Download PDF
Software Project Enriches Controls and Culture
Technology Category
- Functional Applications - Manufacturing Execution Systems (MES)
Applicable Industries
- Electronics
Applicable Functions
- Discrete Manufacturing
- Quality Assurance
Use Cases
- Manufacturing System Automation
Services
- System Integration
The Challenge
SMART Modular Technologies’ 10-year-old memory chip back-end plant in Brazil was stepping up to implement a modern comprehensive manufacturing execution system (MES). The timing was to succeed as a second source for a new product and more to come. As SMART continued its thrust into the mobile market for memory, they recognized that the current controls would no longer suffice. The plant was using an internally-developed WIP tracking system plus Excel and paper. This system did not provide close yield monitoring. SMART could not easily analyze data to prevent defects. Lot traceability was a manual and tedious task, and operators had to choose the right tools and recipe. With new products and more volume, this would not be sufficient. So in 2013, the Atibaia IC facility began looking for a system that would do far more than its current software.
About The Customer
SMART Modular Technologies (SMART) in Atibaia (São Paulo) started out as a memory module maker in 1988 and opened the plant to process, assemble, package and test DRAM ICs early in 2006. Beyond the SMART module company, it has many other global, regional and local Brazilian customers. The facility has clean rooms up to class 10 and introduced die stacking technology in 2009 and flash products in 2010. SMART expanded the Atibaia facility in 2014 after entering the market for mobile device memory chips. The plant makes a mix of sophisticated memory products including: DRAM and LPDRAM, eMCP, eMMC, and microSD.
The Solution
The team identified four systems and evaluated them over the course of eight months. They developed a complete decision matrix that included characteristics about investment, culture and technology. They visited customers of the top suppliers at facilities around the world. Each customer talked about what they are doing with the system; how the supplier helped with their project and the benefits once it was fully live. One supplier was eliminated because the user interface was not friendly. A comparison of the other three led to the selection of an MES supplier that uses Microsoft SQL server platforms, matching SMART’s other systems. They also won on the basis of culture and understanding.
Operational Impact
Related Case Studies.
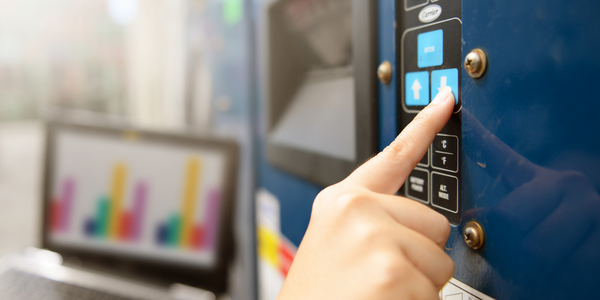
Case Study
Remote Temperature Monitoring of Perishable Goods Saves Money
RMONI was facing temperature monitoring challenges in a cold chain business. A cold chain must be established and maintained to ensure goods have been properly refrigerated during every step of the process, making temperature monitoring a critical business function. Manual registration practice can be very costly, labor intensive and prone to mistakes.
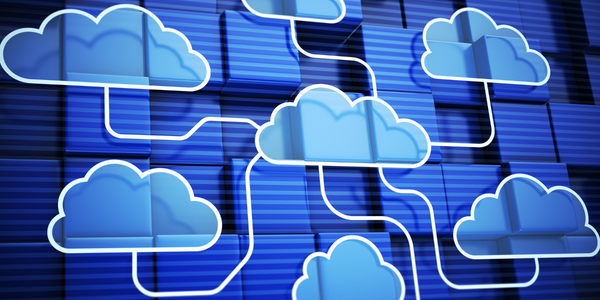
Case Study
Cloud Solution for Energy Management Platform-Schneider Electric
Schneider Electric required a cloud solution for its energy management platform to manage high computational operations, which were essential for catering to client requirements. As the business involves storage and analysis of huge amounts of data, the company also needed a convenient and scalable storage solution to facilitate operations efficiently.
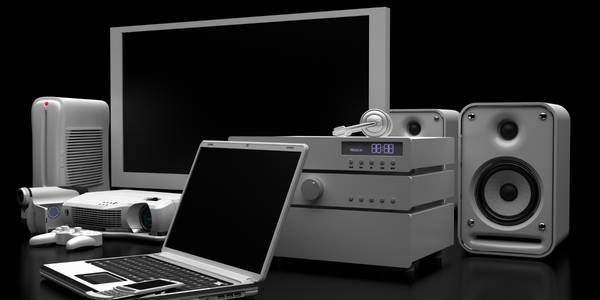
Case Study
Leveraging the IoT to Gain a Competitive Edge in International Competition
Many large manufacturers in and outside Japan are competing for larger market share in the same space, expecting a growing demand for projectors in the areas of entertainment, which requires glamor and strong visual performance as well as digital signage that can attract people’s attention. “It is becoming more and more difficult to differentiate ourselves with stand-alone hardware products,” says Kazuyuki Kitagawa, Director of Service & Support at Panasonic AVC Networks. “In order for Panasonic to grow market share and overall business, it is essential for us to develop solutions that deliver significant added value.” Panasonic believes projection failure and quality deterioration should never happen. This is what and has driven them to make their projectors IoT-enabled. More specifically, Panasonic has developed a system that collects data from projectors, visualizes detailed operational statuses, and predicts issues and address them before failure occurs. Their projectors are embedded with a variety of sensors that measure power supply, voltage, video input/ output signals, intake/exhaust air temperatures, cooling fan operations, and light bulb operating time. These sensors have been used to make the projector more intelligent, automatically suspending operation when the temperature rises excessively, and automatically switching light bulbs. Although this was a great first step, Panasonic projectors were still not equipped with any capability to send the data over a network.