下载PDF
An Integrated Approach to Traceability for a Fresh Start
技术
- 功能应用 - 制造执行系统 (MES)
适用行业
- 电子产品
适用功能
- 离散制造
- 质量保证
用例
- 自动化制造系统
- 资产跟踪
服务
- 软件设计与工程服务
- 系统集成
挑战
AT&S, a leader in the high-end printed circuit board (PCB) market, was building a new plant in China to manufacture integrated circuit (IC) substrates. They recognized that their new substrate production facility would need effective automated information flows to handle all of the data for their products. The systems in place in their six existing PCB production facilities were not adequate. These systems presented two related business challenges: efficiency of data collection and access to data about products and processes, and changing traceability requirements that require agility to revamp information sets. The current application set also presented some IT challenges. Other AT&S plants had an array of systems providing MES capabilities. These included commercial applications from the ERP provider, some applications developed on IBM Notes and homegrown software.
关于客户
Austria Technologie & Systemtechnik Aktiengesellschaft (AT&S) is a leader in the high-end or high density interconnect (HDI) printed circuit board (PCB) market. The company has been growing successfully in the high end of the technology market. To grow and implement its high-tech strategy, AT&S was building a new plant in China to manufacture integrated circuit (IC) substrates. As semiconductor line widths and electronic products shrink, IC substrates are essential interconnections between processors and board-level systems. The growth potential is enormous – across a range of applications including mobile devices, automotive, medical devices, industrial, and healthcare. The advent of wearable devices will create yet more opportunities for AT&S and other advanced manufacturers of substrates and PCBs.
解决方案
AT&S set up a project to evaluate and select an IT system, and to model the new production plant and implement the software. It needed to be ready for go-live of the new plant. AT&S reviewed its requirements by conducting multiple workshops to collect all needed inputs from the business. Based on the detailed analysis, it was clear that they needed to go in the direction of an integrated MES. They formed a multi-disciplinary team for the manufacturing execution system (MES) project. The team included Production, Production Planning, Engineering, Quality, Equipment Management, Logistics, Control Engineering, Maintenance, Production engineering and computer aided-manufacturing (PE/CAM) and IT. This nine member team put in many hours, but was not dedicated full-time to the project. AT&S initially developed a long list of 16 possible software providers. The core team narrowed the field to four finalists. Those four provided demonstrations, customer visits and a detailed analysis for each possible solution and vendor. The main aspects AT&S rated in selecting Critical Manufacturing were: risk, functionality, technology, flexibility and stability.
运营影响
数量效益
相关案例.
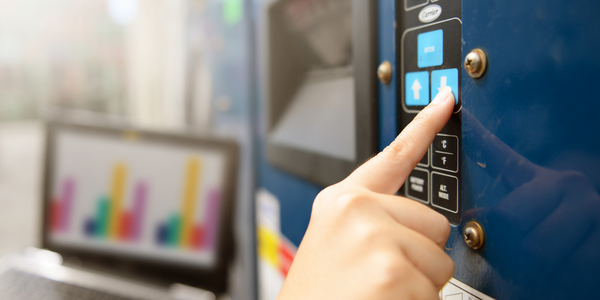
Case Study
Remote Temperature Monitoring of Perishable Goods Saves Money
RMONI was facing temperature monitoring challenges in a cold chain business. A cold chain must be established and maintained to ensure goods have been properly refrigerated during every step of the process, making temperature monitoring a critical business function. Manual registration practice can be very costly, labor intensive and prone to mistakes.
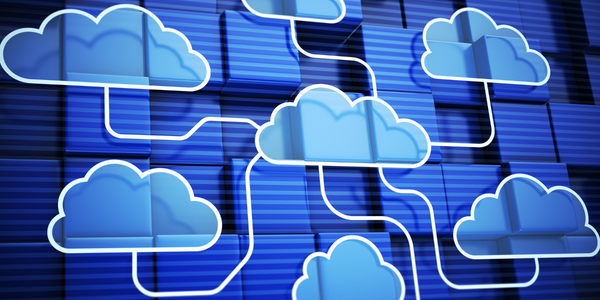
Case Study
Cloud Solution for Energy Management Platform-Schneider Electric
Schneider Electric required a cloud solution for its energy management platform to manage high computational operations, which were essential for catering to client requirements. As the business involves storage and analysis of huge amounts of data, the company also needed a convenient and scalable storage solution to facilitate operations efficiently.
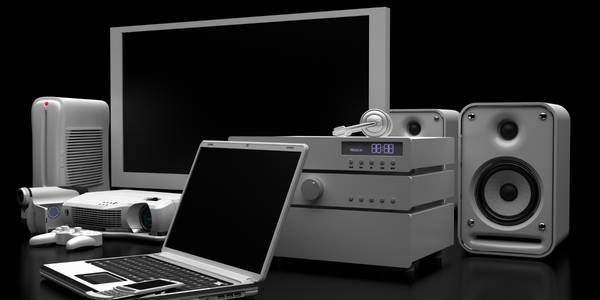
Case Study
Leveraging the IoT to Gain a Competitive Edge in International Competition
Many large manufacturers in and outside Japan are competing for larger market share in the same space, expecting a growing demand for projectors in the areas of entertainment, which requires glamor and strong visual performance as well as digital signage that can attract people’s attention. “It is becoming more and more difficult to differentiate ourselves with stand-alone hardware products,” says Kazuyuki Kitagawa, Director of Service & Support at Panasonic AVC Networks. “In order for Panasonic to grow market share and overall business, it is essential for us to develop solutions that deliver significant added value.” Panasonic believes projection failure and quality deterioration should never happen. This is what and has driven them to make their projectors IoT-enabled. More specifically, Panasonic has developed a system that collects data from projectors, visualizes detailed operational statuses, and predicts issues and address them before failure occurs. Their projectors are embedded with a variety of sensors that measure power supply, voltage, video input/ output signals, intake/exhaust air temperatures, cooling fan operations, and light bulb operating time. These sensors have been used to make the projector more intelligent, automatically suspending operation when the temperature rises excessively, and automatically switching light bulbs. Although this was a great first step, Panasonic projectors were still not equipped with any capability to send the data over a network.