Download PDF
Standardization of Model Building Process with Meshing and Weld Creation Automation at F.tech R&D North America
Technology Category
- Robots - Autonomous Guided Vehicles (AGV)
Applicable Industries
- Automotive
- Equipment & Machinery
Applicable Functions
- Product Research & Development
- Quality Assurance
Use Cases
- Leasing Finance Automation
- Material Handling Automation
Services
- Testing & Certification
The Challenge
F.tech R&D North America, a Tier-1 automotive systems supplier, was facing challenges in standardizing their model building process with meshing and different types of weld creation automation. The complexities in vehicle design and development, including the cost of prototypes, compliance with safety standards, and emissions, posed many challenges for the engineers. The Computer Aided Engineering (CAE) team at F.tech R&D North America was struggling with tedious tasks related to model build and geometry preparation for weld creation. The need for a solution that could streamline these processes, eliminate human errors, increase the accuracy of analysis data, and save valuable development time was evident.
About The Customer
F.tech R&D North America, headquartered in Japan with international locations, is a Tier-1 automotive systems supplier. The company provides a variety of automotive components such as subframes, suspension control arms, and pedals to Original Equipment Manufacturers (OEM). F.tech R&D North America based in Troy, OH, has full in-house research and development capabilities for Design, Computer Aided Engineering (CAE), prototyping and testing. This team embraces virtual design validation, making extensive use of simulation tools, including Altair’s HyperWorks™ software suite.
The Solution
Altair developed a customized solution for F.tech R&D North America, known as F.tech–PAS (F.tech -Pre-processing Automation Solution). This solution was developed using Altair’s Model Mesher Director (MMD) PSO (Packaged Solution Offering). The F.tech-PAS is a streamlined toolset which aids F.tech engineers in CAE meshing and assembly from CAD to solver deck. It includes key features such as launching the tool from Altair HyperMesh™, capturing best model building practices, and automating the different steps in the meshing and welding processes. Once the model file is imported, it is simplified by geometry clean-up and meshing, creating welds and washers. The engineers are now able to efficiently simplify and de-feature the geometry, accelerate the meshing and weld creation process, and automatically assign materials & properties. After the model is complete it is ready for analysis with Altair OptiStruct™ or an alternate solver.
Operational Impact
Quantitative Benefit
Related Case Studies.
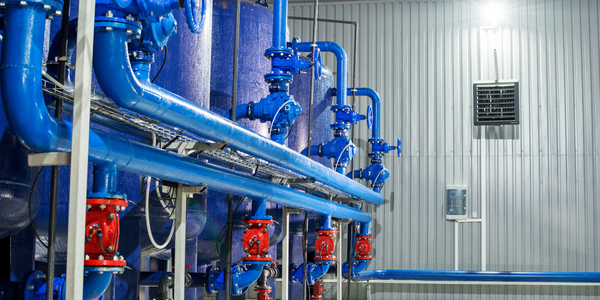
Case Study
Smart Water Filtration Systems
Before working with Ayla Networks, Ozner was already using cloud connectivity to identify and solve water-filtration system malfunctions as well as to monitor filter cartridges for replacements.But, in June 2015, Ozner executives talked with Ayla about how the company might further improve its water systems with IoT technology. They liked what they heard from Ayla, but the executives needed to be sure that Ayla’s Agile IoT Platform provided the security and reliability Ozner required.
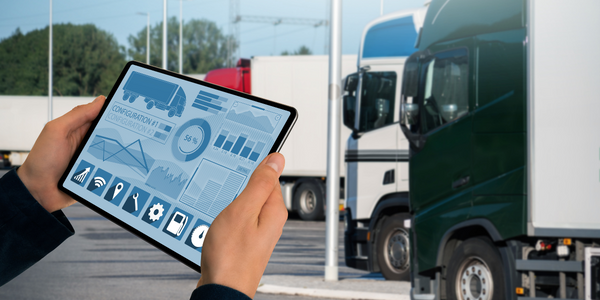
Case Study
IoT enabled Fleet Management with MindSphere
In view of growing competition, Gämmerler had a strong need to remain competitive via process optimization, reliability and gentle handling of printed products, even at highest press speeds. In addition, a digitalization initiative also included developing a key differentiation via data-driven services offers.
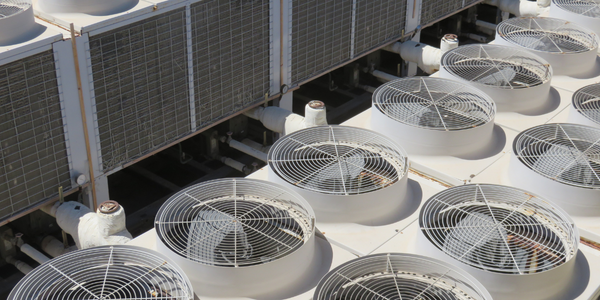
Case Study
Predictive Maintenance for Industrial Chillers
For global leaders in the industrial chiller manufacturing, reliability of the entire production process is of the utmost importance. Chillers are refrigeration systems that produce ice water to provide cooling for a process or industrial application. One of those leaders sought a way to respond to asset performance issues, even before they occur. The intelligence to guarantee maximum reliability of cooling devices is embedded (pre-alarming). A pre-alarming phase means that the cooling device still works, but symptoms may appear, telling manufacturers that a failure is likely to occur in the near future. Chillers who are not internet connected at that moment, provide little insight in this pre-alarming phase.
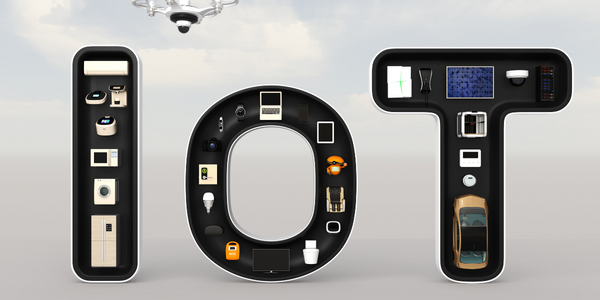
Case Study
Premium Appliance Producer Innovates with Internet of Everything
Sub-Zero faced the largest product launch in the company’s history:It wanted to launch 60 new products as scheduled while simultaneously opening a new “greenfield” production facility, yet still adhering to stringent quality requirements and manage issues from new supply-chain partners. A the same time, it wanted to increase staff productivity time and collaboration while reducing travel and costs.
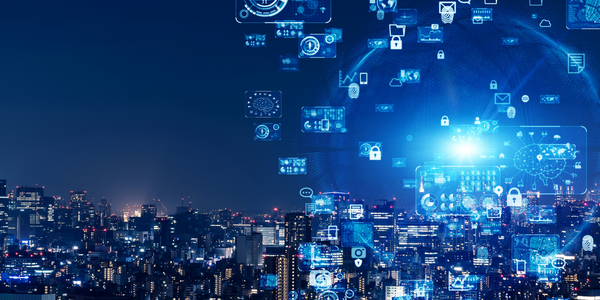
Case Study
Integration of PLC with IoT for Bosch Rexroth
The application arises from the need to monitor and anticipate the problems of one or more machines managed by a PLC. These problems, often resulting from the accumulation over time of small discrepancies, require, when they occur, ex post technical operations maintenance.
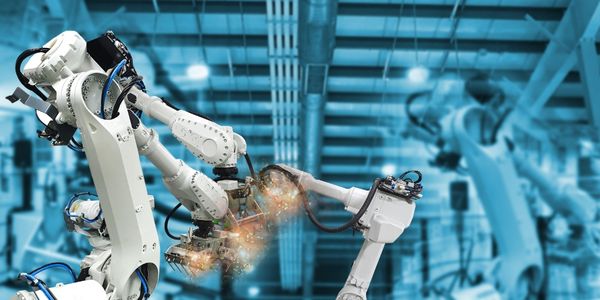
Case Study
Robot Saves Money and Time for US Custom Molding Company
Injection Technology (Itech) is a custom molder for a variety of clients that require precision plastic parts for such products as electric meter covers, dental appliance cases and spools. With 95 employees operating 23 molding machines in a 30,000 square foot plant, Itech wanted to reduce man hours and increase efficiency.