下载PDF
Andrade Gutierrez's Converged Network Built on Check Point Foundation
技术
- 网络安全和隐私 - 网络安全
- 网络与连接 - 网关
适用行业
- 建筑与基础设施
- 国家安全与国防
用例
- 施工管理
- 篡改检测
服务
- 系统集成
挑战
Andrade Gutierrez (AG) 是巴西最大的重型建筑公司之一,该公司正在经历快速增长,需要一个更可靠、性能更高且更易于管理的网络。该公司正在重新设计其基础设施,以将语音和数据融合在一个网络上,并需要一个具有处理组合流量的性能和稳定性的安全解决方案。现有防火墙不稳定,公司面临升级或更换防火墙的决定。与此同时,AG 希望将安全网络连接扩展到其巴西建筑工地的所有远程办公室。虽然主要办事处有直接的网络连接,但一些较小的办事处位于网络之外,只能访问互联网。
关于客户
Andrade Gutierrez (AG) 是巴西最大的重型建筑公司之一,项目遍及拉丁美洲和欧洲。该公司参与了各种合同,包括穿越安第斯山脉的灌溉隧道、秘鲁的一条高速公路、厄瓜多尔的一座桥梁、桑托斯港(巴西)的防波堤和码头以及里斯本、里约热内卢、和圣保罗。 2004年,该公司的净利润比2003年增长了41%,比2002年增长了116%。为了保持其快速增长,AG需要一个更可靠、性能更高、更易于管理的网络。
解决方案
AG 使用 Check Point 更完整的安全解决方案取代了原有的防火墙。为了最大限度地提高其安全网关的可用性和性能,该公司选择使用 ClusterXL® 的 VPN-1® Pro™ 在其核心网络外围的两个网关之间分配流量。该解决方案提高了吞吐量,同时提供了急需的冗余。曾经没有安全方式访问企业应用程序和信息的远程建筑办公室现在可以通过 Check Point UTM-1 Edge 集成安全设备实现安全的站点到站点 IPSec VPN 连接。这些设备将访问控制、用户身份验证和加密集成在一台设备中,易于设置和管理。笔记本电脑上的 VPN-1 SecureClient 软件为移动用户提供具有相同安全级别的远程访问。 AG 通过其圣保罗数据中心的一个控制台配置其所有安全策略并管理其所有安全网关和 VPN。
运营影响
数量效益
相关案例.
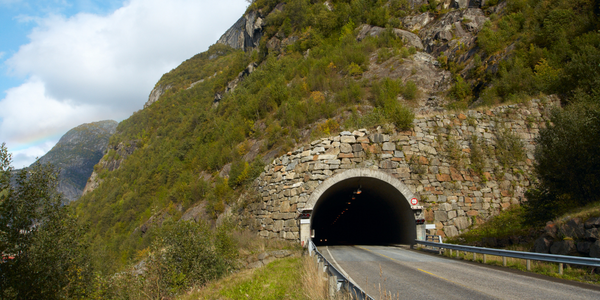
Case Study
IoT System for Tunnel Construction
The Zenitaka Corporation ('Zenitaka') has two major business areas: its architectural business focuses on structures such as government buildings, office buildings, and commercial facilities, while its civil engineering business is targeted at structures such as tunnels, bridges and dams. Within these areas, there presented two issues that have always persisted in regard to the construction of mountain tunnels. These issues are 'improving safety" and "reducing energy consumption". Mountain tunnels construction requires a massive amount of electricity. This is because there are many kinds of electrical equipment being used day and night, including construction machinery, construction lighting, and ventilating fan. Despite this, the amount of power consumption is generally not tightly managed. In many cases, the exact amount of power consumption is only ascertained when the bill from the power company becomes available. Sometimes, corporations install demand-monitoring equipment to help curb the maximum power demanded. However, even in these cases, the devices only allow the total volume of power consumption to be ascertained, or they may issue warnings to prevent the contracted volume of power from being exceeded. In order to tackle the issue of reducing power consumption, it was first necessary to obtain an accurate breakdown of how much power was being used in each particular area. In other words, we needed to be able to visualize the amount of power being consumed. Safety, was also not being managed very rigorously. Even now, tunnel construction sites often use a 'name label' system for managing entry into the work site. Specifically, red labels with white reverse sides that bear the workers' names on both sides are displayed at the tunnel work site entrance. The workers themselves then flip the name label to the appropriate side when entering or exiting from the work site to indicate whether or not they are working inside the tunnel at any given time. If a worker forgets to flip his or her name label when entering or exiting from the tunnel, management cannot be performed effectively. In order to tackle the challenges mentioned above, Zenitaka decided to build a system that could improve the safety of tunnel construction as well as reduce the amount of power consumed. In other words, this new system would facilitate a clear picture of which workers were working in each location at the mountain tunnel construction site, as well as which processes were being carried out at those respective locations at any given time. The system would maintain the safety of all workers while also carefully controlling the electrical equipment to reduce unnecessary power consumption. Having decided on the concept, our next concern was whether there existed any kind of robust hardware that would not break down at the construction work site, that could move freely in response to changes in the working environment, and that could accurately detect workers and vehicles using radio frequency identification (RFID). Given that this system would involve many components that were new to Zenitaka, we decided to enlist the cooperation of E.I.Sol Co., Ltd. ('E.I.Sol') as our joint development partner, as they had provided us with a highly practical proposal.
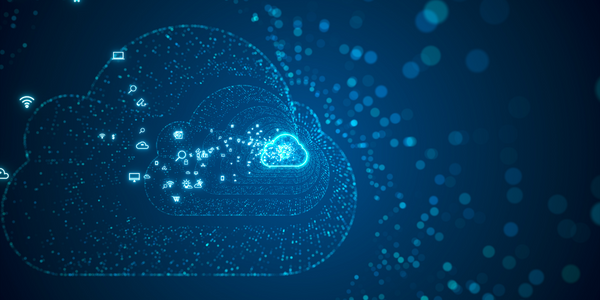
Case Study
Splunk Partnership Ties Together Big Data & IoT Services
Splunk was faced with the need to meet emerging customer demands for interfacing IoT projects to its suite of services. The company required an IoT partner that would be able to easily and quickly integrate with its Splunk Enterprise platform, rather than allocating development resources and time to building out an IoT interface and application platform.
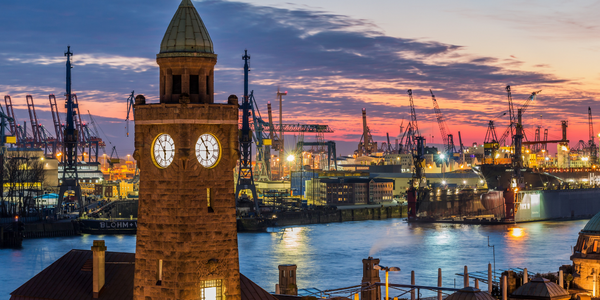
Case Study
Bridge monitoring in Hamburg Port
Kattwyk Bridge is used for both rail and road transport, and it has played an important role in the Port of Hamburg since 1973. However, the increasing pressure from traffic requires a monitoring solution. The goal of the project is to assess in real-time the bridge's status and dynamic responses to traffic and lift processes.
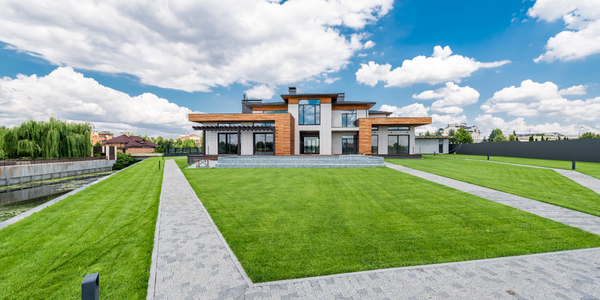
Case Study
Bellas Landscaping
Leading landscaping firm serving central Illinois streamlines operations with Samsara’s real-time fleet tracking solution: • 30+ vehicle fleet includes International Terrastar dump trucks and flatbeds, medium- and light-duty pickups from Ford and Chevrolet. Winter fleet includes of snow plows and salters.

Case Study
Condition Based Monitoring for Industrial Systems
A large construction aggregate plant operates 10 high horsepower Secondary Crusher Drive Motors and associated conveyor belts, producing 600 tons of product per hour. All heavy equipment requires maintenance, but the aggregate producer’s costs were greatly magnified any time that the necessary maintenance was unplanned and unscheduled. The product must be supplied to the customers on a tight time schedule to fulfill contracts, avoid penalties, and prevent the loss of future business. Furthermore, a sudden failure in one of the drive motors would cause rock to pile up in unwanted locations, extending the downtime and increasing the costs.Clearly, preventative maintenance was preferable to unexpected failures. So, twice each year, the company brought in an outside vendor to attach sensors to the motors, do vibration studies, measure bearing temperatures and attempt to assess the health of the motors. But that wasn’t enough. Unexpected breakdowns continued to occur. The aggregate producer decided to upgrade to a Condition Based Monitoring (CBM) sensor system that could continually monitor the motors in real time, apply data analytics to detect changes in motor behavior before they developed into major problems, and alert maintenance staff via email or text, anywhere they happened to be.A wired sensor network would have been cost prohibitive. An aggregate plant has numerous heavy vehicles moving around, so any cabling would have to be protected. But the plant covers 400 acres, and the cable would have to be trenched to numerous locations. Cable wasn’t going to work. The aggregate producer needed a wireless solution.