Download PDF
Verso Corporation Reshapes Outbound Logistics with MercuryGate TMS, Optimization
Technology Category
- Functional Applications - Transportation Management Systems (TMS)
Applicable Industries
- Paper & Pulp
- Packaging
Applicable Functions
- Logistics & Transportation
- Warehouse & Inventory Management
Use Cases
- Fleet Management
- Supply Chain Visibility
- Predictive Maintenance
Services
- System Integration
- Software Design & Engineering Services
The Challenge
Deciding to move to a new Transportation Management System (TMS) isn’t something that logistics managers do without a good reason and careful consideration. Sometimes, however, a company’s hand is forced into making a change. That was the scenario that faced the outbound logistics team at Verso Corporation, a producer of graphic and specialty papers, packaging, and pulp. After a few years on a hosted TMS, Verso was notified by its TMS provider that a system upgrade was required to continue to receive support. The Verso team took that notification as their cue to start their search for a new TMS solution that better fit its needs.\n\n“The biggest thing for us, as a paper company, was to have a system that would be reliable and stable,” said Michael Dailey, Corporate Logistics Manager at Verso. “We needed to make sure that we didn’t have any customer interruptions.”\n\nToday, Verso has more than 5,000 unique customers globally. In the paper industry, these customers often have very late cutoff times and next-day delivery requirements. Delivery appointment times can be difficult to pin down. Cut off times might be at 5 pm while the client’s receiving department leaves at 4 pm. With such tight timeframes, the shipping process must be extremely efficient.
About The Customer
Verso Corporation is a leading producer of graphic and specialty papers, packaging, and pulp. Headquartered in Miamisburg, Ohio, Verso operates seven mills in the United States, located in places like the upper peninsula of Michigan, rural Maine, and isolated areas of West Virginia and Maryland. The company serves more than 5,000 unique customers globally, including merchant partners and direct customers. Verso's operations are characterized by the need for reliable and stable transportation management due to the remote locations of their mills and the tight delivery windows required by their customers. The company manages two distinct supply chains: one for stock material that goes into distribution centers and another for direct shipments from mills to merchant partners or printers.
The Solution
After considering other hosted solutions and evaluating several SaaS-based systems, Verso chose the MercuryGate TMS. In addition to providing stability, they also found the MercuryGate system much easier to use. With a well-defined implementation plan, Verso was able to get up and running quickly on the MercuryGate TMS and the Mojo optimization tool.\n\nDuring the evaluation process, the Verso team looked at both hosted and SaaS-based options to replace their existing system. While the need to change may have been thrust upon them, they wanted to make the most of the opportunity to select a system that could help reshape their operations. As the team reviewed the list of critical requirements, it became clear that MercuryGate checked many of the boxes and closed the functionality gaps left by their existing software.\n\n“We just really felt more comfortable with the MercuryGate software than we did with everything else,” said Dailey.
Operational Impact
Quantitative Benefit
Related Case Studies.
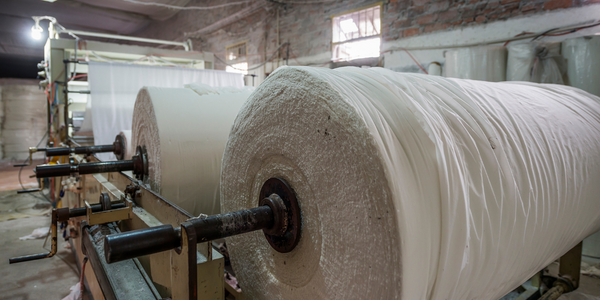
Case Study
Wireless Improves Efficiency in Compressed Air Systems
Hollingsworth and Vose wanted to improve the efficiency of their compressed air system, lower the electricity expense component of manufacturing cost in their commodity industry, and conserve energy leading to lowered greenhouse gas emissions. Compressed air systems degrade over time and become leaky and inefficient. Hollingsworth and Vose wanted to increase the frequency of system inspections without paying the high cost of manual labor.
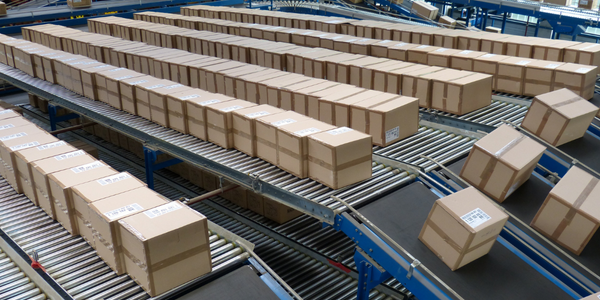
Case Study
IoT Data Analytics Case Study - Packaging Films Manufacturer
The company manufactures packaging films on made to order or configure to order basis. Every order has a different set of requirements from the product characteristics perspective and hence requires machine’s settings to be adjusted accordingly. If the film quality does not meet the required standards, the degraded quality impacts customer delivery causes customer dissatisfaction and results in lower margins. The biggest challenge was to identify the real root cause and devise a remedy for that.
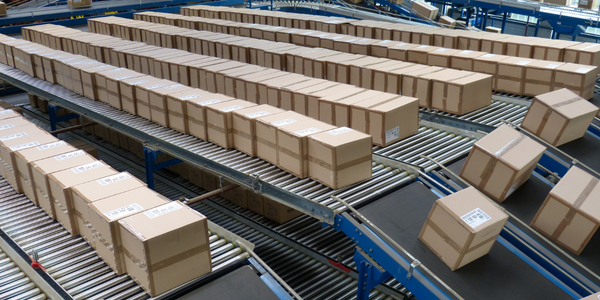
Case Study
Zenon the Ideal Basis for An Ergonomic HMI
KHS develops and produces machines and equipment for filling and packaging in the drinks industry. Because drinks manufacturing, filling and packaging consist of a number of highly complex processes, the user-friendly and intuitive operation of equipment is increasingly gaining in significance. In order to design these processes as simple as possible for the user, KHS decided to introduce a uniform, transparent and standardized solution to the company. The HMI interface should meet the requirement for people with different qualifications and enable them to work on a standard platform.
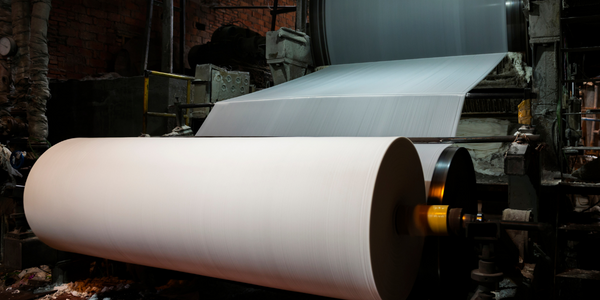
Case Study
Process Predictive Analysis in Pulp and Paper Mill
Common paper breaks consequently lead up to 60 minutes of downtime, delaying a potential $10K per hour of production value process. Thus, defective products cause financial and damage company's reputation. Improving quality and reducing defect rates can generate millions of dollars of revenue per year for your company.
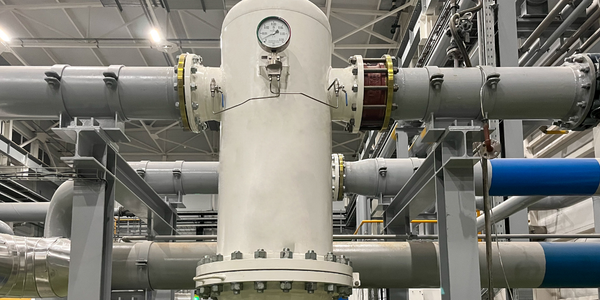
Case Study
Sparks Dynamics Assists Atlas Container Secure a $15,000 BGE Energy Rebate
The ReMASTER Compressed Air Monitoring system was installed in 2015. This system is capable of monitoring compressed air system parameters on a continuous basis and transferring that information to a cloud server which can be accessed by Atlas Container personnel, Industrial Diagnostics and Sparks Dynamics. This information was collected into a database which can be exported to an Excel spreadsheet or displayed graphically using Sparks Dynamics ViewMaster Software. The average annual compressed air electricity expense was estimated to be approximately $116,000. This is based on an incremental $/KWh electric rate of $.091 per KWh and an estimated compressed air energy consumption of 1,279,200 KWH. The implementation phase of Energy Conservation Measures (ECMs) for the Compressed Air System included: • Identification and repair of compressed air leaks • Understanding of compressed air usage per manufacturing machine and installation of shut off valves when the machines are no longer in production mode • Identification of misapplications of compressed air to include blow offs, venturis, and cooling scenarios • Understand system pressure requirements and potential installation of point of use pressure regulation.