Download PDF
Shiva Tool Tech Achieves 80% Time Reduction in Die Design with Altair Inspire Cast
Technology Category
- Analytics & Modeling - Digital Twin / Simulation
- Functional Applications - Manufacturing Execution Systems (MES)
Applicable Industries
- Automotive
- Equipment & Machinery
Applicable Functions
- Maintenance
- Product Research & Development
Use Cases
- Manufacturing Process Simulation
- Virtual Prototyping & Product Testing
Services
- System Integration
- Testing & Certification
The Challenge
Shiva Tool Tech, an automotive manufacturing company based in Pune, India, specializes in designing and manufacturing gravity die casting (GDC), low-pressure die casting (LPDC), and high-pressure die casting (HPDC) Dies. The company supports customers from the manufacturing process design to the production stage. However, the company faced challenges in obtaining a defect-free die design. The casting die designs were developed based on years of experience for components received from their customers in the form of computer-aided design (CAD) and engineering drafts. Once the die for the casting was designed, it was manufactured and assembled at their facility. The die was then sent to the customer for carrying out the physical casting trial. The cast part manufactured from the new dies was sent back to Shiva Tool Tech with an inspection report and defects identified. The die design was then modified to eliminate the defects. This entire process took about 3-4 physical iterations to get a defect-free die design. The company realized the value of simulation software in optimizing this design and manufacturing process to save time and money. However, outsourcing the simulations were expensive and time-consuming.
About The Customer
Shiva Tool Tech is an industrial powerhouse based in Pune, India, with a focus on automotive manufacturing. With over 25 years of experience in designing and manufacturing of gravity die casting (GDC), low-pressure die casting (LPDC), high-pressure die casting (HPDC) Dies, the company supports customers from manufacturing process design to the production stage. Manufacturing processes include milling, drilling, hardening, grinding, Computer Numerical Control (CNC) machining, Electrical Discharge Machining (EDM), inspection and polishing to get the final assembly of the casting die. The company designs and manufactures casting dies for automotive and non-automotive components like brackets, crankcase, housing, cylinder heads, compressor housings, manifolds, alloy wheels, etc.
The Solution
To overcome the challenges, Shiva Tool Tech decided to bring the expertise in-house by investing in simulation software. They chose Altair’s casting simulation software Inspire Cast which met their requirements for ease of use, accuracy of results, speed of computational analysis, rich visualization of results while remaining within budget considerations. The updated process at Shiva Tool Tech now involves Inspire Cast in two phases. On receiving the CAD of the casting part, the model is taken to Inspire Cast for running simulations with a virtual gating system on the part. Once the gating location is fixed based on the desired simulation results, the shot model for the component is designed in CAD. The shot model is then taken to Inspire Cast for carrying out the detailed casting simulation to understand the occurring defects. The methodology is modified to reduce or eliminate defects by changing the gate size, shape and with additions of risers and chillers.
Operational Impact
Quantitative Benefit
Related Case Studies.
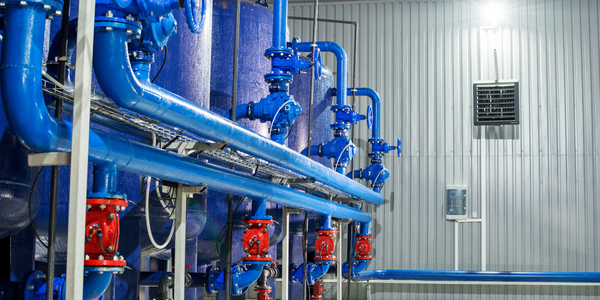
Case Study
Smart Water Filtration Systems
Before working with Ayla Networks, Ozner was already using cloud connectivity to identify and solve water-filtration system malfunctions as well as to monitor filter cartridges for replacements.But, in June 2015, Ozner executives talked with Ayla about how the company might further improve its water systems with IoT technology. They liked what they heard from Ayla, but the executives needed to be sure that Ayla’s Agile IoT Platform provided the security and reliability Ozner required.
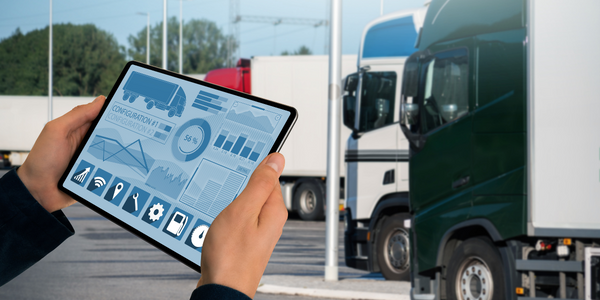
Case Study
IoT enabled Fleet Management with MindSphere
In view of growing competition, Gämmerler had a strong need to remain competitive via process optimization, reliability and gentle handling of printed products, even at highest press speeds. In addition, a digitalization initiative also included developing a key differentiation via data-driven services offers.
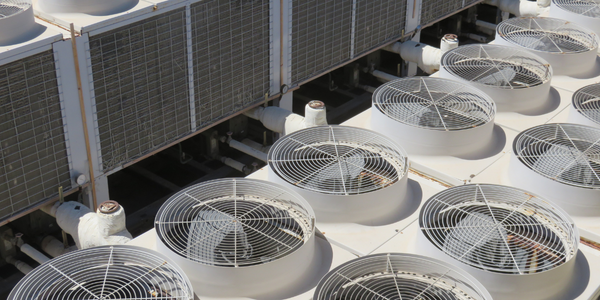
Case Study
Predictive Maintenance for Industrial Chillers
For global leaders in the industrial chiller manufacturing, reliability of the entire production process is of the utmost importance. Chillers are refrigeration systems that produce ice water to provide cooling for a process or industrial application. One of those leaders sought a way to respond to asset performance issues, even before they occur. The intelligence to guarantee maximum reliability of cooling devices is embedded (pre-alarming). A pre-alarming phase means that the cooling device still works, but symptoms may appear, telling manufacturers that a failure is likely to occur in the near future. Chillers who are not internet connected at that moment, provide little insight in this pre-alarming phase.
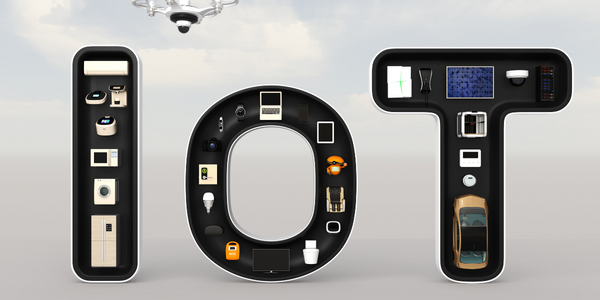
Case Study
Premium Appliance Producer Innovates with Internet of Everything
Sub-Zero faced the largest product launch in the company’s history:It wanted to launch 60 new products as scheduled while simultaneously opening a new “greenfield” production facility, yet still adhering to stringent quality requirements and manage issues from new supply-chain partners. A the same time, it wanted to increase staff productivity time and collaboration while reducing travel and costs.
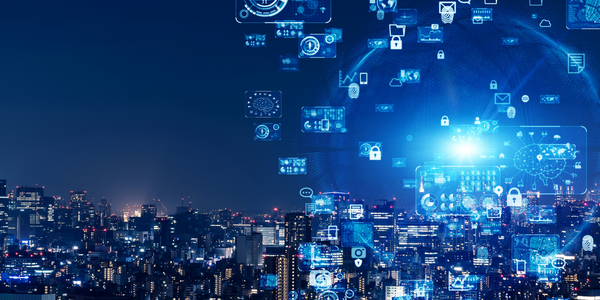
Case Study
Integration of PLC with IoT for Bosch Rexroth
The application arises from the need to monitor and anticipate the problems of one or more machines managed by a PLC. These problems, often resulting from the accumulation over time of small discrepancies, require, when they occur, ex post technical operations maintenance.
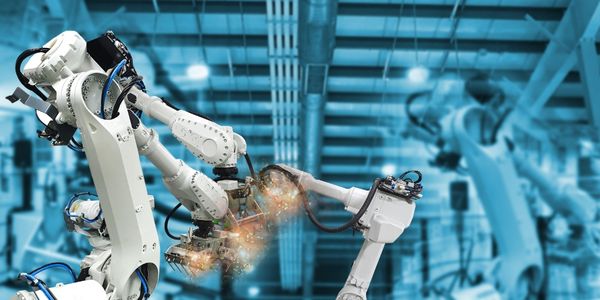
Case Study
Robot Saves Money and Time for US Custom Molding Company
Injection Technology (Itech) is a custom molder for a variety of clients that require precision plastic parts for such products as electric meter covers, dental appliance cases and spools. With 95 employees operating 23 molding machines in a 30,000 square foot plant, Itech wanted to reduce man hours and increase efficiency.