下载PDF
Ameren Callaway Plant's Transition to ICONICS GENESIS32 for Enhanced Data Access and Remote Maintenance

技术
- 分析与建模 - 实时分析
- 传感器 - 电表
适用行业
- 化学品
- 生命科学
适用功能
- 人力资源
用例
- 租赁金融自动化
- 周边安全与访问控制
服务
- 系统集成
挑战
Ameren 需要替换 2000 年后不再受支持的遗留解决方案。经过仔细考虑和评估,选择了 ICONICS GENESIS32。
客户
阿梅伦
关于客户
Ameren 是密苏里州最大的电力公司,为密苏里州中部和东部(包括大圣路易斯地区)的大约 120 万客户提供能源服务。 Ameren 服务于密苏里州的 65 个县和 500 个城镇。 Ameren 一半以上 (55%) 的电力客户位于圣路易斯都会区。其位于富尔顿的卡拉威核电站拥有 1100 兆瓦的容量。
解决方案
Ameren 使用 ICONICS 的 GENESIS32™ 企业版 HMI/SCADA 应用程序; WebHMI™ 基于网络的实时自动化软件;以及 AlarmWorX™32 分布式企业范围的警报和事件管理系统。
GENESIS32 目前用于远程访问在线化学分析仪读数(数字输出和趋势图)。 AlarmWorX 为警报条件提供寻呼警报。
运营影响
数量效益
相关案例.
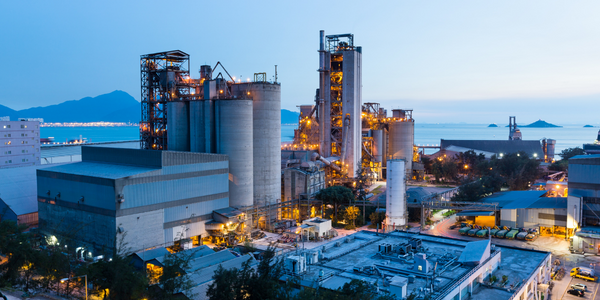
Case Study
Honeywell - Tata Chemicals Improves Data Accessibility with OneWireless
Tata was facing data accessibility challenges in the cement plant control room tapping signals from remote process control areas and other distant locations, including the gas scrubber. Tata needed a wireless solution to extend its control network securely to remote locations that would also provide seamless communication with existing control applications.
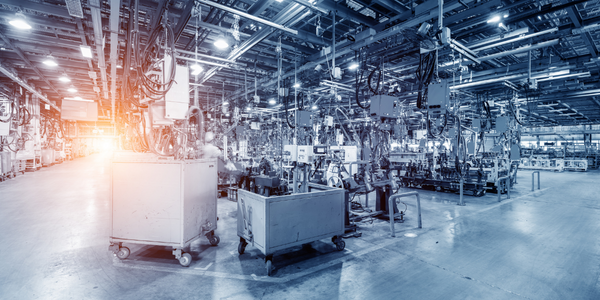
Case Study
Advanced Elastomer Systems Upgrades Production
In order to maintain its share of the international market for thermoplastic elastomers AES recently expanded its Florida plant by adding a new production line. While the existing lines were operating satisfactorily using a PROVOX distributed control system with traditional analog I/O, AES wanted advanced technology on the new line for greater economy, efficiency, and reliability. AES officials were anxious to get this line into production to meet incoming orders, but two hurricanes slowed construction.

Case Study
Wireless GPS Tracking & Security Monitoring
Enhancing the security of hazardous freight and ensuring compliance with Homeland Security’s Transportation Security Administration mandate that all trains carrying chemicals capable of creating a toxic inhalation condition are equipped with on-board safety monitoring systems.
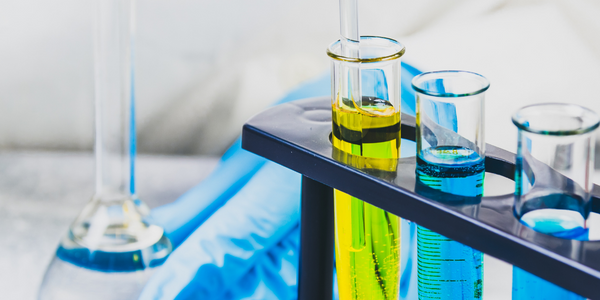
Case Study
Field Device Asset Management For Chemical Company in China
Chinese chemical subsidiary of multinational corporation serves customers throughout the world. Sales offices and research and technology centers are strategically located to provide rapid response to customer requests. Just two workers were assigned to maintain thousands of intelligent instruments in three production units, so they could do little more than react to device issues as they appeared. This costly maintenance method inevitably led to unexpected downtime when a critical instrument failed. Plant management recognized the need to change from reactive to predictive maintenance for all assets, including instruments and control valves, but help was needed in implementing such a technology-based initiative.
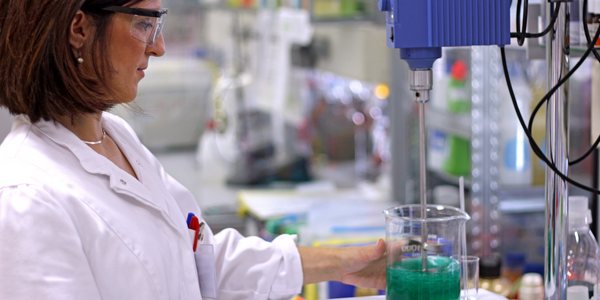
Case Study
Industrial Workforce Mobility for Improved Safety & Operations
Huntsman Corporation, a global manufacturer and marketer of differentiated chemicals, undertook an aggressive program to eliminate injuries, product defects, and environmental releases at their Port Neches facility. Termed “Project Zero”, this program required a completely mobile solution to empower operations and maintenance personnel to capture defects, track work progress and make process and safety related decisions in real-time.