Download PDF
Subros Optimizes Product Designs with Altair HyperWorks, Reducing Simulation Time and Prototyping Costs
Technology Category
- Analytics & Modeling - Digital Twin / Simulation
- Sensors - Voltage Sensors
Applicable Industries
- Automotive
- Chemicals
Applicable Functions
- Logistics & Transportation
- Product Research & Development
Use Cases
- Manufacturing Process Simulation
- Time Sensitive Networking
Services
- Testing & Certification
The Challenge
Subros Limited, a leading manufacturer of thermal products for automotive applications in India, faced significant challenges in meeting product delivery deadlines with agreed quality benchmarks. As a major supplier of AC units to various automotive segments, Subros had to continually upgrade their products to match the evolving designs of vehicles. The pressure of product development timelines was immense, as the launch time of vehicles was crucial for manufacturers. Subros initially used a CAE software tool for simulation to save time in the product development cycle. However, the software was not user-friendly, took a long time to simulate, and was prone to human errors, leading to further delays in product development and delivery. The team needed a robust, quick, reliable, and user-friendly simulation software product to overcome these issues.
About The Customer
Subros Limited, founded in 1985, is a joint venture public limited company with 40% ownership by the Suri family of India and 13% ownership each by Denso Corporation and Suzuki Motor Corporation. Subros is the leading manufacturer of thermal products for automotive applications in India, operating in technical collaboration with Denso. The company has grown from a capacity of 15,000 AC units in 1985 to being the largest and only integrated manufacturing unit in India for Auto Air Conditioning systems. Subros manufactures Compressors, Condensers, Heat Exchangers, and all connecting elements required to complete the AC loop. Their product line caters to all vehicle segments such as Passenger Vehicles, Buses, Trucks, Refrigeration Transport, Off- roaders, and Railways. Subros has manufacturing plants at Noida (2), Manesar, Pune, Chennai, and Sanand with an annual capacity of 1.5 million AC kits. They also have a well-equipped R&D Center and Tool Room in Noida.
The Solution
Subros turned to Altair HyperWorks to address their challenges. The company has been using the Altair suite of products for over a decade. Initially, Subros used Altair’s pre-processor tool HyperMesh coupled with other industry solvers. As they learned more about the capabilities of the Altair suite, they transitioned completely towards RADIOSS and OptiStruct solver for structural analysis. Currently, Subros extensively uses Altair HyperWorks 14.0, which includes HyperMesh, HyperView, HyperGraph, RADIOSS, OptiStruct, MotionView, MotionSolve, and solidThinking Inspire. The team also intermittently uses Altair AcuSolve, SimLab, and HyperStudy as required. The Subros team uses Altair solutions to carry out various types of analyses to evaluate structural integrity. The software suite has enabled them to perform structural and multi-body dynamic analysis without worrying about errors, positively impacting the product development cycle time and cost of prototypes and samples.
Operational Impact
Quantitative Benefit
Related Case Studies.
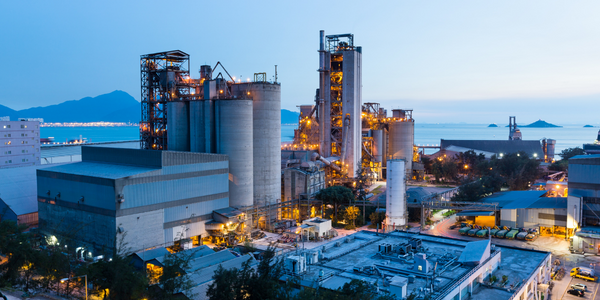
Case Study
Honeywell - Tata Chemicals Improves Data Accessibility with OneWireless
Tata was facing data accessibility challenges in the cement plant control room tapping signals from remote process control areas and other distant locations, including the gas scrubber. Tata needed a wireless solution to extend its control network securely to remote locations that would also provide seamless communication with existing control applications.
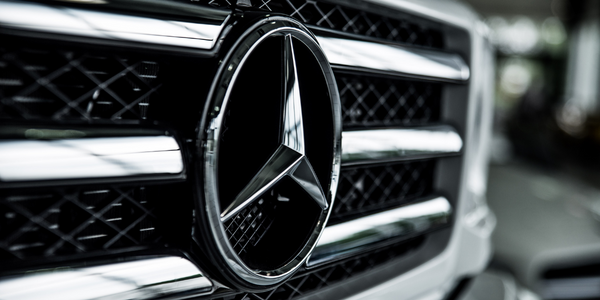
Case Study
Integral Plant Maintenance
Mercedes-Benz and his partner GAZ chose Siemens to be its maintenance partner at a new engine plant in Yaroslavl, Russia. The new plant offers a capacity to manufacture diesel engines for the Russian market, for locally produced Sprinter Classic. In addition to engines for the local market, the Yaroslavl plant will also produce spare parts. Mercedes-Benz Russia and his partner needed a service partner in order to ensure the operation of these lines in a maintenance partnership arrangement. The challenges included coordinating the entire maintenance management operation, in particular inspections, corrective and predictive maintenance activities, and the optimizing spare parts management. Siemens developed a customized maintenance solution that includes all electronic and mechanical maintenance activities (Integral Plant Maintenance).
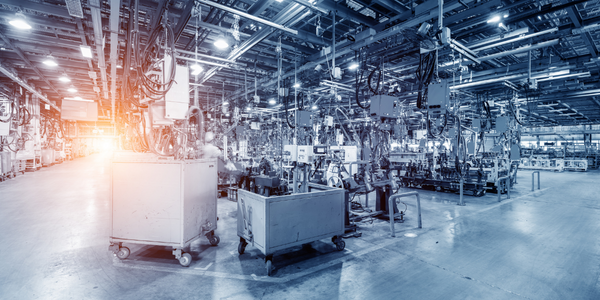
Case Study
Advanced Elastomer Systems Upgrades Production
In order to maintain its share of the international market for thermoplastic elastomers AES recently expanded its Florida plant by adding a new production line. While the existing lines were operating satisfactorily using a PROVOX distributed control system with traditional analog I/O, AES wanted advanced technology on the new line for greater economy, efficiency, and reliability. AES officials were anxious to get this line into production to meet incoming orders, but two hurricanes slowed construction.