Download PDF
TrueCar Employs Imply Cloud for Enhanced Self-Service Analytics
Technology Category
- Analytics & Modeling - Real Time Analytics
- Sensors - Autonomous Driving Sensors
Applicable Industries
- Automotive
- Consumer Goods
Applicable Functions
- Procurement
- Quality Assurance
Use Cases
- Smart Parking
- Vehicle-to-Infrastructure
Services
- Cloud Planning, Design & Implementation Services
- Testing & Certification
The Challenge
TrueCar, a leading automotive digital marketplace, was facing challenges in analyzing real-time clickstream data to detect anomalies in user activity. The latency from its existing data warehouse and business intelligence stack was higher than desired, and the cost of scaling to support analytics on large and growing amounts of streaming data was a concern. TrueCar wanted to make analytics available not just to analysts, but also to business users in diverse functions such as marketing and finance. They sought to achieve this without the time and risk associated with building an end-to-end analytics capability from scratch.
About The Customer
TrueCar is a leading automotive digital marketplace that connects car buyers to a nationwide network of Certified Dealers. The company is committed to building the industry's most personalized and efficient car buying experience by bringing more of the purchasing process online. TrueCar provides a suite of vehicle discovery tools, price ratings, and market context on new and used cars, all with a clear view of what's a great deal. TrueCar also powers car-buying programs for over 250 leading brands, including AARP, Sam’s Club, and American Express. Nearly half of all new-car buyers engage with TrueCar powered sites.
The Solution
TrueCar selected Imply Cloud as their self-service analytics platform to address these challenges. The aim was to make their dashboards real-time, detect anomalies, and do so while minimizing engineering and operational overhead. With Imply, TrueCar planned to unlock insights from digital interaction data from their core services, further empower their data scientists and product teams to improve services with increased agility, deliver a higher quality experience, and ensure they are investing in the right areas of the TrueCar platform. TrueCar’s data architecture uses Amazon Kinesis and Spark Streaming for data ingestion and preparation, Imply Cloud for analytics and HDFS for deep storage. The Imply analytics engine connects to the Imply Pivot analytics UI to power real-time self-service data applications. It also connects to Tableau to provide executive dashboards.
Operational Impact
Related Case Studies.
.png)
Case Study
Improving Vending Machine Profitability with the Internet of Things (IoT)
The vending industry is undergoing a sea change, taking advantage of new technologies to go beyond just delivering snacks to creating a new retail location. Intelligent vending machines can be found in many public locations as well as company facilities, selling different types of goods and services, including even computer accessories, gold bars, tickets, and office supplies. With increasing sophistication, they may also provide time- and location-based data pertaining to sales, inventory, and customer preferences. But at the end of the day, vending machine operators know greater profitability is driven by higher sales and lower operating costs.
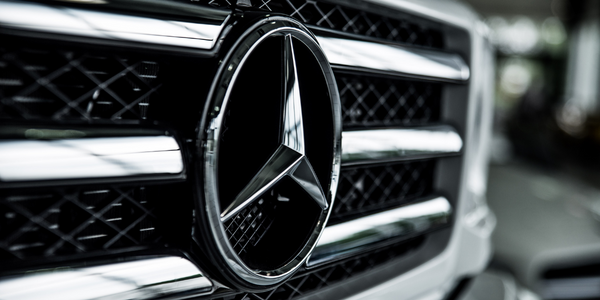
Case Study
Integral Plant Maintenance
Mercedes-Benz and his partner GAZ chose Siemens to be its maintenance partner at a new engine plant in Yaroslavl, Russia. The new plant offers a capacity to manufacture diesel engines for the Russian market, for locally produced Sprinter Classic. In addition to engines for the local market, the Yaroslavl plant will also produce spare parts. Mercedes-Benz Russia and his partner needed a service partner in order to ensure the operation of these lines in a maintenance partnership arrangement. The challenges included coordinating the entire maintenance management operation, in particular inspections, corrective and predictive maintenance activities, and the optimizing spare parts management. Siemens developed a customized maintenance solution that includes all electronic and mechanical maintenance activities (Integral Plant Maintenance).