Download PDF
Sumitomo Corporation Asia & Oceania modernizes business processes by moving from Microsoft BizTalk to Anypoint Platform in just six weeks
Technology Category
- Platform as a Service (PaaS) - Connectivity Platforms
- Platform as a Service (PaaS) - Data Management Platforms
Applicable Functions
- Procurement
- Logistics & Transportation
Use Cases
- Process Control & Optimization
- Supply Chain Visibility
Services
- System Integration
- Software Design & Engineering Services
The Challenge
Sumitomo Corporation Asia & Oceania (SCAO) was facing frequent system outages and data loss due to issues with their Microsoft BizTalk integration platform. This was causing significant disruption to their business operations, including the exchange of vital business documentation such as purchase orders, purchase order confirmations, and shipping notifications. The system required a hard restart every three days, leading to high support costs and interruptions to customer-facing business operations. The issues affecting SCAO’s core business processes and overall customer satisfaction necessitated an immediate replacement of the current system. Management at SCAO wanted to ensure the replacement was quick to deploy and seamless to end users.
About The Customer
Sumitomo Corporation Asia & Oceania (SCAO) is a part of the Sumitomo Corporation, a leading global trading company with 133 locations in 66 countries and 22 locations in Japan. The company is a major player in the global exchange of goods, services, and technology. SCAO is headquartered in Singapore and operates across a wide range of industries. The company exchanges vital business documentation with trading partners, including purchase orders, purchase order confirmations, and shipping notifications. These processes were traditionally supported by Microsoft BizTalk’s integration platform.
The Solution
SCAO conducted a technology evaluation process and selected MuleSoft's Anypoint Platform over three other competing solutions including the incumbent, Microsoft BizTalk. The main criteria for selection were speed of development, ease of deployment, manageability, and cost effectiveness. With the goal of connecting bespoke purchasing systems to each other and to a centralized Oracle Database, SCAO evaluated vendors on their ability to deliver rich data and application integration capabilities with minimal custom code. MuleSoft's Anypoint Studio and Anypoint DataMapper provided the powerful graphical tooling SCAO required to rapidly develop and deliver their BizTalk replacement solution in 6 weeks. MuleSoft's 120+ Anypoint Connectors, including JDBC and Websphere MQ, delivered out-of-the-box extensibility to key endpoints in SCAO's present and future IT landscape. This ability to eliminate friction with a complete and future-proof solution made Anypoint Platform unique.
Operational Impact
Quantitative Benefit
Related Case Studies.
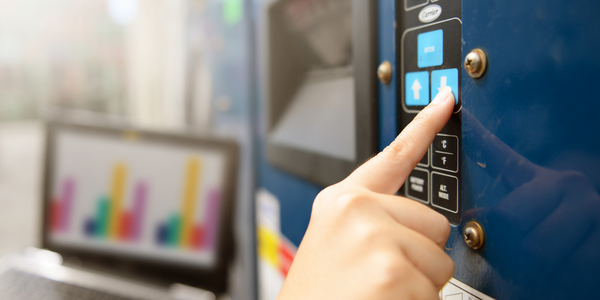
Case Study
Remote Temperature Monitoring of Perishable Goods Saves Money
RMONI was facing temperature monitoring challenges in a cold chain business. A cold chain must be established and maintained to ensure goods have been properly refrigerated during every step of the process, making temperature monitoring a critical business function. Manual registration practice can be very costly, labor intensive and prone to mistakes.
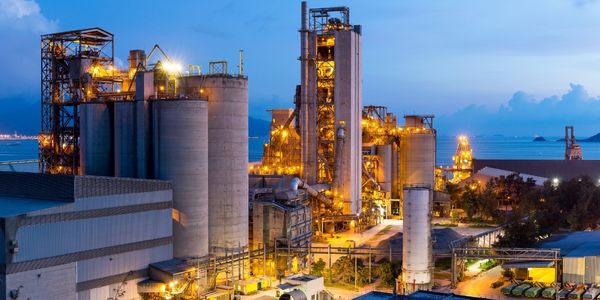
Case Study
System 800xA at Indian Cement Plants
Chettinad Cement recognized that further efficiencies could be achieved in its cement manufacturing process. It looked to investing in comprehensive operational and control technologies to manage and derive productivity and energy efficiency gains from the assets on Line 2, their second plant in India.
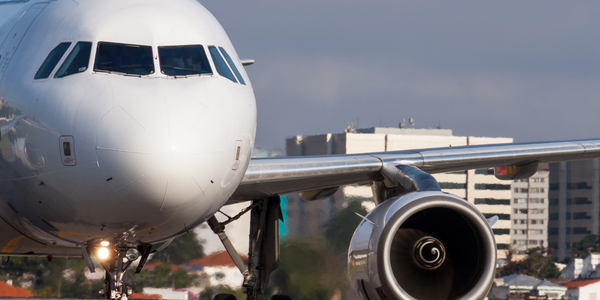
Case Study
Airbus Soars with Wearable Technology
Building an Airbus aircraft involves complex manufacturing processes consisting of thousands of moving parts. Speed and accuracy are critical to business and competitive advantage. Improvements in both would have high impact on Airbus’ bottom line. Airbus wanted to help operators reduce the complexity of assembling cabin seats and decrease the time required to complete this task.
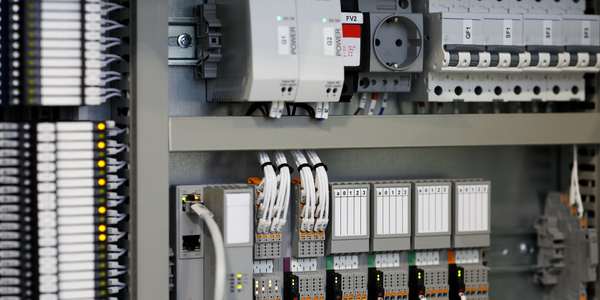
Case Study
Improving Production Line Efficiency with Ethernet Micro RTU Controller
Moxa was asked to provide a connectivity solution for one of the world's leading cosmetics companies. This multinational corporation, with retail presence in 130 countries, 23 global braches, and over 66,000 employees, sought to improve the efficiency of their production process by migrating from manual monitoring to an automatic productivity monitoring system. The production line was being monitored by ABB Real-TPI, a factory information system that offers data collection and analysis to improve plant efficiency. Due to software limitations, the customer needed an OPC server and a corresponding I/O solution to collect data from additional sensor devices for the Real-TPI system. The goal is to enable the factory information system to more thoroughly collect data from every corner of the production line. This will improve its ability to measure Overall Equipment Effectiveness (OEE) and translate into increased production efficiencies. System Requirements • Instant status updates while still consuming minimal bandwidth to relieve strain on limited factory networks • Interoperable with ABB Real-TPI • Small form factor appropriate for deployment where space is scarce • Remote software management and configuration to simplify operations