Download PDF
Optimising 3D Printed Stool Design with solidThinking Inspire: A Case Study on Assa Ashuach Studio
Technology Category
- Functional Applications - Manufacturing Execution Systems (MES)
- Sensors - Lidar & Lazer Scanners
Applicable Industries
- Electronics
- Life Sciences
Applicable Functions
- Product Research & Development
Use Cases
- Additive Manufacturing
- Time Sensitive Networking
The Challenge
Assa Ashuach Studio, a London-based industrial research and product design consultancy, was faced with the challenge of designing a stool that was both light and economical. The stool needed to be customised to support a weight of 120 kg. The challenge was to determine how much material could be removed from the design space while still supporting this weight and achieving a unique design. The design and manufacturing process had to be efficient, reducing material waste and cost, without compromising on the quality of the product. The studio was also interested in exploring new design and production methods to achieve unique forms and aesthetic qualities.
About The Customer
Assa Ashuach Studio is a London-based industrial research and product design consultancy that designs and manufactures lifestyle products and limited edition studio pieces. The studio employs a network of highly skilled specialists from the design, science, and manufacturing sectors, using dedicated 3D software development, electronics, and engineering as an integrated part of its design methodologies and philosophy. The studio is led by Director Assa Ashuach, who is always looking for innovative ways to design and manufacture products that are unique in form and aesthetic quality.
The Solution
The solution came in the form of Altair's solidThinking Inspire, a software that uses industry-leading OptiStruct technology to enable product designers to generate and investigate structurally efficient concepts quickly and easily. The software allows designers to import their design, create the design space, and then define materials and loading conditions. From this point, the ideal material layout is generated which can then be controlled to achieve the desired result of the final design. In this project, Inspire removed any redundant material according to stress zones on the object surface. An optimisation of the exterior and material use was made to achieve a light and economical form. The stool was produced by laser sintering, which allowed for a faster production time and energy savings by reducing the laser millage and distance to the final object layer.
Operational Impact
Quantitative Benefit
Related Case Studies.
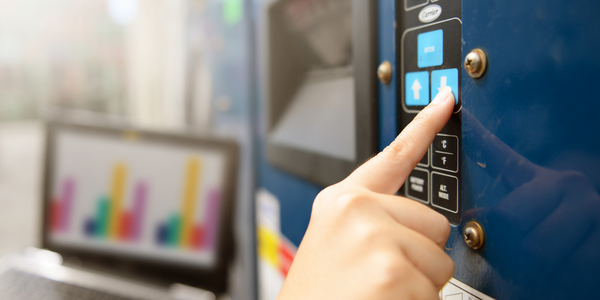
Case Study
Remote Temperature Monitoring of Perishable Goods Saves Money
RMONI was facing temperature monitoring challenges in a cold chain business. A cold chain must be established and maintained to ensure goods have been properly refrigerated during every step of the process, making temperature monitoring a critical business function. Manual registration practice can be very costly, labor intensive and prone to mistakes.
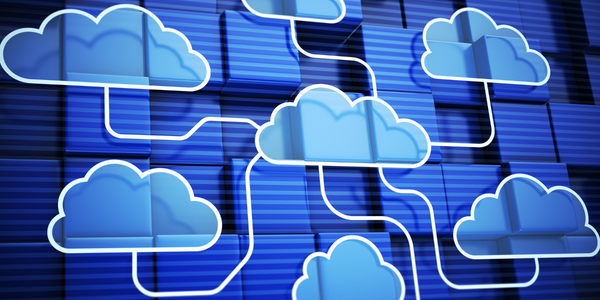
Case Study
Cloud Solution for Energy Management Platform-Schneider Electric
Schneider Electric required a cloud solution for its energy management platform to manage high computational operations, which were essential for catering to client requirements. As the business involves storage and analysis of huge amounts of data, the company also needed a convenient and scalable storage solution to facilitate operations efficiently.
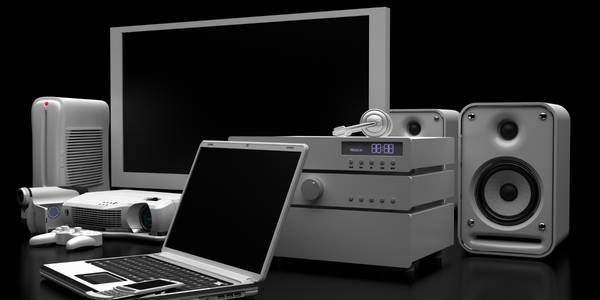
Case Study
Leveraging the IoT to Gain a Competitive Edge in International Competition
Many large manufacturers in and outside Japan are competing for larger market share in the same space, expecting a growing demand for projectors in the areas of entertainment, which requires glamor and strong visual performance as well as digital signage that can attract people’s attention. “It is becoming more and more difficult to differentiate ourselves with stand-alone hardware products,” says Kazuyuki Kitagawa, Director of Service & Support at Panasonic AVC Networks. “In order for Panasonic to grow market share and overall business, it is essential for us to develop solutions that deliver significant added value.” Panasonic believes projection failure and quality deterioration should never happen. This is what and has driven them to make their projectors IoT-enabled. More specifically, Panasonic has developed a system that collects data from projectors, visualizes detailed operational statuses, and predicts issues and address them before failure occurs. Their projectors are embedded with a variety of sensors that measure power supply, voltage, video input/ output signals, intake/exhaust air temperatures, cooling fan operations, and light bulb operating time. These sensors have been used to make the projector more intelligent, automatically suspending operation when the temperature rises excessively, and automatically switching light bulbs. Although this was a great first step, Panasonic projectors were still not equipped with any capability to send the data over a network.