下载PDF
Auto group unleashes power of data
技术
- 分析与建模 - 实时分析
适用行业
- 汽车
- 零售
适用功能
- 销售与市场营销
用例
- 预测性维护
- 库存管理
服务
- 数据科学服务
- 系统集成
挑战
Greenway Automotive Group, a Florida-based organization running 46 full-service car dealerships across several states, was struggling with its Dealer Management Systems (DMS). The DMS was designed for single dealerships, making it difficult to compile consolidated financial reports, track productivity and trends, or compare the performance of different stores. The old DMS could only achieve one update a day and had limited capabilities for drilling down on various issues and generating automated reports. This compromised effective forward planning. Greenway wanted an enterprise-wide view and a reporting layer above the DMS that could show trends and market conditions, and where views could be easily customized and modified without having to log into 46 different computer systems.
关于客户
Greenway Automotive Group is a Florida-based organization that operates 46 full-service car dealerships. These dealerships include prestige brands like Alfa Romeo, and American manufacturers such as Chevy, Ford, and GMC. The dealerships are spread across several states including Alabama, Georgia, Missouri, South Carolina, Tennessee, and Texas. The group was facing challenges with its Dealer Management Systems (DMS), which were designed for single dealerships, making it difficult to compile consolidated financial reports, track productivity and trends, or compare the performance of different stores.
解决方案
Greenway decided to change from its existing DMS to a new management solution from CDK Global. At the same time, it chose to implement a Qlik data analytics solution that has been specifically customized for the automotive market by DI Squared, a Qlik Elite Partner. The solution incorporates Qlik Sense data analytics and the Qlik NPrinting reporting tool, running on top of the CDK system. DI Squared's solution enables groups to do consolidated reporting on massive amounts of data generated by multiple departments. The company can get businesses up and running with Qlik within a month and has developed templates for functions such as P&L, balance sheet, aging receivables, vehicle sales, vehicle inventory, part sales, parts inventory, repair orders, service retention, and more. The solution allows Greenway to grab all of the DMS data, merge it together with external sources like Google Analytics, vAuto, eLeads, etc., and create enterprise dashboards.
运营影响
数量效益
相关案例.
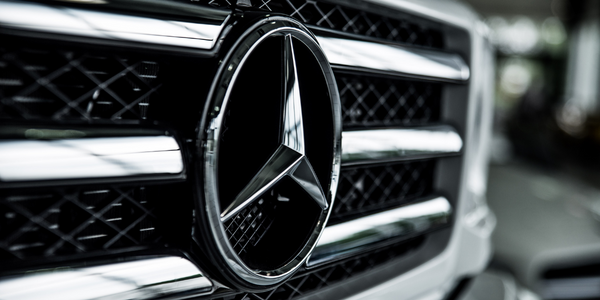
Case Study
Integral Plant Maintenance
Mercedes-Benz and his partner GAZ chose Siemens to be its maintenance partner at a new engine plant in Yaroslavl, Russia. The new plant offers a capacity to manufacture diesel engines for the Russian market, for locally produced Sprinter Classic. In addition to engines for the local market, the Yaroslavl plant will also produce spare parts. Mercedes-Benz Russia and his partner needed a service partner in order to ensure the operation of these lines in a maintenance partnership arrangement. The challenges included coordinating the entire maintenance management operation, in particular inspections, corrective and predictive maintenance activities, and the optimizing spare parts management. Siemens developed a customized maintenance solution that includes all electronic and mechanical maintenance activities (Integral Plant Maintenance).
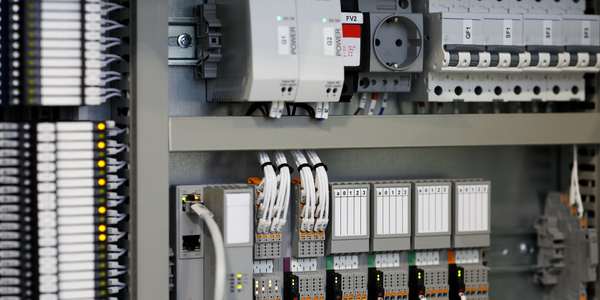
Case Study
Improving Production Line Efficiency with Ethernet Micro RTU Controller
Moxa was asked to provide a connectivity solution for one of the world's leading cosmetics companies. This multinational corporation, with retail presence in 130 countries, 23 global braches, and over 66,000 employees, sought to improve the efficiency of their production process by migrating from manual monitoring to an automatic productivity monitoring system. The production line was being monitored by ABB Real-TPI, a factory information system that offers data collection and analysis to improve plant efficiency. Due to software limitations, the customer needed an OPC server and a corresponding I/O solution to collect data from additional sensor devices for the Real-TPI system. The goal is to enable the factory information system to more thoroughly collect data from every corner of the production line. This will improve its ability to measure Overall Equipment Effectiveness (OEE) and translate into increased production efficiencies. System Requirements • Instant status updates while still consuming minimal bandwidth to relieve strain on limited factory networks • Interoperable with ABB Real-TPI • Small form factor appropriate for deployment where space is scarce • Remote software management and configuration to simplify operations