Download PDF
State Agencies Improve Processes and Share Information in Real Time
Technology Category
- Application Infrastructure & Middleware - API Integration & Management
- Application Infrastructure & Middleware - Data Exchange & Integration
- Platform as a Service (PaaS) - Connectivity Platforms
- Platform as a Service (PaaS) - Data Management Platforms
Applicable Functions
- Logistics & Transportation
- Procurement
- Quality Assurance
Use Cases
- Fraud Detection
- Inventory Management
- Process Control & Optimization
- Supply Chain Visibility
- Track & Trace of Assets
Services
- Cloud Planning, Design & Implementation Services
- Data Science Services
- Software Design & Engineering Services
- System Integration
The Challenge
The Georgia Technology Authority (GTA) was faced with the challenge of improving the availability of data between federal, state, county, and local agencies as well as external partners. They needed to ensure easy interoperability between systems and applications while meeting local, state, and federal reporting and compliance requirements. The agencies were previously limited by point-to-point, hardcoded integrations, siloed systems, and manual processes that were paper-based and slow. This made it difficult for them to share information securely in real time and streamline their services to better meet citizen needs.
About The Customer
The Georgia Technology Authority (GTA) is an organization that manages the delivery of IT infrastructure services to 85 executive branch agencies and managed network services to 1,400 state and local government entities in the U.S. The authority’s strategic vision is to create a transparent, integrated enterprise where technology decisions are made with the citizen in mind. Its mission is to connect Georgians to their government. GTA's main objective is to introduce new technology to state agencies to improve business processes and expand data-sharing opportunities.
The Solution
GTA used Software AG technology as a key component for the State IT Roadmap. They implemented the ARIS Business Process Analysis Platform, webMethods Integration Platform, and webMethods Business Process Management Platform. webMethods became the standard platform for application integration, allowing agencies to share information securely in real time. ARIS and webMethods were used to model, automate, and optimize business processes. The Data Sharing Services (DSS) architecture based on webMethods served as a common point of integration among city, county, and circuit agencies to state and federal entities. This allowed for easier and faster information sharing and reduced complexity for inter- and intra-agency integration.
Operational Impact
Quantitative Benefit
Related Case Studies.
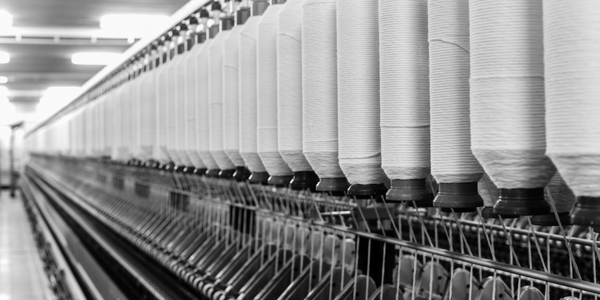
Case Study
IoT Applications and Upgrades in Textile Plant
At any given time, the textile company’s manufacturing facility has up to 2,000 textile carts in use. These carts are pushed from room to room, carrying materials or semi-finished products. Previously, a paper with a hand-written description was attached to each cart. This traditional method of processing made product tracking extremely difficult. Additionally, making sure that every cart of materials or semi-finished products went to its correct processing work station was also a problem. Therefore, the company desired an intelligent solution for tracking assets at their factories. They also wanted a solution that would help them collect process data so they could improve their manufacturing efficiency.
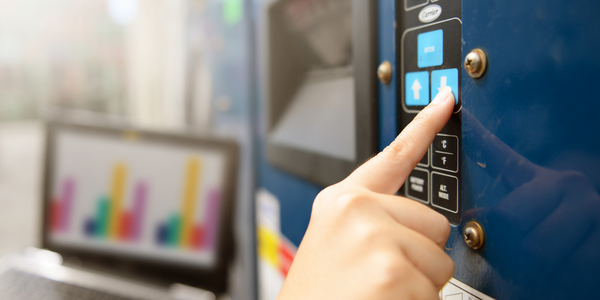
Case Study
Remote Temperature Monitoring of Perishable Goods Saves Money
RMONI was facing temperature monitoring challenges in a cold chain business. A cold chain must be established and maintained to ensure goods have been properly refrigerated during every step of the process, making temperature monitoring a critical business function. Manual registration practice can be very costly, labor intensive and prone to mistakes.
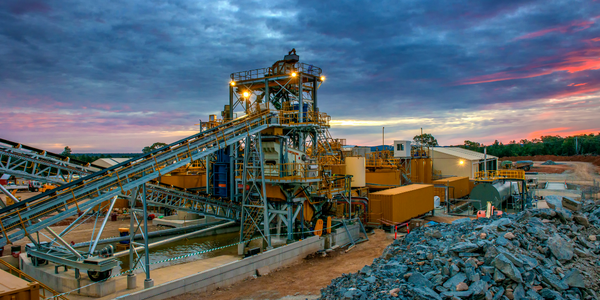
Case Study
Goldcorp: Internet of Things Enables the Mine of the Future
Goldcorp is committed to responsible mining practices and maintaining maximum safety for its workers. At the same time, the firm is constantly exploring ways to improve the efficiency of its operations, extend the life of its assets, and control costs. Goldcorp needed technology that can maximize production efficiency by tracking all mining operations, keep employees safe with remote operations and monitoring of hazardous work areas and control production costs through better asset and site management.
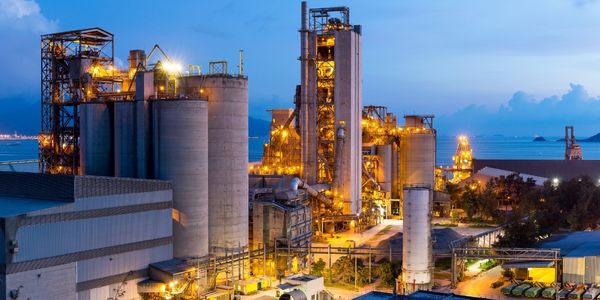
Case Study
System 800xA at Indian Cement Plants
Chettinad Cement recognized that further efficiencies could be achieved in its cement manufacturing process. It looked to investing in comprehensive operational and control technologies to manage and derive productivity and energy efficiency gains from the assets on Line 2, their second plant in India.
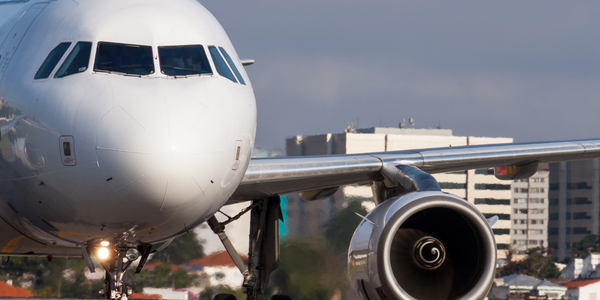
Case Study
Airbus Soars with Wearable Technology
Building an Airbus aircraft involves complex manufacturing processes consisting of thousands of moving parts. Speed and accuracy are critical to business and competitive advantage. Improvements in both would have high impact on Airbus’ bottom line. Airbus wanted to help operators reduce the complexity of assembling cabin seats and decrease the time required to complete this task.