下载PDF
Blending the right reasons with GainSeeker Suite to make a sensible investment
技术
- 功能应用 - 制造执行系统 (MES)
- 分析与建模 - 实时分析
- 自动化与控制 - 可编程逻辑控制器 (PLC)
适用行业
- 消费品
- 包装
适用功能
- 流程制造
- 质量保证
用例
- 预测性维护
- 机器状态监测
- 过程控制与优化
服务
- 软件设计与工程服务
- 系统集成
挑战
The engineering and quality leaders at a consumer goods packaging company saw an opportunity to increase throughput and profitability by automating the ingredient mixing process. The existing manual process involved significant downtime and inefficiencies, particularly during product changeovers, which required shutting down high-speed lines for 5 to 10 minutes multiple times a day. This downtime added up to a significant amount of lost production time. Additionally, the manual mixing process was labor-intensive and required meticulous documentation to meet regulatory requirements. The company needed a solution that would not only automate the mixing process but also ensure compliance with regulatory standards.
关于客户
The customer is a consumer goods packaging company that has been in operation for several years. They have a strong focus on quality and efficiency, having previously implemented Lean Six Sigma projects to improve their processes. The company operates multiple high-speed production lines and is tightly regulated, requiring meticulous documentation to ensure product quality and compliance with federal regulations. The company has a solid business incentive to push for smaller production lots, which necessitates frequent product changeovers. They are committed to continuous improvement and are always looking for ways to increase throughput and profitability.
解决方案
The company implemented a new automated, continuous batch mixing process using computer-controlled (PLC) equipment and software. This new process eliminated the manual mixing of ingredients, reducing the workload in the mixing department by 25%. The GainSeeker Suite was used to collect data automatically from the PLCs that control the flow meters feeding the ingredients into the mix. GainSeeker calculated and stored all the necessary values, providing real-time information and a data historian to help understand and improve the process. This system allowed the Quality Manager to monitor trends and identify issues before they became problems, ensuring the correct formulation of products and compliance with regulatory requirements. The automated process not only improved efficiency but also provided the necessary documentation to meet regulatory standards, making it a sensible investment for the company.
运营影响
数量效益
相关案例.
.png)
Case Study
Improving Vending Machine Profitability with the Internet of Things (IoT)
The vending industry is undergoing a sea change, taking advantage of new technologies to go beyond just delivering snacks to creating a new retail location. Intelligent vending machines can be found in many public locations as well as company facilities, selling different types of goods and services, including even computer accessories, gold bars, tickets, and office supplies. With increasing sophistication, they may also provide time- and location-based data pertaining to sales, inventory, and customer preferences. But at the end of the day, vending machine operators know greater profitability is driven by higher sales and lower operating costs.
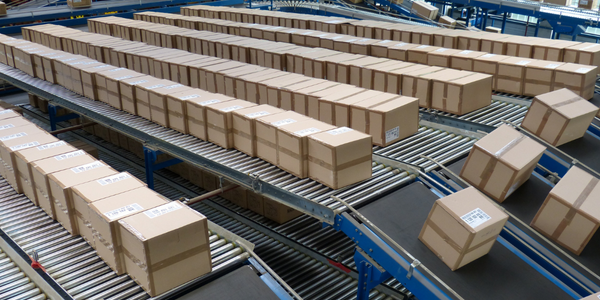
Case Study
IoT Data Analytics Case Study - Packaging Films Manufacturer
The company manufactures packaging films on made to order or configure to order basis. Every order has a different set of requirements from the product characteristics perspective and hence requires machine’s settings to be adjusted accordingly. If the film quality does not meet the required standards, the degraded quality impacts customer delivery causes customer dissatisfaction and results in lower margins. The biggest challenge was to identify the real root cause and devise a remedy for that.
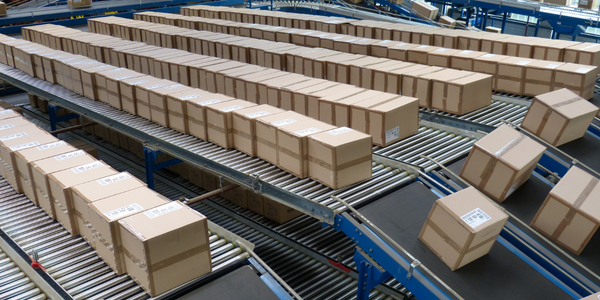
Case Study
Zenon the Ideal Basis for An Ergonomic HMI
KHS develops and produces machines and equipment for filling and packaging in the drinks industry. Because drinks manufacturing, filling and packaging consist of a number of highly complex processes, the user-friendly and intuitive operation of equipment is increasingly gaining in significance. In order to design these processes as simple as possible for the user, KHS decided to introduce a uniform, transparent and standardized solution to the company. The HMI interface should meet the requirement for people with different qualifications and enable them to work on a standard platform.
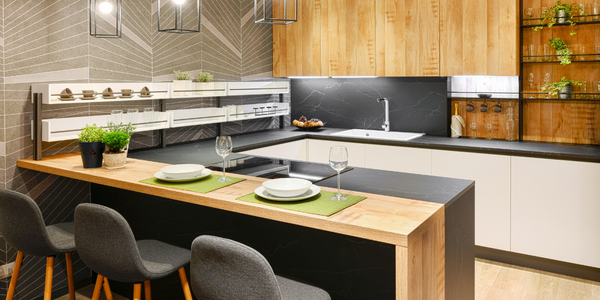
Case Study
Series Production with Lot-size-1 Flexibility
Nobilia manufactures customized fitted kitchens with a lot size of 1. They require maximum transparency of tracking design data and individual processing steps so that they can locate a particular piece of kitchen furniture in the sequence of processes.