Download PDF
VKB Group: Driving consistent standardization and increasing testing efficiency
Technology Category
- Application Infrastructure & Middleware - Data Exchange & Integration
- Application Infrastructure & Middleware - Database Management & Storage
Applicable Functions
- Quality Assurance
- Product Research & Development
Use Cases
- Regulatory Compliance Monitoring
- Predictive Quality Analytics
Services
- System Integration
- Software Design & Engineering Services
The Challenge
VKB Group, Germany’s largest public insurer, was facing challenges in optimizing its software testing. The company's software development teams were experiencing slow test runs when evaluating new features for their mission-critical core insurance applications. The large volumes of data used for testing often resulted in incomplete test runs that had to be restarted, causing delays in productivity and potentially delaying the release of new functionalities. VKB Group aimed to streamline its internal workflows and enable software development teams to test new features and fixes with a smaller set of standardized data, helping to speed up cycle times and improve the agility of development processes.
About The Customer
Versicherungskammer Bayern is part of the VKB Group, Germany’s largest public insurer. The company is among the nation’s top ten primary insurers, and collected EUR7.6 billion (USD8.9 billion) in premiums in 2015 (provisional data). Its regional subsidiaries operate in Bavaria, Palatinate, Saarland, Berlin and Brandenburg. In conjunction with other public insurers, the firm offers health insurance nationwide. VKB Group has earned recognition as a family-friendly company, and employs around 6,800 people including more than 350 apprentices.
The Solution
VKB Group deployed IBM InfoSphere Optim Test Data Management and IBM InfoSphere Optim Data Privacy to streamline its software testing workflows. The solutions were connected to its main IBM DB2 for z/OS database running on an IBM z Systems server, to IBM DB2 for Linux, UNIX and Windows, and also to some other database instances. The new solution has streamlined testing at VKB Group, enabling testers to work with smaller, standardized data sets that can accelerate testing. The implementation of the test data management solution has enabled VKB Group to introduce more self-service capabilities for testers and drive more automated test data management, saving time and improving testing quality.
Operational Impact
Quantitative Benefit
Related Case Studies.
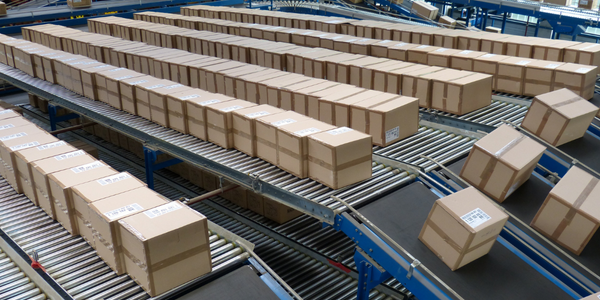
Case Study
IoT Data Analytics Case Study - Packaging Films Manufacturer
The company manufactures packaging films on made to order or configure to order basis. Every order has a different set of requirements from the product characteristics perspective and hence requires machine’s settings to be adjusted accordingly. If the film quality does not meet the required standards, the degraded quality impacts customer delivery causes customer dissatisfaction and results in lower margins. The biggest challenge was to identify the real root cause and devise a remedy for that.

Case Study
Remote Monitoring for Environmental Compliance
Emerson wanted to provide a connected environmental analyzer to their customers. They wanted to leverage IoT technologies to provide a software solution that was easy to use, real-time and centralized. Compliance with pollution control board guidelines and the ability to remotely calibrate and troubleshoot these devices was the primary objective. Requirements - Centralized Remote Monitoring. - IoT Based Smart Environmental Analyzers. - Remote Calibration and Troubleshooting. - User Friendly Application. - Reporting & Dashboards. - Compliance with pollution control board guidelines.
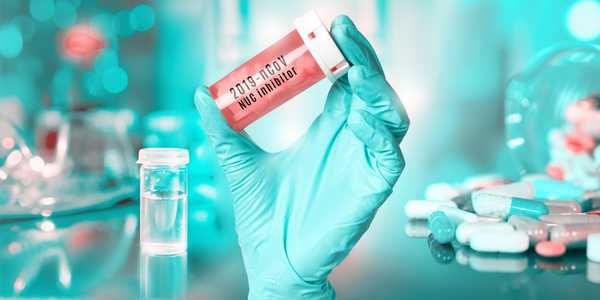
Case Study
ELI LILLY ADOPTS MICROMEDIA’S ALERT NOTIFICATION SYSTEM
Pharmaceutical production is subject to a strict set of enforced rules that must be adhered to and compliance to these standards is critically necessary. Due to the efforts of WIN 911’s strategic partner Micromedia, Lilly was able to adopt an alarm notification infrastructure that integrated smoothly with their existing workflows and emergency hardware and protocols. These raw energy sources enable the industrial process to function: electricity, WIN-911 Software | 4020 South Industrial Drive, Suite 120 | Austin, TX 78744 USA industrial steam, iced water, air mixtures of varying quality. Refrigeration towers, boilers and wastewater are monitored by ALERT. Eli Lilly identified 15000 potential variables, but limitations compelled them to chisel the variable list down to 300. This allowed all major alarms to be covered including pressure, discharge, quantity of waste water discharged,temperature, carbon dioxide content, oxygen & sulphur content, and the water’s pH.
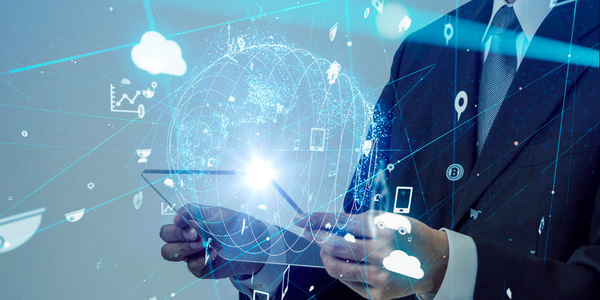
Case Study
IoT Solutions Give Commercial Fishing Real-time insights
Technology to support vessels in the commercial fishing industry had not changed significantly since the advent of radar. Over the past 40 years commercial fishing in the United States has continued to be one of the most active, yet regulated industries. The combination of federal regulations and lack of technology created an opportunity for Faria Watchdog to go-to-market with a solution.
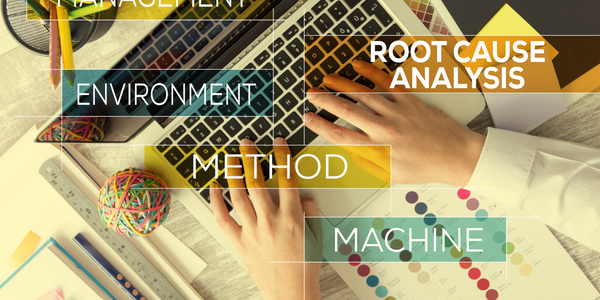
Case Study
Prevent Process Inefficiencies with Automated Root Cause Analysis
Manufacturers mostly rely on on-site expert knowledge for root cause analysis. When the defective product is sent to lab for analysis, it is laborious and always a post-mortem one. Manufacturers that collect data from IT and OT also need a comprehensive understanding of a variety of professionals to make sense of it. This is not only time consuming, but also inefficiencient.
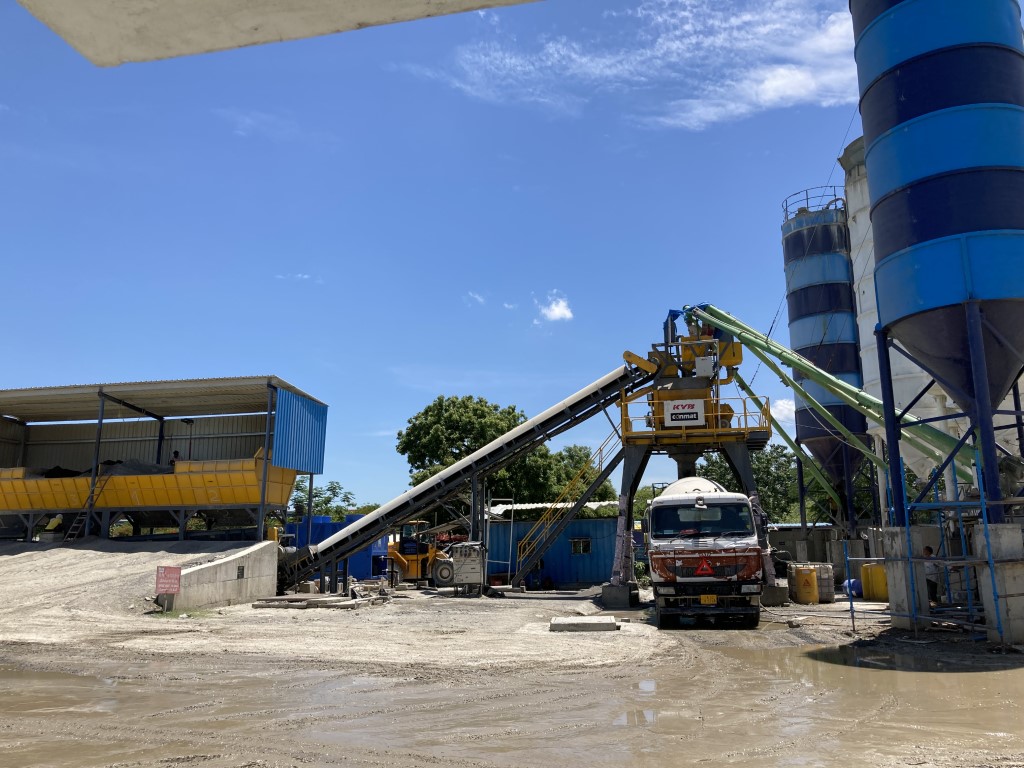
Case Study
Digitalising QC records
Ready-mix concrete batching plant with seasonal demand 6,000 to 12,000 cu.metre per month.Batch-cycle records for each truck is stored in paper format. 1000 to 2000 truck loads per month, generating ~2000 to 6000 paper records.QC anomaly detection in chemical batch-mixing is manual & time consuming.