Download PDF
Vierhout Engineering's Structural Steel Machine Frame Improvement with Mesh-free Simulation
Technology Category
- Analytics & Modeling - Digital Twin / Simulation
- Application Infrastructure & Middleware - Middleware, SDKs & Libraries
Applicable Industries
- Equipment & Machinery
- Metals
Applicable Functions
- Product Research & Development
Use Cases
- Manufacturing Process Simulation
- Virtual Prototyping & Product Testing
The Challenge
Vierhout Engineering (VE), a professional independent engineering services provider, was approached by Universal Corrugated B.V. (UC) to analyze and simulate one of its machines. The machine was incredibly complex, and VE realized that traditional Finite Element Analysis (FEA) might not be sufficient for this project. The traditional FEA process required significant effort and expertise to prepare the models for analysis, especially for geometry simplification and meshing. The machine's complexity meant that each component or system had to be simplified and divided for analysis, a time-consuming process that often reached the hardware limits of the computers used. Large structural frames also had to be analyzed with simplified beams and sheet elements, a cumbersome, error-prone, and time-consuming process.
About The Customer
Universal Corrugated B.V. (UC), part of the Minda Group and based in Almelo, the Netherlands, is a company offering automatic deposit systems for the corrugated cardboard and board industry. UC provides solutions for the dry end of corrugated cardboard plants, including complete systems for the manufacturing of endless corrugated cardboard and stacking systems down-stream of corrugated cardboard converting machines. They approached Vierhout Engineering (VE), a professional independent engineering services provider based in Hengelo, the Netherlands, for support in analyzing and simulating one of their machines.
The Solution
VE turned to Altair SimSolid, a structural analysis software developed specifically for upfront structural assessment. SimSolid eliminates the need for geometry simplification and meshing, the two most time-consuming and expertise-intensive tasks in traditional FEA. VE used SimSolid to analyze the structural steel machine frame in high detail. The frame, which had a mass of about 20 tons and was approximately 32 meters long, was analyzed with different load cases and detailed framework conditions of contacts and forces. SimSolid allowed VE to analyze the complete 3D detailed model, including bolts and nuts with tightening torques and pre-tensions. Parts with contacts such as flange connections were analyzed geometrically, non-linearly, including friction and separation contacts. The results of these analyses were very detailed and clearly displayed in 3D with material stress, displacements, modal frequencies, and reaction forces on the foundations.
Operational Impact
Quantitative Benefit
Related Case Studies.
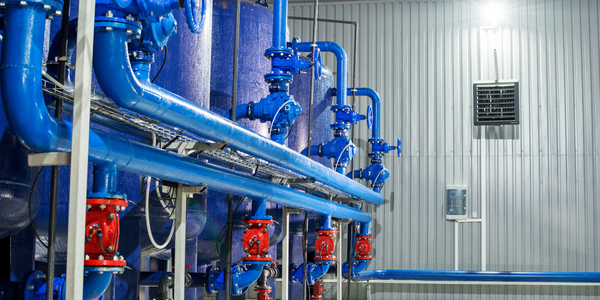
Case Study
Smart Water Filtration Systems
Before working with Ayla Networks, Ozner was already using cloud connectivity to identify and solve water-filtration system malfunctions as well as to monitor filter cartridges for replacements.But, in June 2015, Ozner executives talked with Ayla about how the company might further improve its water systems with IoT technology. They liked what they heard from Ayla, but the executives needed to be sure that Ayla’s Agile IoT Platform provided the security and reliability Ozner required.
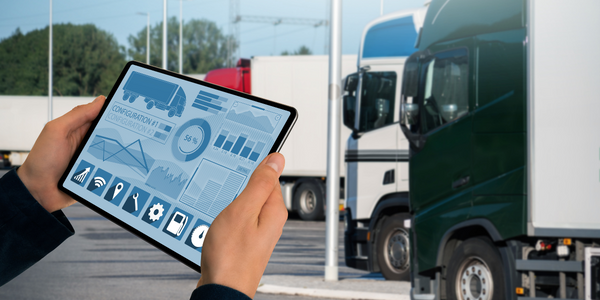
Case Study
IoT enabled Fleet Management with MindSphere
In view of growing competition, Gämmerler had a strong need to remain competitive via process optimization, reliability and gentle handling of printed products, even at highest press speeds. In addition, a digitalization initiative also included developing a key differentiation via data-driven services offers.
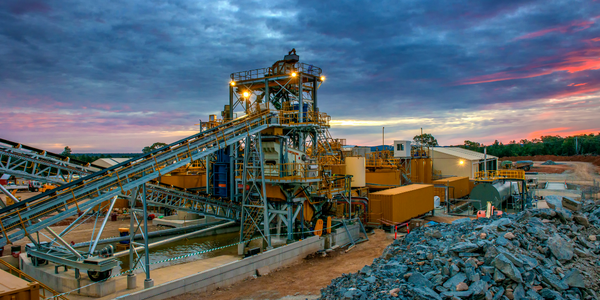
Case Study
Goldcorp: Internet of Things Enables the Mine of the Future
Goldcorp is committed to responsible mining practices and maintaining maximum safety for its workers. At the same time, the firm is constantly exploring ways to improve the efficiency of its operations, extend the life of its assets, and control costs. Goldcorp needed technology that can maximize production efficiency by tracking all mining operations, keep employees safe with remote operations and monitoring of hazardous work areas and control production costs through better asset and site management.
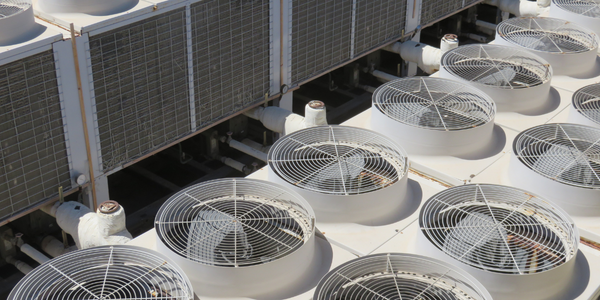
Case Study
Predictive Maintenance for Industrial Chillers
For global leaders in the industrial chiller manufacturing, reliability of the entire production process is of the utmost importance. Chillers are refrigeration systems that produce ice water to provide cooling for a process or industrial application. One of those leaders sought a way to respond to asset performance issues, even before they occur. The intelligence to guarantee maximum reliability of cooling devices is embedded (pre-alarming). A pre-alarming phase means that the cooling device still works, but symptoms may appear, telling manufacturers that a failure is likely to occur in the near future. Chillers who are not internet connected at that moment, provide little insight in this pre-alarming phase.
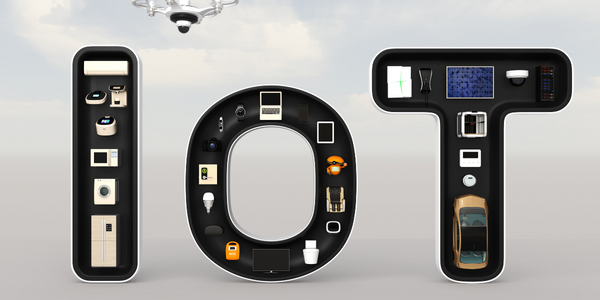
Case Study
Premium Appliance Producer Innovates with Internet of Everything
Sub-Zero faced the largest product launch in the company’s history:It wanted to launch 60 new products as scheduled while simultaneously opening a new “greenfield” production facility, yet still adhering to stringent quality requirements and manage issues from new supply-chain partners. A the same time, it wanted to increase staff productivity time and collaboration while reducing travel and costs.
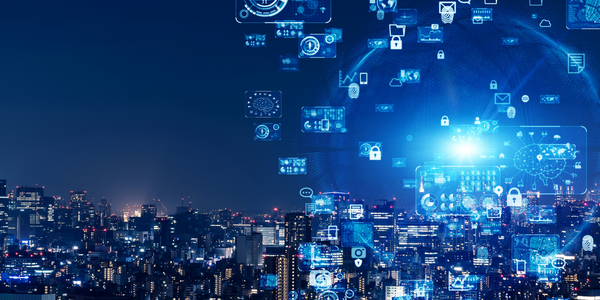
Case Study
Integration of PLC with IoT for Bosch Rexroth
The application arises from the need to monitor and anticipate the problems of one or more machines managed by a PLC. These problems, often resulting from the accumulation over time of small discrepancies, require, when they occur, ex post technical operations maintenance.