Predicting Rare Failures in Hydro Turbines

- Analytics & Modeling - Machine Learning
- Analytics & Modeling - Predictive Analytics
- Functional Applications - Remote Monitoring & Control Systems
- Sensors - Accelerometers
- Sensors - Level Sensors
- Sensors - Temperature Sensors
- Sensors - Vibration Sensors
- Utilities
- Maintenance
- Predictive Maintenance
Utility companies that operate hydro turbines have a vested interest in performing regular maintenance to prevent unexpected failures. Most maintenance occurs on a scheduled basis where the asset is taken offline, inspected, and repaired proactively if needed. Hydro turbine units are highly reliable, meaning that few examples of unplanned downtime exist. However, these failures are very costly to their operators.
Given the sensitivity operators have to unplanned downtime, many have equipped turbines and generators with sensors and platforms to collect valuable performance information in real-time. But because there are so few historical hydro failures to compare against, rich streaming data and legacy statistics-based analysis are not very accurate at predicting true failure events. In fact, they often create more problems by overloading monitoring teams with benign false positives that result in unnecessary downtime to evaluate. This begs the question: Can artificial intelligence help maintenance teams extract more value out of their data?
For the engagement, the hydropower utility company wanted to evaluate SparkPredict’s performance in two key areas and compare the results to their existing, statistics-based solution:
• Could SparkPredict detect changes to the generator prior to known events that occurred in one of their turbines?
• What additional insights could SparkPredict provide to the engineering teams to help them improve maintenance?
SparkCognition was provided with two years of data for one turbine which had experienced several failure events between 2015-2016.
From the given collection of sensors, SparkPredict data scientists identified 40 important tags which measured important variables such as generator speed, power output, temperature readings, oil level, vibrations, and shaft gap measurements. Within six weeks of receiving the data, SparkPredict data scientists researched, trained, and built an unsupervised machine learning model. Unsupervised learning is especially powerful when predicting rare failures since there is little failure information and none of it is consistently documented. Instead of comparing to previously known indicators, this type of model adapts to the unique behaviour of the asset. By flagging anomalous behaviour, SparkPredict can identify indicators for unknown failures.
Using this approach, SparkPredict accurately identified the turbine failure events within the data set with over one-month advanced warning, successfully fulfilling the first project criteria.
Additionally, SparkPredict exposed key leading indicators for the events with explainable AI. In particular, the utility wanted to see how multiple sensors related to one another and how small, subtle deviations from historical measurements contributed to incipient failure modes. SparkPredict elevated nine sensors whose values had changed.
Related Case Studies.

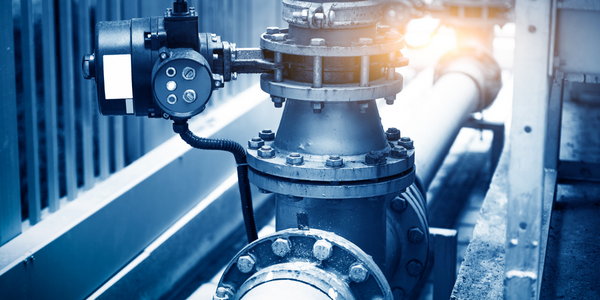
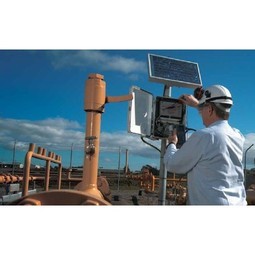
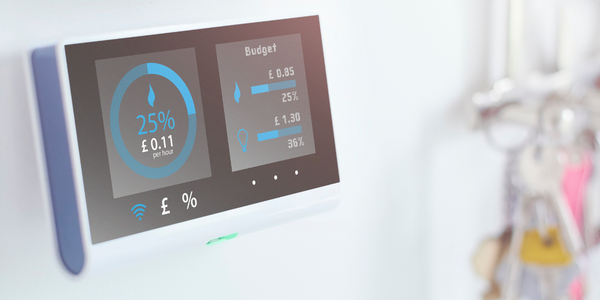
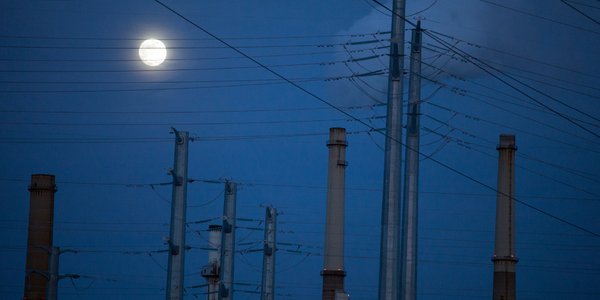
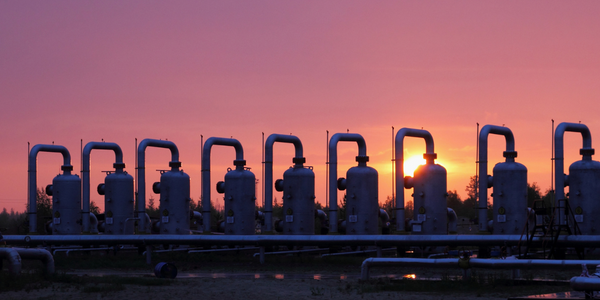