Download PDF
SYSPRO Helps to Evolve Life and Science with Fisher Scientific
Technology Category
- Analytics & Modeling - Data-as-a-Service
- Functional Applications - Enterprise Resource Planning Systems (ERP)
Applicable Industries
- Healthcare & Hospitals
- Life Sciences
Applicable Functions
- Business Operation
- Quality Assurance
Use Cases
- Inventory Management
- Predictive Maintenance
- Process Control & Optimization
Services
- Software Design & Engineering Services
- System Integration
The Challenge
The diversity of companies falling under the Fisher Scientific International umbrella continues to be a challenge to effective corporate management. While each Fisher Scientific unit operates as an independent entity, the Fisher Scientific management team realizes that corporate control and economies of scale are necessary to enhance corporate profits, maximize operations, enhance quality and improve customer service. In an effort to facilitate proactive corporate decision-making, boost overall corporate efficiency and quality, and maximize customer service, the management team established common corporate software standards – ones that could eventually be adopted by all Fisher Scientific units. It was felt that software uniformity would facilitate efficiency as well as cost-containment. It would also streamline employee training, minimize the impact of employee turnover and ease software maintenance by Fisher Scientific’s IT department. In addition, standardized software would produce uniform data and reports, as well as provide the ability to generate customized reports – all necessary to maximize corporate control and decision-making. Moreover, common software standards would enhance management’s ability to conduct sophisticated research on sales and market trends.
About The Customer
Fisher Scientific International Inc., headquartered in Portsmouth, NH, is a worldwide leader in the design, manufacturing and sales of the highest quality life science and analytical products. The company produces thousands of lines of specialty and state-of-the-art laboratory products for the clinical, research and industrial markets. Fisher Scientific’s products basically fall into three categories: Clinical Diagnostics, Labware and Life Sciences, and Laboratory Equipment. With annual revenues exceeding one billion dollars, Fisher Scientific’s rapid growth has come from several fronts. Sales have grown as a result of rising worldwide expenditures on medical research and the demand for more sophisticated medical instrumentation and lab supplies to improve the speed, accuracy and cost-containment of the research and diagnostic testing. Fisher Scientific has also grown through worldwide acquisition. Today, Fisher Scientific consists of more than 50 different companies located around the globe. The majority of these companies can be classified as small- to mid-size manufacturing businesses (SMB), with unit sales typically ranging from $3 million to $200 million. While many of the Fisher Scientific International companies are single-site operations, some are characterized by multiple facilities. Additionally, many of the companies employ diverse manufacturing methodologies. Some units make and engineer product to order, while others build product to stock based upon sales forecasts. Still others employ a combination of methodologies, or what can be characterized as “mixed-mode” manufacturing.
The Solution
Jerry Bean, Fisher Scientific’s Corporate Director of MIS, faced the challenge of selecting software that would meet the highly diversified needs of the various Fisher Scientific International units. After extensive research, he selected a software solution that was currently being successfully utilized by two Fisher Scientific units. He chose Microsoft’s SQL Server 2000 platform and SYSPRO enterprise software offered through SYSPRO reseller Sutton Software, Inc. While Fisher Scientific International is a “billion dollar company,” many of the company’s 50+ units fall into the small- to mid-range manufacturing category, with individual sales ranging from $3 to $200 million. The choice of SYSPRO enterprise business software was partly based on the fact that the solution is designed for single and multi-site units in the small- to mid-range manufacturing category. Bean’s choice was also based on the SYSPRO ability to handle all the diverse manufacturing methodologies employed by different Fisher Scientific units. The software easily accommodates: make-to-stock; make-to-order; engineer-to-order and mixed mode manufacturing. Additionally, the software features full accounting functionality and supports the high volume distribution requirements characteristic of many of the units. Bean also considered the global nature of Fisher Scientific’s operations and the fact that SYSPRO translates to French and Spanish, as well as English.
Operational Impact
Quantitative Benefit
Related Case Studies.
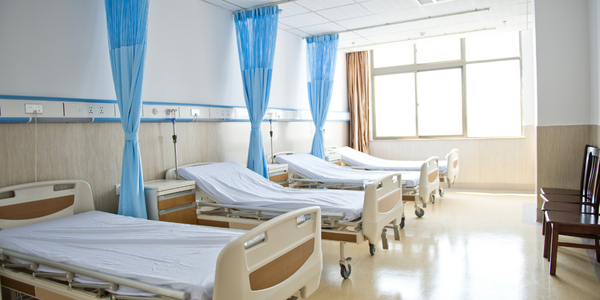
Case Study
Hospital Inventory Management
The hospital supply chain team is responsible for ensuring that the right medical supplies are readily available to clinicians when and where needed, and to do so in the most efficient manner possible. However, many of the systems and processes in use at the cancer center for supply chain management were not best suited to support these goals. Barcoding technology, a commonly used method for inventory management of medical supplies, is labor intensive, time consuming, does not provide real-time visibility into inventory levels and can be prone to error. Consequently, the lack of accurate and real-time visibility into inventory levels across multiple supply rooms in multiple hospital facilities creates additional inefficiency in the system causing over-ordering, hoarding, and wasted supplies. Other sources of waste and cost were also identified as candidates for improvement. Existing systems and processes did not provide adequate security for high-cost inventory within the hospital, which was another driver of cost. A lack of visibility into expiration dates for supplies resulted in supplies being wasted due to past expiry dates. Storage of supplies was also a key consideration given the location of the cancer center’s facilities in a dense urban setting, where space is always at a premium. In order to address the challenges outlined above, the hospital sought a solution that would provide real-time inventory information with high levels of accuracy, reduce the level of manual effort required and enable data driven decision making to ensure that the right supplies were readily available to clinicians in the right location at the right time.
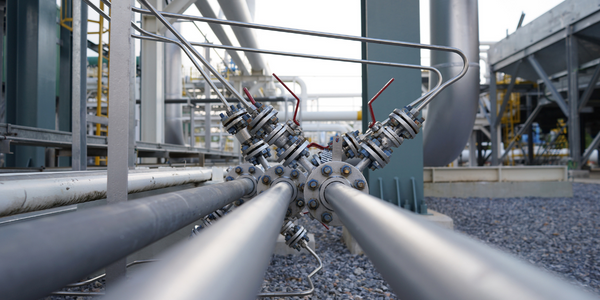
Case Study
Gas Pipeline Monitoring System for Hospitals
This system integrator focuses on providing centralized gas pipeline monitoring systems for hospitals. The service they provide makes it possible for hospitals to reduce both maintenance and labor costs. Since hospitals may not have an existing network suitable for this type of system, GPRS communication provides an easy and ready-to-use solution for remote, distributed monitoring systems System Requirements - GPRS communication - Seamless connection with SCADA software - Simple, front-end control capability - Expandable I/O channels - Combine AI, DI, and DO channels
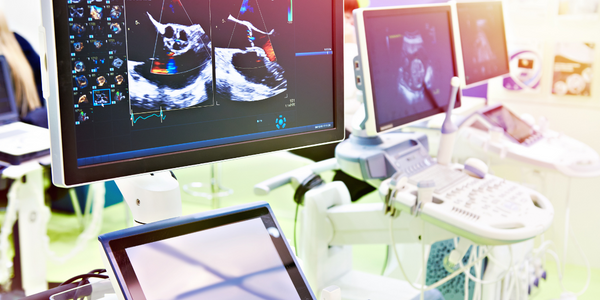
Case Study
Driving Digital Transformations for Vitro Diagnostic Medical Devices
Diagnostic devices play a vital role in helping to improve healthcare delivery. In fact, an estimated 60 percent of the world’s medical decisions are made with support from in vitrodiagnostics (IVD) solutions, such as those provided by Roche Diagnostics, an industry leader. As the demand for medical diagnostic services grows rapidly in hospitals and clinics across China, so does the market for IVD solutions. In addition, the typically high cost of these diagnostic devices means that comprehensive post-sales services are needed. Wanteed to improve three portions of thr IVD:1. Remotely monitor and manage IVD devices as fixed assets.2. Optimizing device availability with predictive maintenance.3. Recommending the best IVD solution for a customer’s needs.
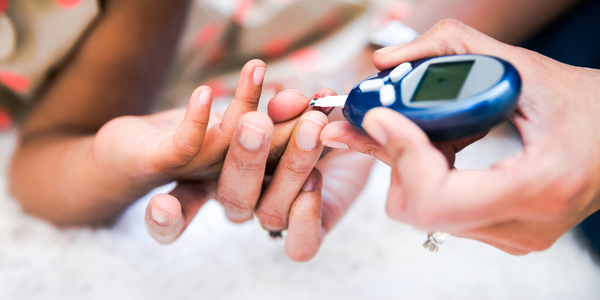
Case Study
HaemoCloud Global Blood Management System
1) Deliver a connected digital product system to protect and increase the differentiated value of Haemonetics blood and plasma solutions. 2) Improve patient outcomes by increasing the efficiency of blood supply flows. 3) Navigate and satisfy a complex web of global regulatory compliance requirements. 4) Reduce costly and labor-intensive maintenance procedures.
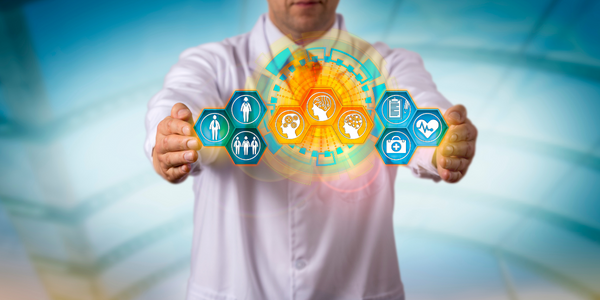
Case Study
Harnessing real-time data to give a holistic picture of patient health
Every day, vast quantities of data are collected about patients as they pass through health service organizations—from operational data such as treatment history and medications to physiological data captured by medical devices. The insights hidden within this treasure trove of data can be used to support more personalized treatments, more accurate diagnosis and more advanced preparative care. But since the information is generated faster than most organizations can consume it, unlocking the power of this big data can be a struggle. This type of predictive approach not only improves patient care—it also helps to reduce costs, because in the healthcare industry, prevention is almost always more cost-effective than treatment. However, collecting, analyzing and presenting these data-streams in a way that clinicians can easily understand can pose a significant technical challenge.