下载PDF
BACnet enabled Wireless Temperature Monitoring System

技术
- 功能应用 - 远程监控系统
- 网络与连接 - 网关
- 传感器 - 空气污染传感器
- 传感器 - 湿度传感器
- 传感器 - 温度传感器
适用功能
- 设施管理
用例
- 楼宇自动化与控制
挑战
客户提供了一个由无线发射器和应用软件组成的温度监测系统。第三方 BACnet 应用程序(例如楼宇自动化系统)需要访问由无线传感器设备测量的重要参数,例如温度、湿度、二氧化碳等。客户需要一种解决方案,以允许从其温度监测系统与 BMS 进行数据交换。
客户
未公开
关于客户
无线温度和湿度变送器的领先制造商。
解决方案
SoftDEL 开发了一款软件 BACnet 网关,可将来自温度监测系统的传感器数据转换为 BACnet 格式。 SoftDEL 使用自己的 BACnet/IP 堆栈来开发网关解决方案。网关包括一个数据记录设施,用于存储数据直到检索。
收集的数据
Carbon Dioxide Emissions, Device Status, Humidity, Temperature
运营影响
相关案例.
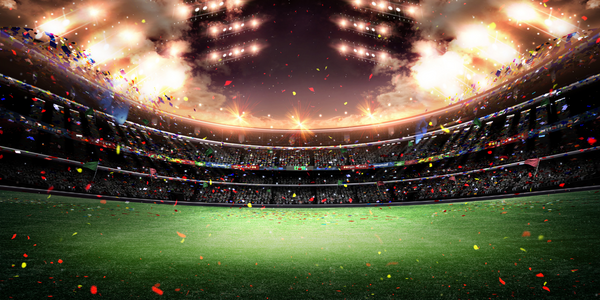
Case Study
Turning A Stadium Into A Smart Building
Honeywell created what it called the “intelligent system” for the National Stadium in Beijing, China, turning the venue for the opening and closing events at the 2008 Summer Olympics into a “smart building.” Designed by highly controversial artist Ai Weiwei, the “Bird’s Nest” remains one of the most impressive feats of stadium architecture in the world. The 250,000 square meter structure housed more than 100,000 athletes and spectators at a time. To accommodate such capacity, China turned to Honeywell’s EBI Integrated Building Management System to create an integrated “intelligent system” for improved building security, safety and energy efficiency.

Case Study
Medanta the Medicity
Medanta is one of India's largest multi-super specialty institutes located in Gurgaon, India. Some of the key challenges facing Medanta included: - No Monitoring & Control over Energy Use, Indoor Air Quality, Indoor Lighting Quality & Noise Levels. - No compliance monitoring of temperature & pressure in critical care wards. - Energy bills were a surprise with no way to forecast energy costs. - Missing data & insights that could be used for targeting areas of improvement. - Existing Billing Management System (BMS) was inflexible and could not be used across the enterprise to serve the needs of different users. Requirements Based on these challenges, Medanta was looking for a comprehensive solution to Monitor & Control: - Energy Usage - Power Generators - Clean Rooms - HVAC Temperature - Chiller Temperature - Hydrant Pressure - Air Quality & Noise Levels - Critical Wards
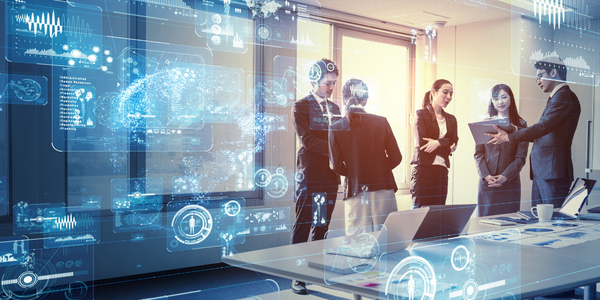
Case Study
Sirqul and Catalyst Workplace Activation Reveal the Future of Smart Offices
This partnership will disrupt the “traditional” office furniture conversation by examining the intersection of people, place, and technology. We realize it is increasingly evident that the design of spaces is an enabler to meaningful interactions between people and fosters a sense of community and culture by taking on the challenges of designing for a more productive, collaborative, and inspiring workplace, leveraging technology to process data on how people work, communicate and engage with one another.
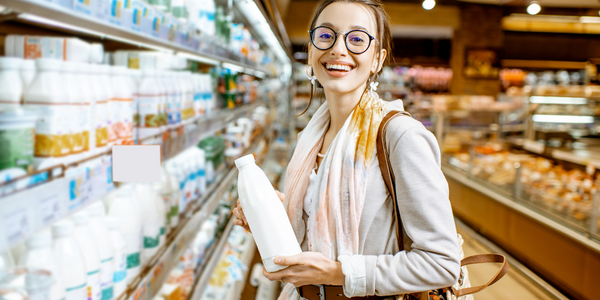
Case Study
Ensures Cold Milk in Your Supermarket
As of 2014, AK-Centralen has over 1,500 Danish supermarkets equipped, and utilizes 16 operators, and is open 24 hours a day, 365 days a year. AK-Centralen needed the ability to monitor the cooling alarms from around the country, 24 hours a day, 365 days a year. Each and every time the door to a milk cooler or a freezer does not close properly, an alarm goes off on a computer screen in a control building in southwestern Odense. This type of alarm will go off approximately 140,000 times per year, equating to roughly 400 alarms in a 24-hour period. Should an alarm go off, then there is only a limited amount of time to act before dairy products or frozen pizza must be disposed of, and this type of waste can quickly start to cost a supermarket a great deal of money.
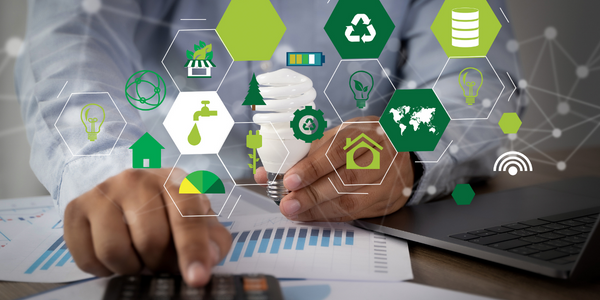
Case Study
IoE Increases Operational Efficiencies and Improves Energy Management
For many manufacturing companies today, the opportunity to connect people, process, data, and things created by the Internet of Everything (IoE) presents a new way to look at factory automation. The opportunity for digital innovation often arises when a company is expanding capacity or building a new production facility. Mahindra and Mahindra, one of India’s leading automakers, seized the opportunity to deploy a connected factory of the future at their new Chakan facility.