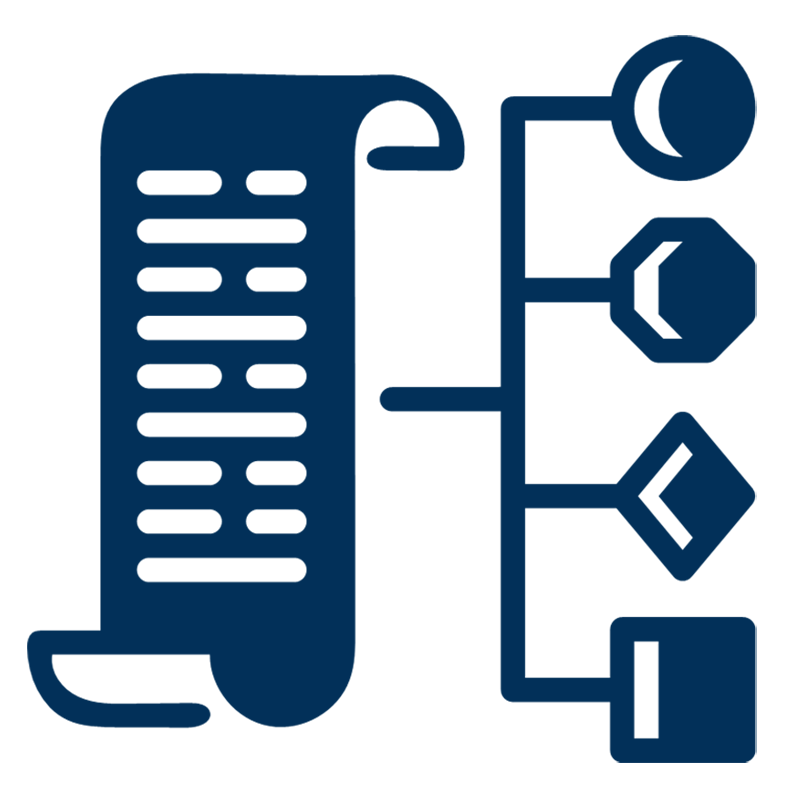
Picking, Sorting & Positioning
Picking, sorting and positioning systems either automate material handling processes or support employees by providing precise guidance through the order processing and fulfillment process. Automated solutions are based on robotics that use scheduled process flows, digital IDs, or machine vision to determing picking, sorting and positioning behavior. Prevision guidance solutions work by increasing the ease of identifying the product-bin combination by removing the need for employees to manually locate and identify the right product-bin combination. They direct warehouse employees using physical displays, virtual or Augmented Reality Wearables, and other devices that can signal which products to put in which bin. Usually, tags such as barcodes, RFID tags, or QR codes are used to identify both the bin and the product. These inventory systems are usually integrated with other supply chain systems such as order management systems, enterprise resource planning systems, and ecommerce systems.
Efficiency and Productivity: Implementing automated picking, sorting, and positioning systems streamlines warehouse operations, reduces labor costs, and enhances overall efficiency. By automating repetitive tasks, businesses can increase throughput, minimize errors, and meet customer demand more effectively.
Inventory Management: Picking, sorting, and positioning systems enable accurate inventory management by tracking the movement of goods within the facility. Real-time data on inventory levels, locations, and status ensure optimal stock levels, reduce stockouts, and improve order fulfillment rates.
Stakeholders involved in picking, sorting, and positioning systems include warehouse managers, logistics operators, production supervisors, and frontline workers. Here's how they perceive these systems:
Warehouse Managers: Warehouse managers prioritize picking, sorting, and positioning systems to optimize warehouse layout, maximize storage space, and improve order fulfillment efficiency. They rely on these systems to coordinate operations, allocate resources, and meet performance targets.
Logistics Operators: Logistics operators view picking, sorting, and positioning systems as essential tools for streamlining distribution processes, reducing lead times, and enhancing customer satisfaction. They expect these systems to enable fast and accurate order processing while minimizing handling and transportation costs.
Robotics and Automation: Robotics technology is used for automated picking, sorting, and positioning of goods within the warehouse or manufacturing facility. Robotic arms, automated guided vehicles (AGVs), and autonomous mobile robots (AMRs) perform tasks such as picking, sorting, palletizing, and transporting goods with precision and efficiency.
Barcode and RFID Technology: Barcode and RFID technology are used for item identification, tracking, and inventory management. Barcodes and RFID tags are attached to goods, pallets, and containers to enable accurate identification and tracking throughout the supply chain.
Data plays a crucial role in picking, sorting, and positioning systems by providing insights into inventory levels, order volumes, and process efficiency. Here's how data is utilized:
Inventory Tracking: Picking, sorting, and positioning systems collect real-time data on inventory levels, locations, and movements within the facility. This data is used to track stock levels, optimize storage allocation, and replenish inventory as needed to prevent stockouts.
Performance Monitoring: Data from picking, sorting, and positioning systems is analyzed to monitor process performance, identify bottlenecks, and improve operational efficiency. Key performance indicators such as order cycle times, picking accuracy, and throughput rates are tracked to measure system effectiveness.
Hardware Installation: Picking, sorting, and positioning systems may require the installation of conveyors, automated guided vehicles (AGVs), robotic arms, and other equipment within the facility. Hardware components are integrated into existing infrastructure to facilitate seamless operation.
Software Integration: Picking, sorting, and positioning systems are integrated with warehouse management systems (WMS), enterprise resource planning (ERP) software, and other business applications to enable data exchange and process synchronization. Software solutions provide control, visibility, and automation capabilities to optimize system performance.