Download PDF
Real-time Data Engineering for Industrial Systems Testing & Monitoring

Technology Category
- Analytics & Modeling - Machine Learning
- Analytics & Modeling - Predictive Analytics
Applicable Industries
- Equipment & Machinery
- Renewable Energy
Applicable Functions
- Maintenance
- Quality Assurance
Use Cases
- Machine Condition Monitoring
- Real-Time Location System (RTLS)
Services
- Data Science Services
- Training
The Challenge
The UK-based instruments engineering company was facing challenges with their existing system of capturing, managing, and analyzing data from live machines and systems. The sensors installed on various components of industrial equipment like turbines and pumps captured physical data at a high frequency, which was then managed and analyzed locally on desktop-based systems. This resulted in manual, inaccurate, and time-consuming fault detection. The company decided to automate data collection, enable cloud-based data processing, and implement AI-based fault detection. However, they faced several challenges including the difficulty of scaling and deploying traditional predictive tools, the need for predictive analytics to be embedded within their application, the requirement of expertise for data preparation, cleansing, choosing the right algorithm, training, and validation, and the need for the platform and application to easily integrate with all hardware products.
The Customer
Not disclosed
About The Customer
The customer is a UK-based instruments engineering company that empowers leaders in the industrial equipment and renewable energy industry. They provide smart sensors and hardware to help industrial enterprises reduce their equipment maintenance costs, improve machine yield, increase machine uptime, and ensure process quality. Their smart hardware solution captures vibration and other environmental data in real time through sensors installed on various components of industrial equipment like turbines and pumps. The data is then processed to monitor, analyze, and alert about machine condition, generating insights to help predict downtimes and maintain systems health and equipment efficiency.
The Solution
The company adopted a minimum viable product approach to quickly engineer and build a data platform capable of connecting millions of sensors globally and enabling industrial systems and equipment to be more intelligent about their failures, availability, and operating efficiency. They partnered with Saviant to develop the intelligent data platform. The team of technology consultants included Data Science/Machine Learning consultants, a Technology Architect, and IoT consultants. The platform designed enabled high-performance data engineering and automated capturing data, orchestration, and analysis. Machine Learning models were used to replace the age-old “if-then rules” method of fault detection. The platform also provided accurate and timely alerts and notifications about the failure conditions and alarms.
Operational Impact
Related Case Studies.
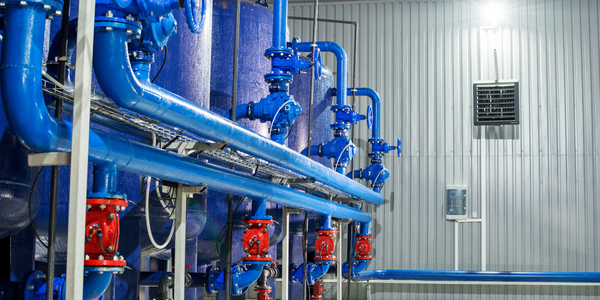
Case Study
Smart Water Filtration Systems
Before working with Ayla Networks, Ozner was already using cloud connectivity to identify and solve water-filtration system malfunctions as well as to monitor filter cartridges for replacements.But, in June 2015, Ozner executives talked with Ayla about how the company might further improve its water systems with IoT technology. They liked what they heard from Ayla, but the executives needed to be sure that Ayla’s Agile IoT Platform provided the security and reliability Ozner required.
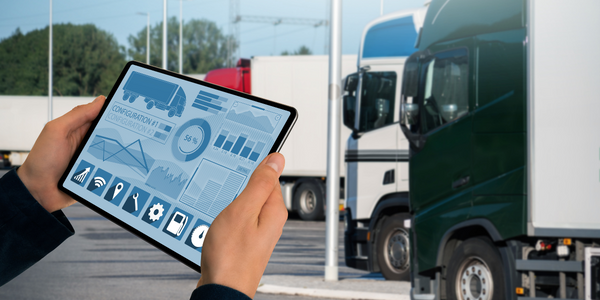
Case Study
IoT enabled Fleet Management with MindSphere
In view of growing competition, Gämmerler had a strong need to remain competitive via process optimization, reliability and gentle handling of printed products, even at highest press speeds. In addition, a digitalization initiative also included developing a key differentiation via data-driven services offers.
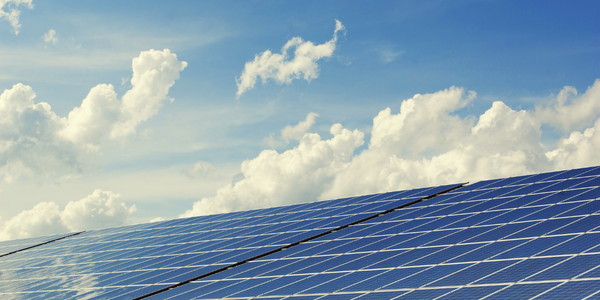
Case Study
Remote Monitoring & Predictive Maintenance App for a Solar Energy System
The maintenance & tracking of various modules was an overhead for the customer due to the huge labor costs involved. Being an advanced solar solutions provider, they wanted to ensure early detection of issues and provide the best-in-class customer experience. Hence they wanted to automate the whole process.
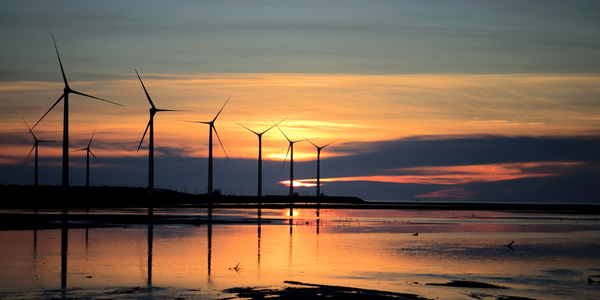
Case Study
Vestas: Turning Climate into Capital with Big Data
Making wind a reliable source of energy depends greatly on the placement of the wind turbines used to produce electricity. Turbulence is a significant factor as it strains turbine components, making them more likely to fail. Vestas wanted to pinpoint the optimal location for wind turbines to maximize power generation and reduce energy costs.
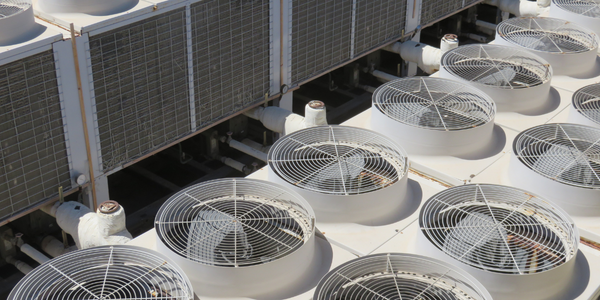
Case Study
Predictive Maintenance for Industrial Chillers
For global leaders in the industrial chiller manufacturing, reliability of the entire production process is of the utmost importance. Chillers are refrigeration systems that produce ice water to provide cooling for a process or industrial application. One of those leaders sought a way to respond to asset performance issues, even before they occur. The intelligence to guarantee maximum reliability of cooling devices is embedded (pre-alarming). A pre-alarming phase means that the cooling device still works, but symptoms may appear, telling manufacturers that a failure is likely to occur in the near future. Chillers who are not internet connected at that moment, provide little insight in this pre-alarming phase.
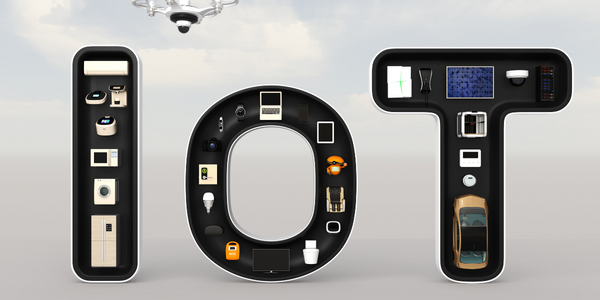
Case Study
Premium Appliance Producer Innovates with Internet of Everything
Sub-Zero faced the largest product launch in the company’s history:It wanted to launch 60 new products as scheduled while simultaneously opening a new “greenfield” production facility, yet still adhering to stringent quality requirements and manage issues from new supply-chain partners. A the same time, it wanted to increase staff productivity time and collaboration while reducing travel and costs.