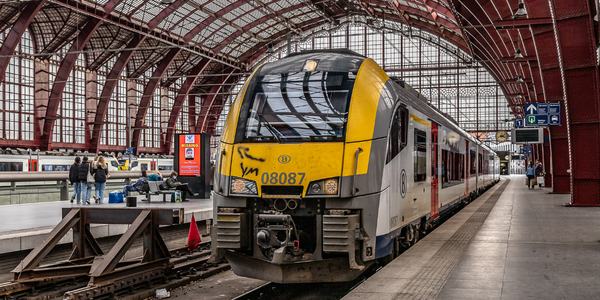
- Analytics & Modeling - Big Data Analytics
- Infrastructure as a Service (IaaS)
- Transportation
- Product Research & Development
- Root Cause Analysis & Diagnosis
Train operators the world over are expected to work miracles, i.e. never to be late. So, with acute service and availability targets to meet, an efficient maintenance program is important. And data-enabled functionality is a must for Siemens. Reactive maintenance (after an incident) and routine, preventive maintenance with its visual inspections and scheduled exchange of components, are no longer enough. We’ve moved on to more cost-effective, condition-based, predictive maintenance. The actual condition of components is measured via the transfer and remote monitoring of diagnostic sensor data; data which is also used to analyse patterns and trends. This helps predict when a component is likely to fail, so it can be repaired before anything untoward happens. To ensure the commercial sustainability of this approach, Siemens needs to use and re-use existing data, creating a kind of ‘Internet of Trains’. Towards this end, they’re analysing sensor data in near real time, which means they can react very quickly, ensuring that customer transport services aren’t interrupted. “It is really difficult to define every issue before it impacts operations using only data from the trains”, Kress explains. However, recent success stories prove that everything is possible.
And in the UK, Siemens conducted a pilot project with a large European train operator on one of its regional routes. The project analysed a relatively small data set of one million sensor-log readings, taken in five-minute intervals over the course of a year. Analysts measured variables such as component temperature and pressure from 300 different sensors. This data was overlaid with many thousands of corresponding reports of failures and fixes. Then the team combined data sources, defined the most relevant engine problems, and divided the data into appropriate sections. They used the Teradata Aster Discovery Platform’s exceptional range of analytic tools to evaluate the combined data from different perspectives. It highlighted variables that helped to predict engine problems and identify failed elements that triggered the malfunction of other components. Siemens then applied the Aster nPath function to categorise the different sensors attributing normal, high, and low values, then tracking changes. These changes revealed which sensor pattern was likely to result in engine failure. For example, on a number of occasions Siemens found that when the engine temperature dropped from mid to low then rose to mid value again, an engine failed three days later. During the validation process, comparing results from the test data to the total data set showed a high degree of accuracy, proving that sensor-data analysis makes it possible not only to predict engine failures, but to react in time to prevent them.
Case Study missing?
Start adding your own!
Register with your work email and create a new case study profile for your business.