Download PDF
Utilizing Computational Flow Modeling for Enhanced Combined Sewer Overflow System Design
Technology Category
- Sensors - Liquid Detection Sensors
- Sensors - Utility Meters
Applicable Industries
- Renewable Energy
- Utilities
Applicable Functions
- Procurement
- Product Research & Development
Use Cases
- Intelligent Urban Water Supply Management
- Leakage & Flood Monitoring
Services
- System Integration
The Challenge
Cities in the northeastern U.S. were exploring the installation of new combined sewer overflow (CSO) treatment units using an advanced hydrodynamic vortex separator (HDVS) with a self-cleansing screen, such as that produced by Hydro International. Traditionally, HDVSs have been used as high-rate solid–liquid separators; only recently has their potential use as contact chambers for high-rate disinfection of CSOs been realized. Conventional disinfection of CSOs, using mixed basins, requires contact times of around 15 minutes. However, a report demonstrated that these systems provide effective high-rate disinfection at contact times of only three minutes. While the shorter contact times could save up to 50 percent of overall project costs for municipalities, regulators still expected to see longer contact times based on performance requirements of older systems. The challenge for Hydro International was to understand the basis for the shorter contact times and validate that high-rate disinfection is an acceptable alternative to longer conventional disinfection methods.
About The Customer
Hydro International is a global supplier of innovative, environmentally sustainable products and services that meet the evolving regulations for the control and treatment of stormwater, combined sewer overflows, and wastewater. The company’s line of products provides an economical solution to control quantity and improve water quality. They are committed to offering their customers a less expensive, high-performance solution to address combined sewer overflow requirements.
The Solution
Hydro International, in collaboration with Cardiff University, used ANSYS Fluent flow modeling software to develop a computational model for the Storm King HDVS. They ran the model through a range of flow speeds corresponding to full-scale laboratory experiments and used the results to compute contact times and compare these values with the experimental results. By combining physical experiments with the computational program, Hydro International successfully demonstrated that modeled residence times and disinfection kill rates in the Storm King system agree with full-scale laboratory observations. They provided insights into the basis for the observed disinfection efficacy and confirmed that disinfection kill rates are equivalent to (or in some cases better than) those of a conventional tank. These results were used to support a proposal for regulatory agencies to relax the 15-minute contact time mandate for CSO disinfection.
Operational Impact
Quantitative Benefit
Related Case Studies.
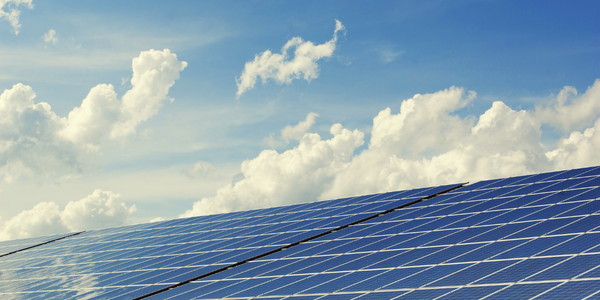
Case Study
Remote Monitoring & Predictive Maintenance App for a Solar Energy System
The maintenance & tracking of various modules was an overhead for the customer due to the huge labor costs involved. Being an advanced solar solutions provider, they wanted to ensure early detection of issues and provide the best-in-class customer experience. Hence they wanted to automate the whole process.

Case Study
IoT Solutions for Smart City | Internet of Things Case Study
There were several challenges faced: It is challenging to build an appliance that can withstand a wide range of voltage fluctuations from as low at 90v to as high as 320v. Since the device would be installed in remote locations, its resilience was of paramount importance. The device would have to deal with poor network coverage and have the ability to store and re-transmit data if networks were not available, which is often the case in rural India. The device could store up to 30 days of data.
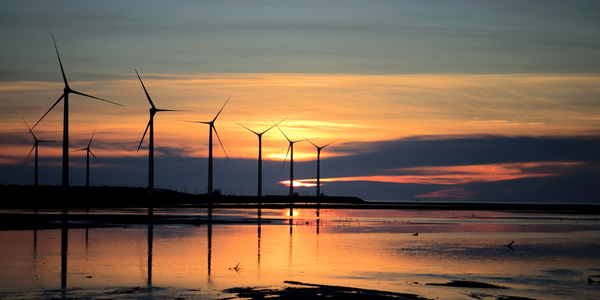
Case Study
Vestas: Turning Climate into Capital with Big Data
Making wind a reliable source of energy depends greatly on the placement of the wind turbines used to produce electricity. Turbulence is a significant factor as it strains turbine components, making them more likely to fail. Vestas wanted to pinpoint the optimal location for wind turbines to maximize power generation and reduce energy costs.
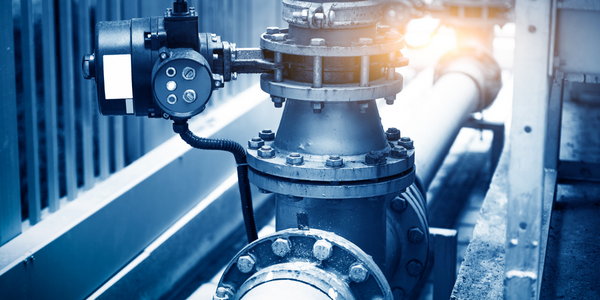
Case Study
Automation of the Oguz-Gabala-Baku water pipeline, Azerbaijan
The Oguz-Gabala-Baku water pipeline project dates back to plans from the 1970’s. Baku’s growth was historically driven by the booming oil industry and required the import of drinking water from outside of the city. Before the construction of the pipeline, some 60 percent of the city’s households received water for only a few hours daily. After completion of the project, 75 percent of the two million Baku residents are now served around the clock with potable water, based on World Health Organization (WHO) standards. The 262-kilometer pipeline requires no pumping station, but uses the altitude differences between the Caucasian mountains and the capital to supply 432,000 m³/d to the Ceyranbatan water reservoir. To the people of Baku, the pipeline is “the most important project not only in 2010, but of the last 20 years.”
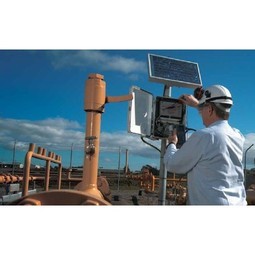
Case Study
GPRS Mobile Network for Smart Metering
Around the world, the electricity supply industry is turning to ‘smart’ meters to lower costs, reduce emissions and improve the management of customer supplies. Smart meters collect detailed consumption information and using this feedback consumers can better understand their energy usage which in turn enables them to modify their consumption to save money and help to cut carbon emissions. A smart meter can be defined in many ways, but generally includes an element of two-way communication between the household meter and the utility provider to efficiently collect detailed energy usage data. Some implementations include consumer feedback beyond the energy bill to include online web data, SMS text messages or an information display in consumers’ premises. Providing a cost-effective, reliable communications mechanism is one of the most challenging aspects of a smart meter implementation. In New Zealand, the utilities have embraced smart metering and designed cost effective ways for it to be implemented. The New Zealand government has encouraged such a move to smart metering by ensuring the energy legislation is consistent with the delivery of benefits to the consumer while allowing innovation in this area. On the ground, AMS is a leader in the deployment of smart metering and associated services. Several of New Zealand’s energy retailers were looking for smart metering services for their residential and small business customers which will eventually account for over 500,000 meters when the multi-year national deployment program is concluded. To respond to these requirements, AMS needed to put together a solution that included data communications between each meter and the central data collection point and the solution proposed by Vodafone satisfied that requirement.
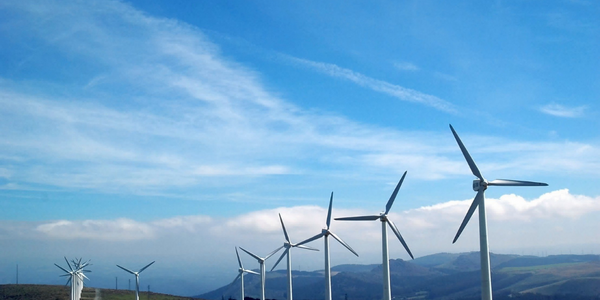
Case Study
Siemens Wind Power
Wind provides clean, renewable energy. The core concept is simple: wind turbines spin blades to generate power. However, today's systems are anything but simple. Modern wind turbines have blades that sweep a 120 meter circle, cost more than 1 million dollars and generate multiple megawatts of power. Each turbine may include up to 1,000 sensors and actuators – integrating strain gages, bearing monitors and power conditioning technology. The turbine can control blade speed and power generation by altering the blade pitch and power extraction. Controlling the turbine is a sophisticated job requiring many cooperating processors closing high-speed loops and implementing intelligent monitoring and optimization algorithms. But the real challenge is integrating these turbines so that they work together. A wind farm may include hundreds of turbines. They are often installed in difficult-to-access locations at sea. The farm must implement a fundamentally and truly distributed control system. Like all power systems, the goal of the farm is to match generation to load. A farm with hundreds of turbines must optimize that load by balancing the loading and generation across a wide geography. Wind, of course, is dynamic. Almost every picture of a wind farm shows a calm sea and a setting sun. But things get challenging when a storm goes through the wind farm. In a storm, the control system must decide how to take energy out of gusts to generate constant power. It must intelligently balance load across many turbines. And a critical consideration is the loading and potential damage to a half-billion-dollar installed asset. This is no environment for a slow or undependable control system. Reliability and performance are crucial.