下载PDF
CinePostproduction: Speeding delivery of digital cinema packages for theatre release using hybrid cloud model
技术
- 基础设施即服务 (IaaS) - 云计算
- 基础设施即服务 (IaaS) - 混合云
适用功能
- 物流运输
用例
- 资产跟踪
服务
- 云规划/设计/实施服务
挑战
CinePostproduction 是德国一家领先的后期制作机构,它面临着加快媒体文件采集和向整个 DACH 地区的电影院交付大型数字影院包 (DCP) 的挑战。从 35 毫米胶片到数字影院的过渡对该公司来说是一个重大挑战。尽管已经转向数字化,但分发 DCP 的最常见方法仍然是通过快递或卫星运送专用硬盘。这种方法不仅速度慢、不可靠,而且成本高昂。媒体文件的数量和大小使这一挑战更加复杂:DCP 的大小通常在 100GB 到 400GB 之间。对于其电视和电影后期制作业务领域,CinePostproduction 需要发送每部故事片 150GB 到 1.5TB 的数据集,有时需要在全球范围内传输。
关于客户
CinePostproduction 是德国领先的后期制作机构之一,多年来一直活跃于数字影院市场。该公司提供一系列服务,包括故事片和电视节目的后期制作、DCP 副本复制、DCP 版本控制和母版制作、预告片本地化和 KDM 服务。CinePostproduction 开发软件解决方案已有四年多,其中包括 DCP 门户 SHARC。DA-CH 地区的大多数影院都使用此解决方案下载 DCP 影院预告片,同时还为发行商提供了一种舒适灵活的 DCP 密钥创建和管理方式。该公司成立于 1911 年,是 35 毫米胶片向数字影院过渡的先驱。
解决方案
CinePostproduction 将 IBM® Aspera® on Demand 集成到其新的 SHARC 系统中,以加快从工作室提取 DCP 并将 DCP 直接交付到影院的速度。SHARC 系统完全集成了在云中运行的 Aspera on Demand,使 CinePostproduction 能够在其数据中心的 CinePostproduction 内容交付网络服务器和 DACH 地区的参与影院之间传输加密的高分辨率数字影院包 (DCP),分辨率高达 2K 或 4K。该分发平台极具成本效益,因为影院可以利用其现有的基础设施来实现最快速度的交付。他们只需安装包含嵌入式 Aspera 客户端的 CinePostproduction 下载客户端软件,然后通过现有的宽带连接直接从 SHARC 将 DCP 接收到影院即可。在云中运行 Aspera On Demand 使 CinePostproduction 能够根据需要扩展传输容量,以帮助满足不断变化的需求并按时交付给影院。
运营影响
数量效益
相关案例.
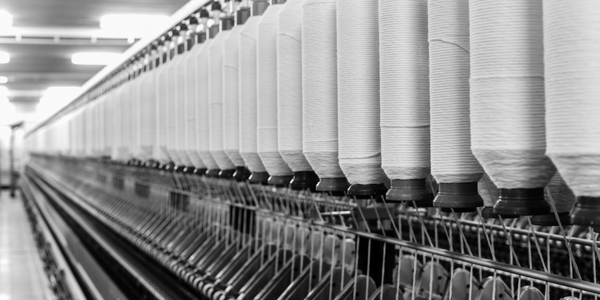
Case Study
IoT Applications and Upgrades in Textile Plant
At any given time, the textile company’s manufacturing facility has up to 2,000 textile carts in use. These carts are pushed from room to room, carrying materials or semi-finished products. Previously, a paper with a hand-written description was attached to each cart. This traditional method of processing made product tracking extremely difficult. Additionally, making sure that every cart of materials or semi-finished products went to its correct processing work station was also a problem. Therefore, the company desired an intelligent solution for tracking assets at their factories. They also wanted a solution that would help them collect process data so they could improve their manufacturing efficiency.
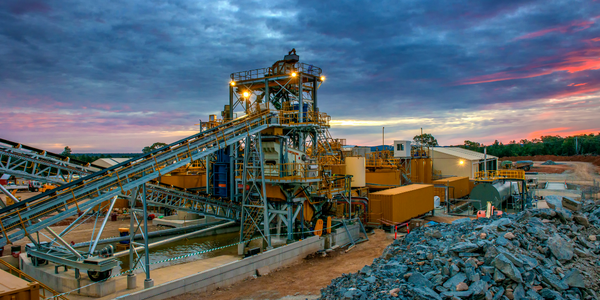
Case Study
Goldcorp: Internet of Things Enables the Mine of the Future
Goldcorp is committed to responsible mining practices and maintaining maximum safety for its workers. At the same time, the firm is constantly exploring ways to improve the efficiency of its operations, extend the life of its assets, and control costs. Goldcorp needed technology that can maximize production efficiency by tracking all mining operations, keep employees safe with remote operations and monitoring of hazardous work areas and control production costs through better asset and site management.
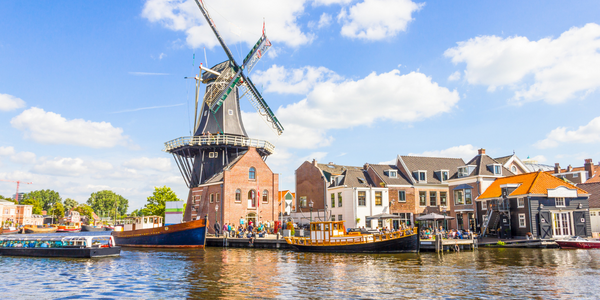
Case Study
Buoy Status Monitoring with LoRa
The Netherlands are well-known for their inland waterways, canals, sluices and of course port activities. The Dutch Ministry of Infrastructure indicates that there are thousands of buoys and fixed items in and near water environments that would profit from IoT monitoring. One of the problems with buoys for example, is that they get hit by ships and the anchor cable breaks. Without connectivity, it takes quite some time to find out that something has happened with that buoy. Not to mention the costs of renting a boat to go to the buoy to fix it. Another important issue, is that there is no real-time monitoring of the buoys at this moment. Only by physically visiting the object on the water, one gains insight in its status.
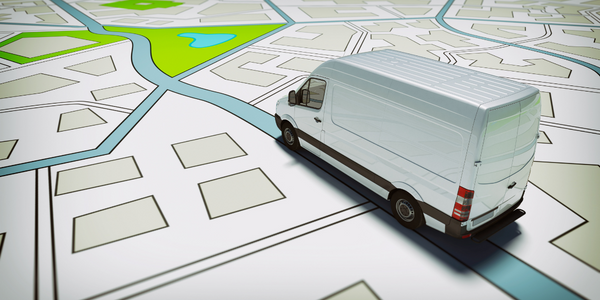
Case Study
IoT Based Asset Tracking System
The existing system used by the customer could only track a few thousand assets and was able to generate only a few standard set of reports. As the number of assets tracked grew exponentially, the system started to break at the seams. The Tracking devices were from different manufacturers following different protocols. There was no proper integration among the devices to send instant alerts. There are thousands of tracking devices spread across multiple geographies, that are moving. The configuration and troubleshooting of these devices incurred heavy costs, which was a logistics challenge. The existing system did not provide sophisticated Analytics, Business Intelligence and Insights from the data
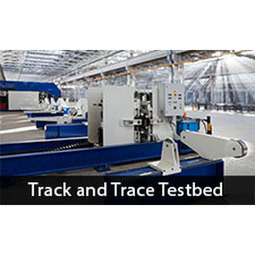
Case Study
IIC - Track and Trace Testbed
Factory systems can detect - within a meter - the location of a tool; Misuse of tools can result in serious accident or injury; The production of many industrial and consumer goods requires exacting work - down to the precise force used to tighten a screw. GOAL Manage smart, hand-held tools in manufacturing, maintenance, and industrial environments