Download PDF
Philips Leverages IoT for Efficient Product Conceptualization and Design
Technology Category
- Application Infrastructure & Middleware - Data Visualization
- Sensors - Autonomous Driving Sensors
Applicable Industries
- Electronics
- Healthcare & Hospitals
Applicable Functions
- Product Research & Development
Use Cases
- Construction Management
- Construction Site Monitoring
Services
- Training
The Challenge
Philips, a leading health technology company, was faced with the challenge of visualizing new product concepts quickly and efficiently. The goal was to work collaboratively with design colleagues and the engineering department to share feedback, understand challenges, and ultimately conceptualize final products. The company needed a tool that could be used by all members of the team to create consistency, facilitate easy file transfer/handoff with design peers and engineering, and increase overall team speed and efficiency. The existing tools were not meeting these requirements, leading to a search for a new software solution.
About The Customer
Royal Philips, founded in 1891 in the Netherlands, is one of the largest electronics companies in the world, employing over 105,000 individuals in over 100 countries. It is a leading health technology company with a keen focus on improving people’s health. This spans from healthy living, to diagnosis, treatment, and home care. Philips puts strong emphasis on leveraging the latest in technology, design, and deep consumer insights when developing each of the products in its broad portfolio. The company is a leader in diagnostic imaging, image-guided therapy, patient monitoring and health informatics, as well as consumer health and home care. Design is a key aspect of the company’s success, driving everything they bring to market.
The Solution
Philips adopted solidThinking Evolve for concept development and visualization. This tool was selected after a pilot program and a 1-week training course. Jens Andersson, a Design Lead at Philips Design, utilized Evolve on a live project shortly after the training. Since then, Evolve has been used on a number of projects, including three that have already gone to market, as well as multiple strategic projects that Philips is currently exploring in health care, male grooming, and personal health. Evolve's construction history features allow the design team to adapt their models for both business or technical reasons while development is ongoing, rather than starting from scratch. It also enables quick reaction and tweaking of the design while keeping the original design intent intact.
Operational Impact
Quantitative Benefit
Related Case Studies.
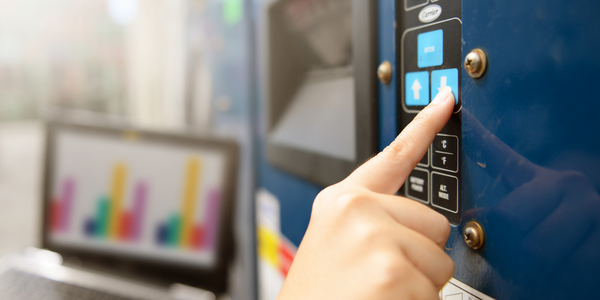
Case Study
Remote Temperature Monitoring of Perishable Goods Saves Money
RMONI was facing temperature monitoring challenges in a cold chain business. A cold chain must be established and maintained to ensure goods have been properly refrigerated during every step of the process, making temperature monitoring a critical business function. Manual registration practice can be very costly, labor intensive and prone to mistakes.
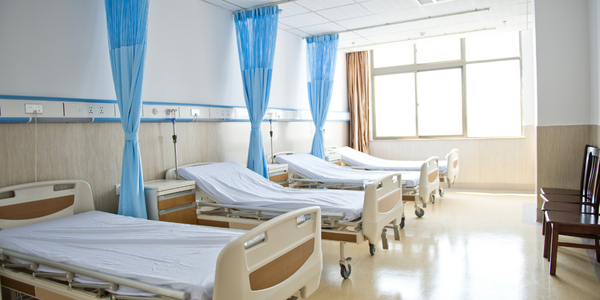
Case Study
Hospital Inventory Management
The hospital supply chain team is responsible for ensuring that the right medical supplies are readily available to clinicians when and where needed, and to do so in the most efficient manner possible. However, many of the systems and processes in use at the cancer center for supply chain management were not best suited to support these goals. Barcoding technology, a commonly used method for inventory management of medical supplies, is labor intensive, time consuming, does not provide real-time visibility into inventory levels and can be prone to error. Consequently, the lack of accurate and real-time visibility into inventory levels across multiple supply rooms in multiple hospital facilities creates additional inefficiency in the system causing over-ordering, hoarding, and wasted supplies. Other sources of waste and cost were also identified as candidates for improvement. Existing systems and processes did not provide adequate security for high-cost inventory within the hospital, which was another driver of cost. A lack of visibility into expiration dates for supplies resulted in supplies being wasted due to past expiry dates. Storage of supplies was also a key consideration given the location of the cancer center’s facilities in a dense urban setting, where space is always at a premium. In order to address the challenges outlined above, the hospital sought a solution that would provide real-time inventory information with high levels of accuracy, reduce the level of manual effort required and enable data driven decision making to ensure that the right supplies were readily available to clinicians in the right location at the right time.
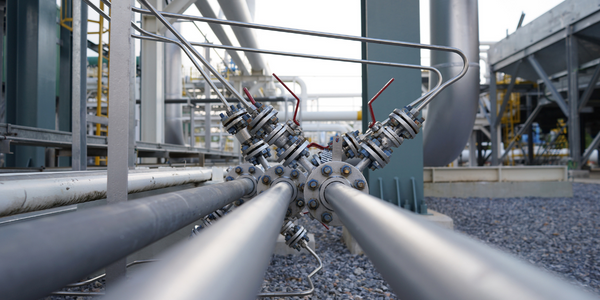
Case Study
Gas Pipeline Monitoring System for Hospitals
This system integrator focuses on providing centralized gas pipeline monitoring systems for hospitals. The service they provide makes it possible for hospitals to reduce both maintenance and labor costs. Since hospitals may not have an existing network suitable for this type of system, GPRS communication provides an easy and ready-to-use solution for remote, distributed monitoring systems System Requirements - GPRS communication - Seamless connection with SCADA software - Simple, front-end control capability - Expandable I/O channels - Combine AI, DI, and DO channels
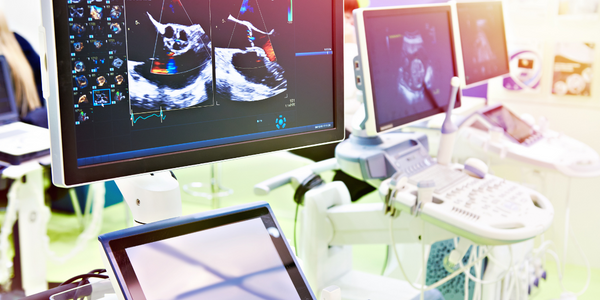
Case Study
Driving Digital Transformations for Vitro Diagnostic Medical Devices
Diagnostic devices play a vital role in helping to improve healthcare delivery. In fact, an estimated 60 percent of the world’s medical decisions are made with support from in vitrodiagnostics (IVD) solutions, such as those provided by Roche Diagnostics, an industry leader. As the demand for medical diagnostic services grows rapidly in hospitals and clinics across China, so does the market for IVD solutions. In addition, the typically high cost of these diagnostic devices means that comprehensive post-sales services are needed. Wanteed to improve three portions of thr IVD:1. Remotely monitor and manage IVD devices as fixed assets.2. Optimizing device availability with predictive maintenance.3. Recommending the best IVD solution for a customer’s needs.