Download PDF
Sensorless Motor Control Technology Characterization Using VisSim: A Texas Instruments Case Study
Technology Category
- Analytics & Modeling - Digital Twin / Simulation
- Processors & Edge Intelligence - Embedded & Edge Computers
Applicable Industries
- Automotive
- Electronics
Applicable Functions
- Product Research & Development
Use Cases
- Manufacturing Process Simulation
- Virtual Reality
Services
- System Integration
- Testing & Certification
The Challenge
The C2000 MCU group at Texas Instruments (TI), a global semiconductor design and manufacturing company, was faced with the challenge of characterizing their new software product, InstaSPIN™. This software enables designers to identify, tune, and fully control any type of three-phase, variable speed, sensorless, synchronous or asynchronous motor control system. It uses TI’s new software encoder, a sensorless observer called FAST™ (Flux, Angle, Speed and Torque), which is embedded in the read-only-memory (ROM) of Piccolo devices. Dave Wilson, Senior Motor Systems Engineer with The C2000 Group, was tasked with characterizing the FAST™ observer and developing a datasheet for it. However, the process was slow and tedious due to output variances over time and temperature changes, and it required constant recalibration. Moreover, the hardware he was using was not adequately equipped to test the FAST software.
About The Customer
The customer in this case study is Texas Instruments (TI), a global semiconductor design and manufacturing company with a valuation of 13 billion dollars. TI is known for its groundbreaking advancements in power electronics and microelectronics, with applications in a wide range of fields from appliances to automotive control systems. The C2000 MCU group at TI, which focuses on high-end processing applications like sensorless field oriented motor control, is the specific customer group in this case study. They were tasked with the challenge of characterizing their new software product, InstaSPIN™, which uses TI’s new software encoder, a sensorless observer called FAST™.
The Solution
To overcome the challenge, Mr. Wilson turned to VisSim, a software he had become familiar with four years prior. VisSim provided him with the tools he needed to model fast and accurate motor analog dynamics as well as digital control. It was then able to automatically create C code from the controller portion of his graphical diagram, and download the code to run on the Piccolo target. Using the VisSim JTAG Hotlink in a new synchronous mode that was released in the latest version 9 of the software, Mr. Wilson could run the motor simulation in lock step with the control running on the target in non real-time to verify the FAST outputs against the ideal values of Flux, Angle, Speed, and Torque from the VisSim model. As a result, FAST can be evaluated for ANY brushless motor, no matter how big or small, by simply supplying the simulated voltage and current values to the FAST observer running in ROM on the target.
Operational Impact
Related Case Studies.
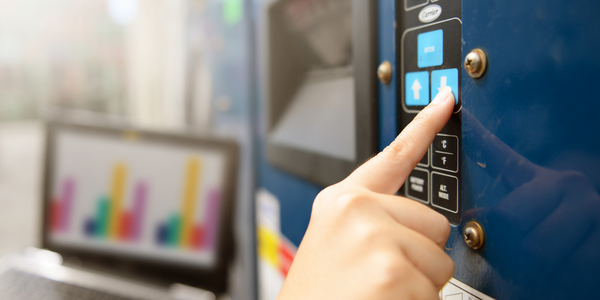
Case Study
Remote Temperature Monitoring of Perishable Goods Saves Money
RMONI was facing temperature monitoring challenges in a cold chain business. A cold chain must be established and maintained to ensure goods have been properly refrigerated during every step of the process, making temperature monitoring a critical business function. Manual registration practice can be very costly, labor intensive and prone to mistakes.
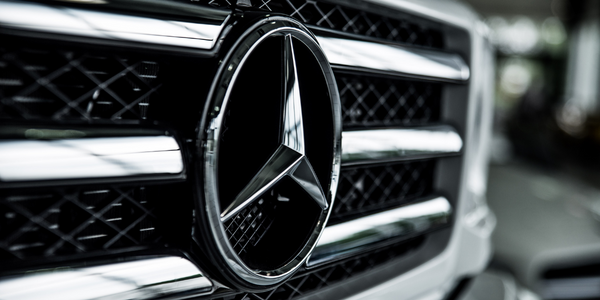
Case Study
Integral Plant Maintenance
Mercedes-Benz and his partner GAZ chose Siemens to be its maintenance partner at a new engine plant in Yaroslavl, Russia. The new plant offers a capacity to manufacture diesel engines for the Russian market, for locally produced Sprinter Classic. In addition to engines for the local market, the Yaroslavl plant will also produce spare parts. Mercedes-Benz Russia and his partner needed a service partner in order to ensure the operation of these lines in a maintenance partnership arrangement. The challenges included coordinating the entire maintenance management operation, in particular inspections, corrective and predictive maintenance activities, and the optimizing spare parts management. Siemens developed a customized maintenance solution that includes all electronic and mechanical maintenance activities (Integral Plant Maintenance).