下载PDF
Breakthrough Performance
技术
- 功能应用 - 企业资源规划系统 (ERP)
- 应用基础设施与中间件 - 数据交换与集成
- 功能应用 - 库存管理系统
适用行业
- 化学品
- 电子产品
适用功能
- 仓库和库存管理
- 商业运营
- 质量保证
用例
- 库存管理
- 预测性维护
- 供应链可见性(SCV)
服务
- 系统集成
- 软件设计与工程服务
- 培训
挑战
Epoxy Technology, a leading manufacturer of specialty adhesives, faced significant challenges due to rapid growth and reliance on manual processes. They struggled with filling customer orders by hand, tracking raw materials, and managing over 500 products with mixed ratios. Manual fill tickets led to order inaccuracies, and the lack of real-time insight made it difficult to analyze batch history or predict stock loads. This resulted in customer dissatisfaction and internal miscommunications. Epoxy needed to automate their supply chain to increase efficiency and meet growing demand.
关于客户
Epoxy Technology is a prominent manufacturer of specialty adhesives used in advanced technology applications such as electronics, medical devices, semiconductors, and fiber optics. Their products are distributed in over 70 countries through a network of qualified representatives and distributors. The company has a diverse product range, with over 500 products that require precise mixed ratios. Epoxy Technology's rapid growth and high demand for their products necessitated a shift from manual processes to automated systems to maintain efficiency and customer satisfaction.
解决方案
Epoxy Technology implemented the Vicinity solution integrated with Microsoft Dynamics GP over the course of a year. This integration allowed them to automate their supply chain, ensuring accurate formulas and seamless data exchange between systems. The Vicinity solution enabled Epoxy to predict batches, maintain product readiness, and shorten lead times. They adopted the FIFO method for production, ensuring quality and efficient stock management. The integration also provided real-time insight into raw materials and associated costs, streamlining internal audits and order processing. Vicinity's flexibility allowed for customizations to meet Epoxy's unique needs, such as managing and shipping adhesive kits.
运营影响
数量效益
相关案例.
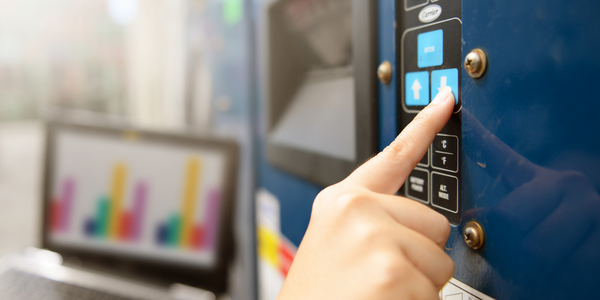
Case Study
Remote Temperature Monitoring of Perishable Goods Saves Money
RMONI was facing temperature monitoring challenges in a cold chain business. A cold chain must be established and maintained to ensure goods have been properly refrigerated during every step of the process, making temperature monitoring a critical business function. Manual registration practice can be very costly, labor intensive and prone to mistakes.
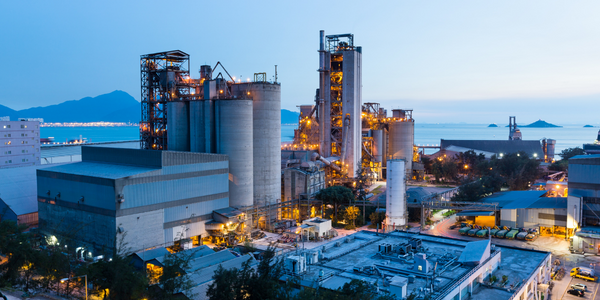
Case Study
Honeywell - Tata Chemicals Improves Data Accessibility with OneWireless
Tata was facing data accessibility challenges in the cement plant control room tapping signals from remote process control areas and other distant locations, including the gas scrubber. Tata needed a wireless solution to extend its control network securely to remote locations that would also provide seamless communication with existing control applications.
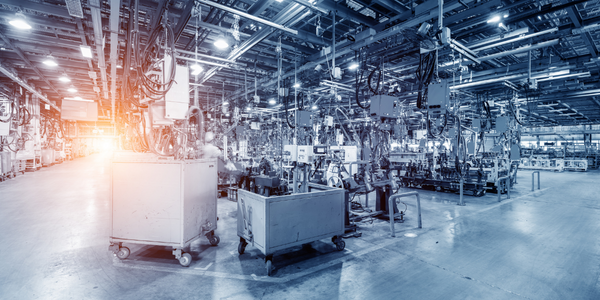
Case Study
Advanced Elastomer Systems Upgrades Production
In order to maintain its share of the international market for thermoplastic elastomers AES recently expanded its Florida plant by adding a new production line. While the existing lines were operating satisfactorily using a PROVOX distributed control system with traditional analog I/O, AES wanted advanced technology on the new line for greater economy, efficiency, and reliability. AES officials were anxious to get this line into production to meet incoming orders, but two hurricanes slowed construction.