Download PDF
Q-Safety's Transformation: Automating Health and Safety Processes in Construction
Technology Category
- Analytics & Modeling - Real Time Analytics
- Platform as a Service (PaaS) - Application Development Platforms
Applicable Industries
- Cement
- Healthcare & Hospitals
Applicable Functions
- Human Resources
- Quality Assurance
Use Cases
- Construction Site Monitoring
- Onsite Human Safety Management
Services
- System Integration
- Testing & Certification
The Challenge
Q-Safety by Quirónprevención, a leading company in the provision of health and safety services for the construction sector, faced a significant challenge in automating its business processes. The company's work system was heavily dependent on manual processes for routine tasks such as data entry, registration and search for information, and document storage. This led to delays in processing contracting services for clients and subsequent invoicing. It also caused problems in tracking documents, errors, and even loss of documentation. The company used an ERP for enterprise resource planning, but it did not adapt to their specific needs as it did not allow automation and data input was completely manual. The company needed a technology solution that could automate its processes, provide real-time data, and be highly customizable.
About The Customer
Q-Safety by Quirónprevención is a Spanish company specializing in health and safety services for the construction sector. It was created following the merger of the largest companies specializing in Occupational Risk Prevention and Business Activity Coordination. With over 25 years of experience and more than 150 professionals, this subsidiary of the Quirónprevención Group offers a wide range of services including health and safety coordination on construction sites, technical offices, safety management, health and safety technical assistance and the health and safety certification “Spatium”. The company has participated in important construction projects including the BBVA City (Madrid), Vodafone Plaza (Madrid), Airbus Defense & Space Campus (Madrid), C.C. Finestrelles Esplugues (Barcelona), Lagoh Shopping Centre (Seville), Vialia Estación de Vigo (Pontevedra) and the “Living Stone” ship (Vizcaya).
The Solution
Q-Safety by Quirónprevención chose AuraQuantic as their technology solution. AuraQuantic allowed the company to automate all its business processes, from quote preparation to resource allocation, service delivery, and invoicing. The platform enabled the company's technicians to record their activities online during site visits, which immediately resulted in the issuance of a report to all those involved in the work. This report was recorded in the system, allowing real-time control of its activity, and the possibility for the technician to consult the evolution of the work at any time. AuraQuantic also enabled the General Services Administration department to keep control of the available material resources. The company implemented three macro-processes: offer and budget management, service delivery and control, and invoicing. These macro-processes were further divided into other sub-processes, with the company managing around 400 processes on AuraQuantic.
Operational Impact
Quantitative Benefit
Related Case Studies.
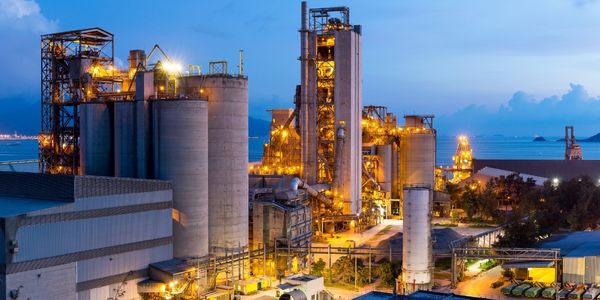
Case Study
System 800xA at Indian Cement Plants
Chettinad Cement recognized that further efficiencies could be achieved in its cement manufacturing process. It looked to investing in comprehensive operational and control technologies to manage and derive productivity and energy efficiency gains from the assets on Line 2, their second plant in India.
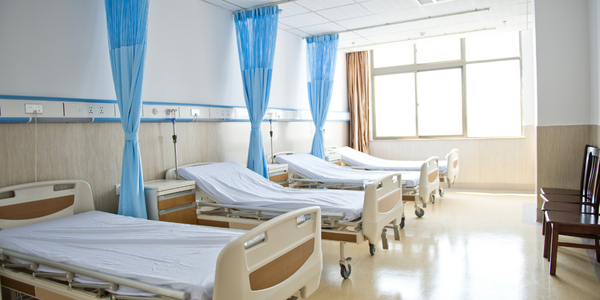
Case Study
Hospital Inventory Management
The hospital supply chain team is responsible for ensuring that the right medical supplies are readily available to clinicians when and where needed, and to do so in the most efficient manner possible. However, many of the systems and processes in use at the cancer center for supply chain management were not best suited to support these goals. Barcoding technology, a commonly used method for inventory management of medical supplies, is labor intensive, time consuming, does not provide real-time visibility into inventory levels and can be prone to error. Consequently, the lack of accurate and real-time visibility into inventory levels across multiple supply rooms in multiple hospital facilities creates additional inefficiency in the system causing over-ordering, hoarding, and wasted supplies. Other sources of waste and cost were also identified as candidates for improvement. Existing systems and processes did not provide adequate security for high-cost inventory within the hospital, which was another driver of cost. A lack of visibility into expiration dates for supplies resulted in supplies being wasted due to past expiry dates. Storage of supplies was also a key consideration given the location of the cancer center’s facilities in a dense urban setting, where space is always at a premium. In order to address the challenges outlined above, the hospital sought a solution that would provide real-time inventory information with high levels of accuracy, reduce the level of manual effort required and enable data driven decision making to ensure that the right supplies were readily available to clinicians in the right location at the right time.
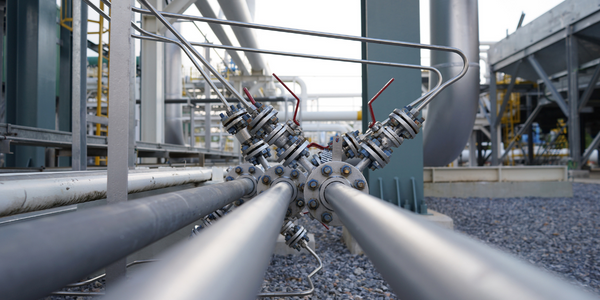
Case Study
Gas Pipeline Monitoring System for Hospitals
This system integrator focuses on providing centralized gas pipeline monitoring systems for hospitals. The service they provide makes it possible for hospitals to reduce both maintenance and labor costs. Since hospitals may not have an existing network suitable for this type of system, GPRS communication provides an easy and ready-to-use solution for remote, distributed monitoring systems System Requirements - GPRS communication - Seamless connection with SCADA software - Simple, front-end control capability - Expandable I/O channels - Combine AI, DI, and DO channels
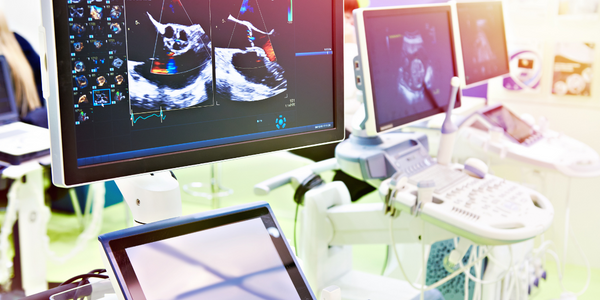
Case Study
Driving Digital Transformations for Vitro Diagnostic Medical Devices
Diagnostic devices play a vital role in helping to improve healthcare delivery. In fact, an estimated 60 percent of the world’s medical decisions are made with support from in vitrodiagnostics (IVD) solutions, such as those provided by Roche Diagnostics, an industry leader. As the demand for medical diagnostic services grows rapidly in hospitals and clinics across China, so does the market for IVD solutions. In addition, the typically high cost of these diagnostic devices means that comprehensive post-sales services are needed. Wanteed to improve three portions of thr IVD:1. Remotely monitor and manage IVD devices as fixed assets.2. Optimizing device availability with predictive maintenance.3. Recommending the best IVD solution for a customer’s needs.
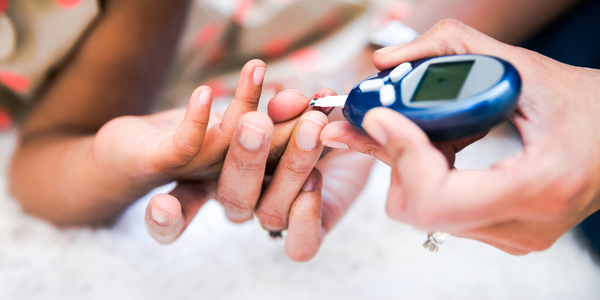
Case Study
HaemoCloud Global Blood Management System
1) Deliver a connected digital product system to protect and increase the differentiated value of Haemonetics blood and plasma solutions. 2) Improve patient outcomes by increasing the efficiency of blood supply flows. 3) Navigate and satisfy a complex web of global regulatory compliance requirements. 4) Reduce costly and labor-intensive maintenance procedures.