Download PDF
Polymers International Enhances Customer Service through Automated Shipment Tracking
Technology Category
- Analytics & Modeling - Real Time Analytics
- Cybersecurity & Privacy - Identity & Authentication Management
Applicable Industries
- Glass
- Plastics
Applicable Functions
- Logistics & Transportation
- Sales & Marketing
Use Cases
- Real-Time Location System (RTLS)
- Supply Chain Visibility
The Challenge
Polymers International, a global player in the plastics and rubber industry, was facing significant challenges in tracking the movement of its approximately 200 monthly shipments. The lack of efficient tracking mechanisms led to difficulties in keeping customers informed about shipment statuses, resulting in confusion and subpar customer service. The operations team had to visit multiple carrier websites to gather updates on shipment locations, a process that was not only time-consuming and prone to errors but also diverted the team from focusing on more critical tasks. The inaccuracies in tracking updates led to a surge in customer queries regarding shipment statuses. The team also struggled with accessing timely information on changes in departure and arrival timings, making it challenging to provide customers with accurate delivery dates. Furthermore, the company was unable to leverage crucial insights such as visibility on the carriers offering the best service, trade routes ensuring cost-effectiveness and speedy deliveries, thereby compromising their ability to identify cost-saving opportunities and make informed decisions.
About The Customer
Polymers International is a global company founded in 1995, renowned for its contributions to the plastics and rubber industry. The company specializes in the marketing, sales, and distribution of high-performance elastomers, engineering plastics, silicones, specialty polyolefins, and films. It serves customers worldwide, with Australia and New Zealand being its key markets. The company was facing challenges in tracking its approximately 200 monthly shipments, leading to customer dissatisfaction and inefficiencies in operations.
The Solution
Polymers International sought a solution that could provide real-time visibility of all their global shipments on a single platform. GoComet's GoTrack Automated Shipment Tracking module provided the solution they needed. GoTrack automated the end-to-end shipment tracking process, eliminating human dependency and saving 90% of the time previously required for tracking shipments. This automation allowed the operations team to focus on more critical tasks. The module provided real-time cargo tracking, enabling the company to proactively respond to disruptions, efficiently plan their supply chain operations, and eliminate the possibility of detention and demurrage charges. GoTrack's comprehensive dashboard and its ability to generate detailed reports on carrier performance enabled the company to make informed decisions and identify the most reliable service providers. The solution also significantly improved Polymers International's customer service by reducing customer queries around shipment tracking by 80% and allowing the company to share live tracking updates directly with customers for their specific orders.
Operational Impact
Quantitative Benefit
Related Case Studies.
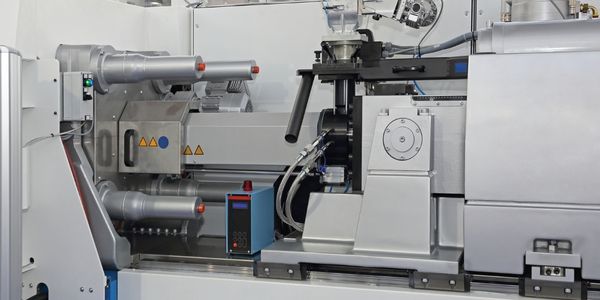
Case Study
Plastic Spoons Case study: Injection Moulding
In order to meet customer expectations by supplying a wide variety of packaging units, from 36 to 1000 spoons per package, a new production and packaging line needed to be built. DeSter wanted to achieve higher production capacity, lower cycle time and a high degree of operator friendliness with this new production line.
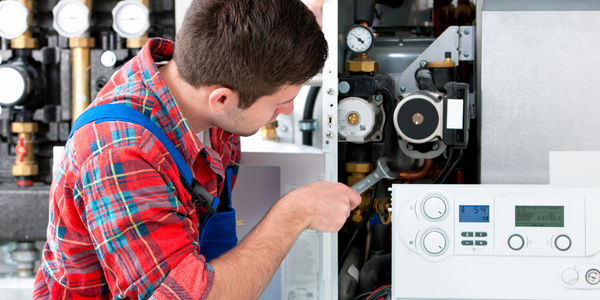
Case Study
Boiler Control System for Plastic Manufacturing Applications
Factory automation applications must be equipped to handle and monitor the myriads of information from attached devices. For plastic manufacturing applications, the boiler control system plays a critical role by gathering and regulating information to ensure production is accurate and smooth. In this particular case, the customer combines eight subsystems that include power meters, water meters, alarm output, displays, and I/O status to be controlled by several intelligent controllers with Modbus RTU interface. The Modbus TCP protocol is used for this application due to the distance. System Requirements: • Modbus serial to Modbus TCP translation • Multiple slaves/masters support • Automatic Modbus TCP response time detection
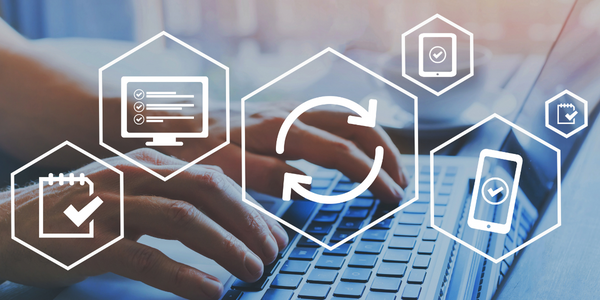
Case Study
Ascend Performance Materials Case Study
Ascend operations must access multiple software systems to manage day-to-day operations in an effective and secure manner. These systems generate large sets of data which contain critical information pertaining to management systems, planning and cost information in business systems and energy consumption. As a result, Ascend management was challenged with creating relevant reports reflecting performance measures in overall context of their operational process. The company’s previous process entailed collecting and analyzing data manually which was not effective, since the information collected was generated after the fact, and was too complex for collaborative use across the organization.
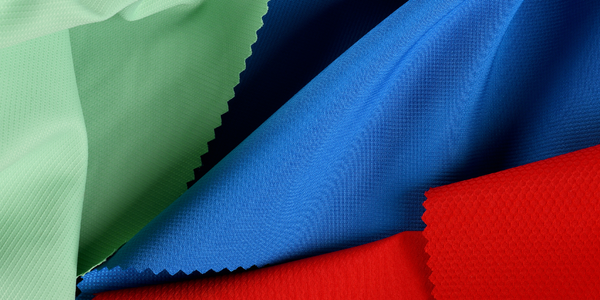
Case Study
Remake Enterprise-to-production System
The client was running a legacy material flow tracking system and wanted to replace the system with a more effective one as the system was increasingly expensive to maintain and support and also was not extendable. The client's IT landscape was filled with modern applications and it was difficult to interface the material flow tracking system with modern applications.
.png)
Case Study
Discrete Manufacturing Industries (Fiberglass Pipe)
The implementation of ERP software in a Discrete Manufacturing organization needs to be strategic, irrespective of its size and capacity. The client had already implemented an ERP system which fulfilled their requirements but was not efficient enough. Efficiency here meant Synchronized Planning, Updating and Multisite Planning. Planning at client’s place was done outside the ERP system. Lack of proper synchronization to the ERP system paved way to huge delays in the changes getting updated in the system. These delays caused disruption in achieving delivery schedules. Multisite Planning is a solution to an organization which has multiple production units (may or may not be geographically separated) and thus needs planning across these units to synchronize production activities within them. The client also has multiple factories and hence Production Planning control is very essential in their case. Since Multisite planning was not possible with Baan ERP system, this was another bottleneck for the client.