Download PDF
Plantool Oy: Enhancing Production Automation with ANSYS DesignSpace Simulation Software
Technology Category
- Analytics & Modeling - Digital Twin / Simulation
Applicable Industries
- Equipment & Machinery
Applicable Functions
- Product Research & Development
Use Cases
- Virtual Prototyping & Product Testing
- Virtual Reality
The Challenge
Plantool Oy, a leading production automation company in the Nordic countries, faced significant challenges in its operations. The company specializes in tailor-made special machines, standard circular saws, system solutions, and production lines for metal industries. However, the custom nature of their machines did not allow for prototypes. Each new order posed a major risk as the initial creation had to be the final product, necessitating perfect design from the outset. Additionally, these special machines often had to be designed from scratch, requiring a flexible design and simulation process. The use of existing 3D models for simulation was crucial, but the company lacked an efficient system to facilitate this.
About The Customer
Plantool Oy is a Finland-based company with 30 years of experience in the production automation industry. The company markets and manufactures tailor-made special machines, standard circular saws, system solutions, and production lines for metal industries. Located in Seinäjoki, Finland, Plantool Oy is recognized as one of the leading production automation companies in the Nordic countries. The company's operations are characterized by the production of custom machines, which presents unique challenges in terms of design and risk management.
The Solution
To overcome these challenges, Plantool Oy adopted ANSYS DesignSpace, integrating it with Autodesk Inventor 3D design tools. This allowed the company to analyze machine parts and structural performance in the early stages of the design process. The solution enabled virtual prototyping, which was instrumental in designing better tailor-made special machines. Large assemblies were analyzed with minor defeaturing of the model, and various alternatives were cost-effectively investigated. The integration of ANSYS DesignSpace with Autodesk Inventor meant that geometry modeling for analysis could be completed with a program Plantool designers were already familiar with, eliminating the need to learn new software.
Operational Impact
Quantitative Benefit
Related Case Studies.
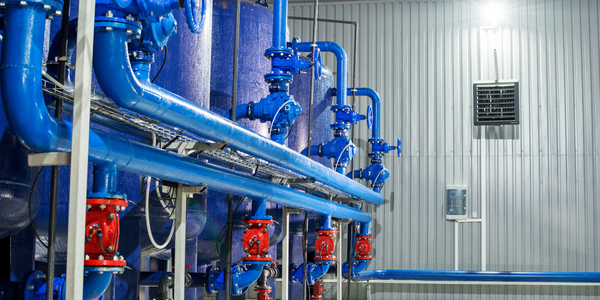
Case Study
Smart Water Filtration Systems
Before working with Ayla Networks, Ozner was already using cloud connectivity to identify and solve water-filtration system malfunctions as well as to monitor filter cartridges for replacements.But, in June 2015, Ozner executives talked with Ayla about how the company might further improve its water systems with IoT technology. They liked what they heard from Ayla, but the executives needed to be sure that Ayla’s Agile IoT Platform provided the security and reliability Ozner required.
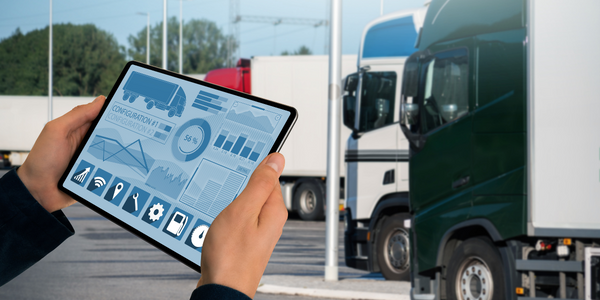
Case Study
IoT enabled Fleet Management with MindSphere
In view of growing competition, Gämmerler had a strong need to remain competitive via process optimization, reliability and gentle handling of printed products, even at highest press speeds. In addition, a digitalization initiative also included developing a key differentiation via data-driven services offers.
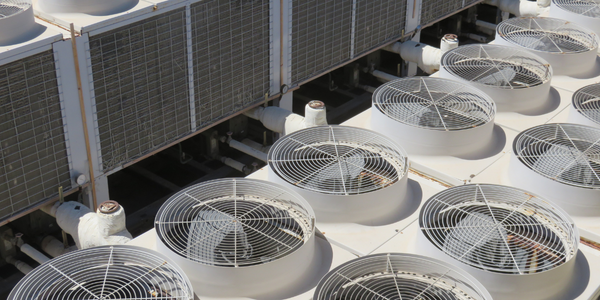
Case Study
Predictive Maintenance for Industrial Chillers
For global leaders in the industrial chiller manufacturing, reliability of the entire production process is of the utmost importance. Chillers are refrigeration systems that produce ice water to provide cooling for a process or industrial application. One of those leaders sought a way to respond to asset performance issues, even before they occur. The intelligence to guarantee maximum reliability of cooling devices is embedded (pre-alarming). A pre-alarming phase means that the cooling device still works, but symptoms may appear, telling manufacturers that a failure is likely to occur in the near future. Chillers who are not internet connected at that moment, provide little insight in this pre-alarming phase.
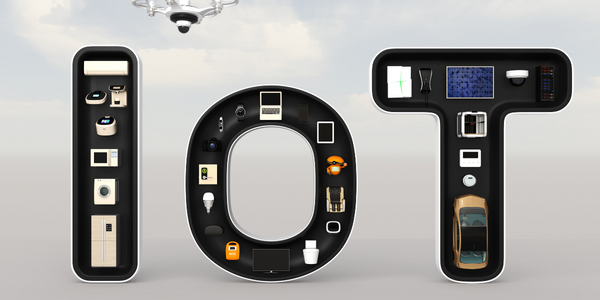
Case Study
Premium Appliance Producer Innovates with Internet of Everything
Sub-Zero faced the largest product launch in the company’s history:It wanted to launch 60 new products as scheduled while simultaneously opening a new “greenfield” production facility, yet still adhering to stringent quality requirements and manage issues from new supply-chain partners. A the same time, it wanted to increase staff productivity time and collaboration while reducing travel and costs.
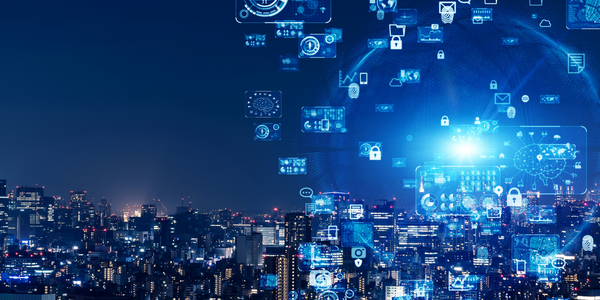
Case Study
Integration of PLC with IoT for Bosch Rexroth
The application arises from the need to monitor and anticipate the problems of one or more machines managed by a PLC. These problems, often resulting from the accumulation over time of small discrepancies, require, when they occur, ex post technical operations maintenance.
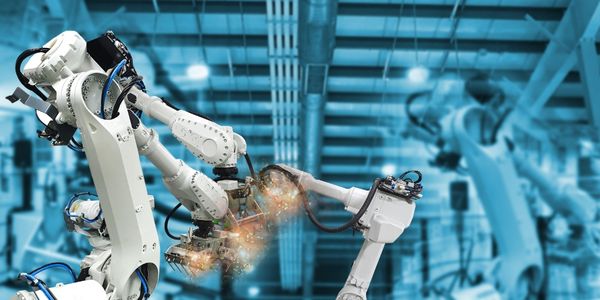
Case Study
Robot Saves Money and Time for US Custom Molding Company
Injection Technology (Itech) is a custom molder for a variety of clients that require precision plastic parts for such products as electric meter covers, dental appliance cases and spools. With 95 employees operating 23 molding machines in a 30,000 square foot plant, Itech wanted to reduce man hours and increase efficiency.