Download PDF
Scaling Creative Operations Across Global Markets: A Case Study on Schroders and Bynder
Technology Category
- Functional Applications - Enterprise Asset Management Systems (EAM)
- Platform as a Service (PaaS) - Application Development Platforms
Applicable Industries
- Cement
- Equipment & Machinery
Applicable Functions
- Product Research & Development
- Sales & Marketing
Use Cases
- Machine Translation
- Time Sensitive Networking
Services
- Testing & Certification
The Challenge
Schroders, a global investment manager with over 500 billion assets and 5,000+ employees in over 30 countries, faced a significant challenge in scaling and improving their creative operations while ensuring brand consistency. The company's marketing team, which consists of over 500 people, required a solution that could automate and scale the production of creative assets beyond just the creative team. This would allow the team to focus on higher-value creative tasks while meeting the high demands of the marketing team. Additionally, Schroders needed a solution that could centralize and drive efficiencies during the day-to-day creative process—from briefing and feedback rounds to the eventual sign-off of assets. The company also sought to optimize and automate their creative production with a templating model, allowing for more self-sufficiency beyond the creative team.
About The Customer
Schroders is a global investment manager responsible for over 500 billion assets on behalf of its clients. The company is based in 37 different locations and employs over 5,000 people globally, with around 550 people in the marketing team. Schroders is a multi-brand business with a complex brand architecture, creating and managing branding activities for internal initiatives and divisions, each requiring their own unique identity. The company's Branch team, consisting of just three people, manages all brand and creative operations, advertising events, and is responsible for all in-house and external agency activities.
The Solution
Schroders found a solution in Bynder, a digital asset management software. Bynder allowed Schroders to automate and scale the production of creative assets, enabling the creative team to focus on higher-value tasks. The software also helped centralize and drive efficiencies during the day-to-day creative process, from briefing and feedback rounds to the eventual sign-off of assets. Since implementing Bynder in 2019, Schroders has onboarded 1000+ users and completed 1200+ projects in Creative Workflow. The software has also helped Schroders deliver a multi award-winning global campaign and win an award for Best Use of Social Media from Investment Week. Bynder's Creative Workflow has improved Schroders' operations through effective briefing, prioritizing incoming requests, accurate forecasting, and ensuring consistency and quality of work.
Operational Impact
Quantitative Benefit
Related Case Studies.
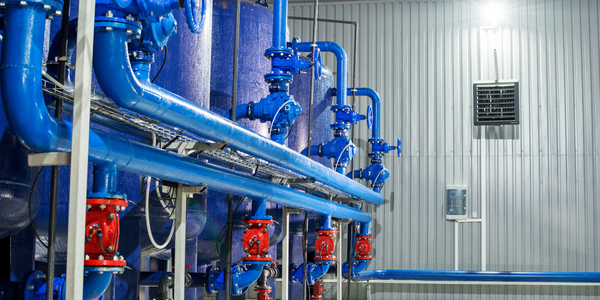
Case Study
Smart Water Filtration Systems
Before working with Ayla Networks, Ozner was already using cloud connectivity to identify and solve water-filtration system malfunctions as well as to monitor filter cartridges for replacements.But, in June 2015, Ozner executives talked with Ayla about how the company might further improve its water systems with IoT technology. They liked what they heard from Ayla, but the executives needed to be sure that Ayla’s Agile IoT Platform provided the security and reliability Ozner required.
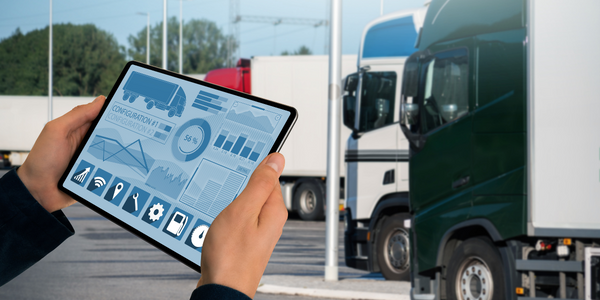
Case Study
IoT enabled Fleet Management with MindSphere
In view of growing competition, Gämmerler had a strong need to remain competitive via process optimization, reliability and gentle handling of printed products, even at highest press speeds. In addition, a digitalization initiative also included developing a key differentiation via data-driven services offers.
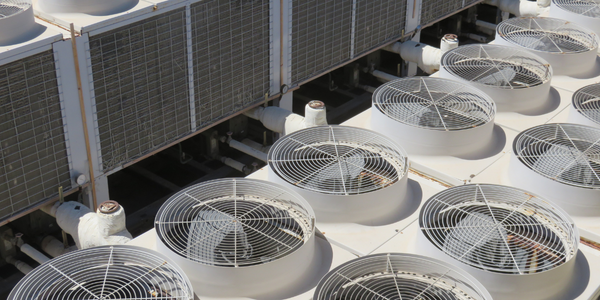
Case Study
Predictive Maintenance for Industrial Chillers
For global leaders in the industrial chiller manufacturing, reliability of the entire production process is of the utmost importance. Chillers are refrigeration systems that produce ice water to provide cooling for a process or industrial application. One of those leaders sought a way to respond to asset performance issues, even before they occur. The intelligence to guarantee maximum reliability of cooling devices is embedded (pre-alarming). A pre-alarming phase means that the cooling device still works, but symptoms may appear, telling manufacturers that a failure is likely to occur in the near future. Chillers who are not internet connected at that moment, provide little insight in this pre-alarming phase.
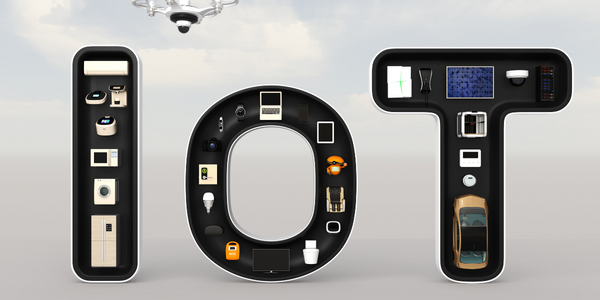
Case Study
Premium Appliance Producer Innovates with Internet of Everything
Sub-Zero faced the largest product launch in the company’s history:It wanted to launch 60 new products as scheduled while simultaneously opening a new “greenfield” production facility, yet still adhering to stringent quality requirements and manage issues from new supply-chain partners. A the same time, it wanted to increase staff productivity time and collaboration while reducing travel and costs.
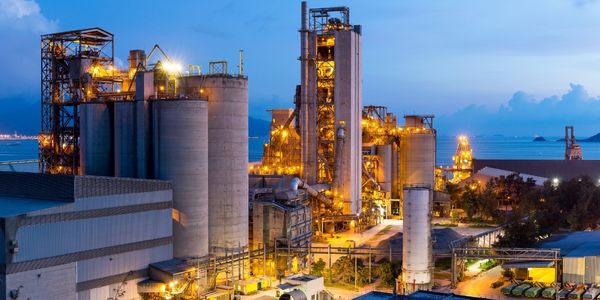
Case Study
System 800xA at Indian Cement Plants
Chettinad Cement recognized that further efficiencies could be achieved in its cement manufacturing process. It looked to investing in comprehensive operational and control technologies to manage and derive productivity and energy efficiency gains from the assets on Line 2, their second plant in India.
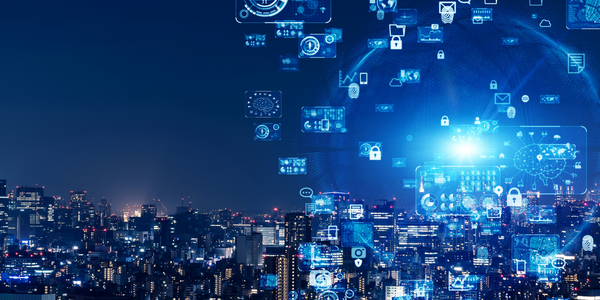
Case Study
Integration of PLC with IoT for Bosch Rexroth
The application arises from the need to monitor and anticipate the problems of one or more machines managed by a PLC. These problems, often resulting from the accumulation over time of small discrepancies, require, when they occur, ex post technical operations maintenance.