下载PDF
Advanced Elastomer Systems Upgrades Production
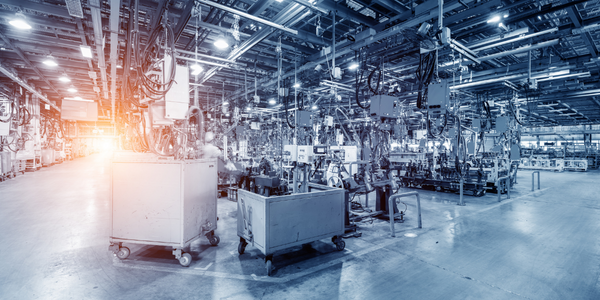
技术
- 分析与建模 - 预测分析
- 平台即服务 (PaaS) - 设备管理平台
适用行业
- 化学品
适用功能
- 流程制造
用例
- 机器状态监测
挑战
为了保持其在热塑性弹性体国际市场的份额,AES 最近扩大了其佛罗里达工厂,增加了一条新的生产线。虽然现有生产线使用带有传统模拟 I/O 的 PROVOX 分布式控制系统运行良好,但 AES 希望在新生产线上采用先进技术,以提高经济性、效率和可靠性。 AES 官员急于让这条生产线投入生产以满足收到的订单,但两次飓风减缓了建设速度。
客户
先进的弹性体系统
关于客户
Advanced Elastomer Systems (AES) 是埃克森美孚化工的附属公司,也是热塑性弹性体的主要生产商。
解决方案
通过选择先进的控制技术来利用总线架构的安装效率来弥补一些损失的时间。现场总线网络简化了安装并将总布线成本降低了约 15%。仪器到货时已配置好并可以联网。在调试和启动阶段,AES 通过使用艾默生的智能设备管理器预测性维护软件与现场仪器进行通信,从而节省了大量时间。在调试期间,一名技术人员可以直接从控制室查询每台仪器,与现场观察员确认该设备的功能,然后在不打开仪器盖的情况下继续使用另一台设备。如果设备或相关设备的状况变化超出预定限制,则状态警报会向线路操作员指示问题。真实、可操作的信息使设备维护更容易。硬件组件 - PROVOX 分布式控制系统(带有传统模拟 I/O) - FOUNDATION 现场总线网络 - 罗斯蒙特仪表 软件组件 - DeltaV 数字自动化系统 - AMS Suite 智能设备管理器(用于预测性维护)
收集的数据
Device Status, Equipment Status, Installation Diagnostics
运营影响
数量效益
相关案例.
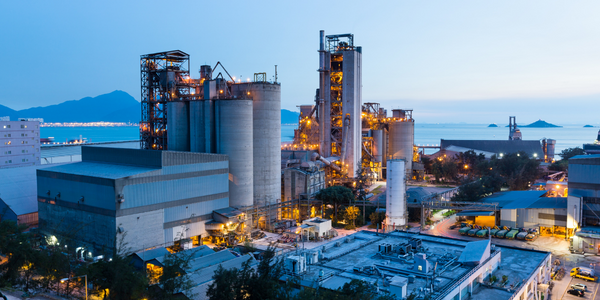
Case Study
Honeywell - Tata Chemicals Improves Data Accessibility with OneWireless
Tata was facing data accessibility challenges in the cement plant control room tapping signals from remote process control areas and other distant locations, including the gas scrubber. Tata needed a wireless solution to extend its control network securely to remote locations that would also provide seamless communication with existing control applications.

Case Study
Wireless GPS Tracking & Security Monitoring
Enhancing the security of hazardous freight and ensuring compliance with Homeland Security’s Transportation Security Administration mandate that all trains carrying chemicals capable of creating a toxic inhalation condition are equipped with on-board safety monitoring systems.
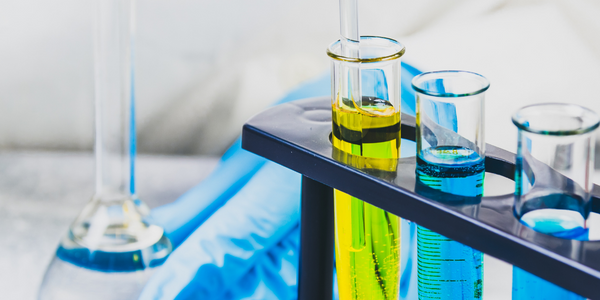
Case Study
Field Device Asset Management For Chemical Company in China
Chinese chemical subsidiary of multinational corporation serves customers throughout the world. Sales offices and research and technology centers are strategically located to provide rapid response to customer requests. Just two workers were assigned to maintain thousands of intelligent instruments in three production units, so they could do little more than react to device issues as they appeared. This costly maintenance method inevitably led to unexpected downtime when a critical instrument failed. Plant management recognized the need to change from reactive to predictive maintenance for all assets, including instruments and control valves, but help was needed in implementing such a technology-based initiative.
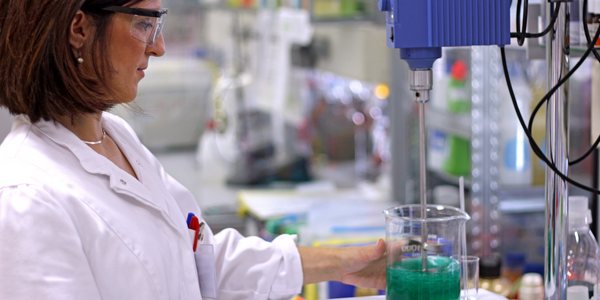
Case Study
Industrial Workforce Mobility for Improved Safety & Operations
Huntsman Corporation, a global manufacturer and marketer of differentiated chemicals, undertook an aggressive program to eliminate injuries, product defects, and environmental releases at their Port Neches facility. Termed “Project Zero”, this program required a completely mobile solution to empower operations and maintenance personnel to capture defects, track work progress and make process and safety related decisions in real-time.

Case Study
Downtime of automated systems cut by 28% at Brillux paint plant
Paint and coatings specialist Brillux is a manufacturer of painting products in central Europe. The company's warehouse and distribution operations include a fully automated conveyor system controlled by Siemens SIMATIC automated process controllers and a traditional MLOG SCADA system to reduce downtime.