spare parts management. Siemens developed a customized maintenance solution that includes all electronic and mechanical maintenance activities (Integral Plant Maintenance).
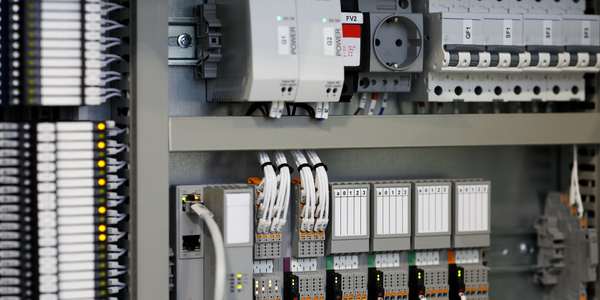
Case Study
Improving Production Line Efficiency with Ethernet Micro RTU Controller
Moxa was asked to provide a connectivity solution for one of the world's leading cosmetics companies. This multinational corporation, with retail presence in 130 countries, 23 global braches, and over 66,000 employees, sought to improve the efficiency of their production process by migrating from manual monitoring to an automatic productivity monitoring system. The production line was being monitored by ABB Real-TPI, a factory information system that offers data collection and analysis to improve plant efficiency. Due to software limitations, the customer needed an OPC server and a corresponding I/O solution to collect data from additional sensor devices for the Real-TPI system. The goal is to enable the factory information system to more thoroughly collect data from every corner of the production line. This will improve its ability to measure Overall Equipment Effectiveness (OEE) and translate into increased production efficiencies. System Requirements • Instant status updates while still consuming minimal bandwidth to relieve strain on limited factory networks • Interoperable with ABB Real-TPI • Small form factor appropriate for deployment where space is scarce • Remote software management and configuration to simplify operations