Download PDF
QlikView enables the straight way to a coordinated business for Systemair
Technology Category
- Analytics & Modeling - Real Time Analytics
Applicable Functions
- Sales & Marketing
Use Cases
- Process Control & Optimization
- Real-Time Location System (RTLS)
Services
- Software Design & Engineering Services
- System Integration
The Challenge
Systemair, a leading ventilation company with operations mainly in Europe and North America, faced several challenges. The company needed to share valuable business data locked in its Movex ERP system with more than 25 subsidiaries throughout Europe. The goal was to simplify and speed up data analysis enterprise-wide for improved decision-making. Additionally, Systemair wanted tighter control over business processes and operations to ensure 24x7 product availability for customers. As the business complexity grew, the existing system of analyzing data with simple SQL queries and Excel became unworkable.
About The Customer
Systemair is a leading ventilation company with the main part of its operations in Europe and North America. The company was founded and built up around an innovation that revolutionized the ventilation business. The circular inline centrifugal duct fan made it possible to straighten the ventilation duct. Today, the company has expanded all over Europe with approximately 1,400 employees. More than 80% of the production is exported. Availability, innovative products, and high competence are the most important reasons why Systemair has been able to grow steadily ever since its beginning in 1974.
The Solution
Systemair deployed QlikView to 400 employees throughout Europe, with several applications up and running in less than 1 week. With QlikView across 6 functional areas, management now has complete control and visibility over the entire operation to ensure on-time delivery of their products throughout Europe. And, with QlikView Server (64-bit), the company easily handles the large data volume. Data that was previously locked in its Movex ERP system as well as multiple other systems are now easily accessible and more functional. Today, Systemair has QlikView applications for sales & marketing, finance, staff, production, purchasing, and inventory. All applications are open to virtually all employees. Today 21 of 30 European subsidiaries use Movex and thereby also QlikView.
Operational Impact
Related Case Studies.
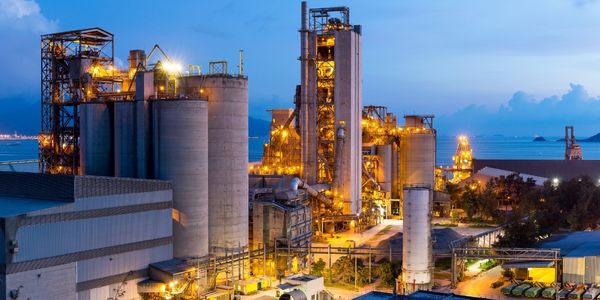
Case Study
System 800xA at Indian Cement Plants
Chettinad Cement recognized that further efficiencies could be achieved in its cement manufacturing process. It looked to investing in comprehensive operational and control technologies to manage and derive productivity and energy efficiency gains from the assets on Line 2, their second plant in India.
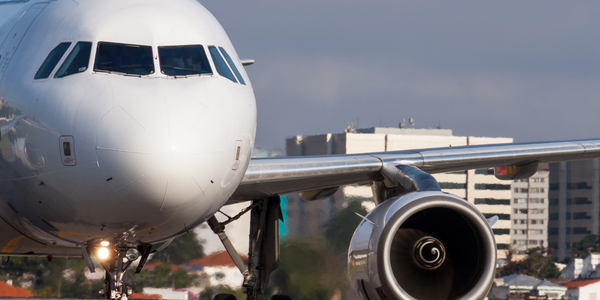
Case Study
Airbus Soars with Wearable Technology
Building an Airbus aircraft involves complex manufacturing processes consisting of thousands of moving parts. Speed and accuracy are critical to business and competitive advantage. Improvements in both would have high impact on Airbus’ bottom line. Airbus wanted to help operators reduce the complexity of assembling cabin seats and decrease the time required to complete this task.
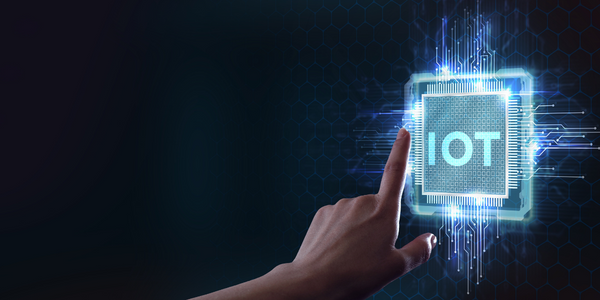
Case Study
Leading Tools Manufacturer Transforms Operations with IoT
Stanley Black & Decker required transparency of real-time overall equipment effectiveness and line productivity to reduce production line change over time.The goal was to to improve production to schedule, reduce actual labor costs and understanding the effects of shift changes and resource shifts from line to line.
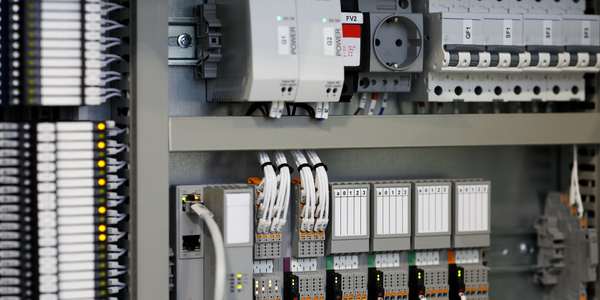
Case Study
Improving Production Line Efficiency with Ethernet Micro RTU Controller
Moxa was asked to provide a connectivity solution for one of the world's leading cosmetics companies. This multinational corporation, with retail presence in 130 countries, 23 global braches, and over 66,000 employees, sought to improve the efficiency of their production process by migrating from manual monitoring to an automatic productivity monitoring system. The production line was being monitored by ABB Real-TPI, a factory information system that offers data collection and analysis to improve plant efficiency. Due to software limitations, the customer needed an OPC server and a corresponding I/O solution to collect data from additional sensor devices for the Real-TPI system. The goal is to enable the factory information system to more thoroughly collect data from every corner of the production line. This will improve its ability to measure Overall Equipment Effectiveness (OEE) and translate into increased production efficiencies. System Requirements • Instant status updates while still consuming minimal bandwidth to relieve strain on limited factory networks • Interoperable with ABB Real-TPI • Small form factor appropriate for deployment where space is scarce • Remote software management and configuration to simplify operations