下载PDF
ComfortFit Labs: Digital Transformation with FactoryFour
技术
- 平台即服务 (PaaS) - 应用开发平台
适用行业
- 医疗保健和医院
适用功能
- 离散制造
用例
- 数字孪生
- 大规模定制
服务
- 软件设计与工程服务
挑战
ComfortFit Labs, a New Jersey-based packaging manufacturer that designs and manufactures custom orthotics, was facing a challenge with their traditional order processing workflow. The process was tedious, involving significant manual labor and long turnaround times. Customers would send plaster casts of their patients’ limbs along with paper order forms to ComfortFit. The order data was recorded manually, and when a work order was issued to the floor, technicians had to manually measure the cast and find the right mold out of hundreds to manufacture from. This resulted in an average 7–20 day turnaround time with a process that was prone to human error from order entry.
关于客户
ComfortFit Labs is a New Jersey-based packaging manufacturer that designs and manufactures custom orthotics. Their manufacturing process involves more than 50 production personnel that produce more than 80,000 products per year. Each orthotic is made per customer and combines several different types of materials and techniques. The company was facing challenges with their traditional order processing workflow, which was tedious and prone to human error. The process involved significant manual labor and long turnaround times, with customers sending plaster casts of their patients’ limbs along with paper order forms.
解决方案
ComfortFit Labs implemented the FactoryFour platform to create a completely digital order workflow. Customers could log into ComfortFit’s order intake portal, fill out a digital order form specific to ComfortFit’s product, and take a scan via an iPad-mounted 3D scanner. The order form was automatically validated for errors prior to submission, reducing the risk of human error. Once submitted, the order appeared instantly in ComfortFit’s manufacturing queue. Using FactoryFour’s 3D file analysis engine, measurements were automatically captured from the scan and were presented with a “best-fit” code that identified which mold to produce from. As the device moved through production, the customer received automatic notifications and visibility into the status of their order.
运营影响
数量效益
相关案例.
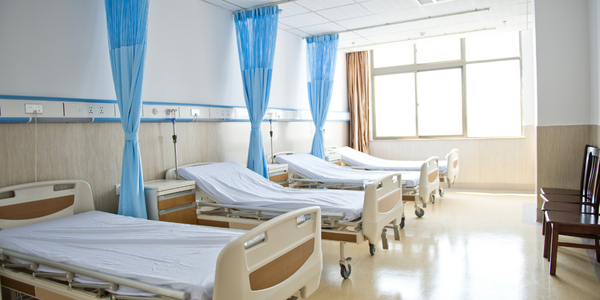
Case Study
Hospital Inventory Management
The hospital supply chain team is responsible for ensuring that the right medical supplies are readily available to clinicians when and where needed, and to do so in the most efficient manner possible. However, many of the systems and processes in use at the cancer center for supply chain management were not best suited to support these goals. Barcoding technology, a commonly used method for inventory management of medical supplies, is labor intensive, time consuming, does not provide real-time visibility into inventory levels and can be prone to error. Consequently, the lack of accurate and real-time visibility into inventory levels across multiple supply rooms in multiple hospital facilities creates additional inefficiency in the system causing over-ordering, hoarding, and wasted supplies. Other sources of waste and cost were also identified as candidates for improvement. Existing systems and processes did not provide adequate security for high-cost inventory within the hospital, which was another driver of cost. A lack of visibility into expiration dates for supplies resulted in supplies being wasted due to past expiry dates. Storage of supplies was also a key consideration given the location of the cancer center’s facilities in a dense urban setting, where space is always at a premium. In order to address the challenges outlined above, the hospital sought a solution that would provide real-time inventory information with high levels of accuracy, reduce the level of manual effort required and enable data driven decision making to ensure that the right supplies were readily available to clinicians in the right location at the right time.
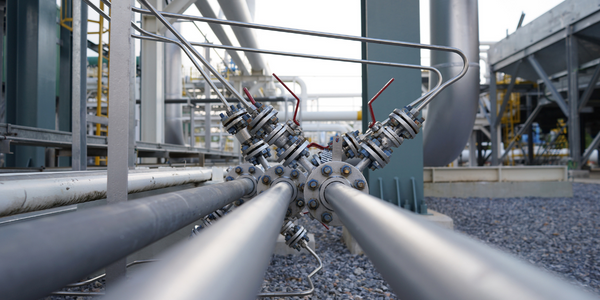
Case Study
Gas Pipeline Monitoring System for Hospitals
This system integrator focuses on providing centralized gas pipeline monitoring systems for hospitals. The service they provide makes it possible for hospitals to reduce both maintenance and labor costs. Since hospitals may not have an existing network suitable for this type of system, GPRS communication provides an easy and ready-to-use solution for remote, distributed monitoring systems System Requirements - GPRS communication - Seamless connection with SCADA software - Simple, front-end control capability - Expandable I/O channels - Combine AI, DI, and DO channels
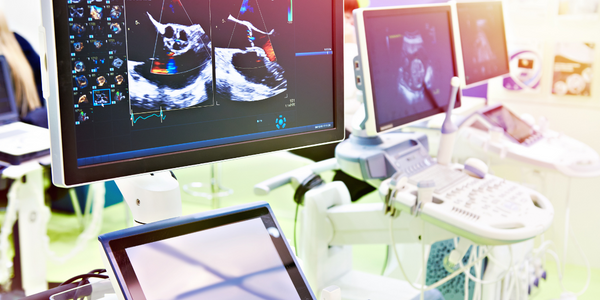
Case Study
Driving Digital Transformations for Vitro Diagnostic Medical Devices
Diagnostic devices play a vital role in helping to improve healthcare delivery. In fact, an estimated 60 percent of the world’s medical decisions are made with support from in vitrodiagnostics (IVD) solutions, such as those provided by Roche Diagnostics, an industry leader. As the demand for medical diagnostic services grows rapidly in hospitals and clinics across China, so does the market for IVD solutions. In addition, the typically high cost of these diagnostic devices means that comprehensive post-sales services are needed. Wanteed to improve three portions of thr IVD:1. Remotely monitor and manage IVD devices as fixed assets.2. Optimizing device availability with predictive maintenance.3. Recommending the best IVD solution for a customer’s needs.
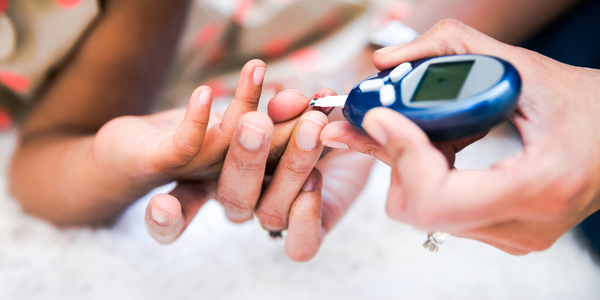
Case Study
HaemoCloud Global Blood Management System
1) Deliver a connected digital product system to protect and increase the differentiated value of Haemonetics blood and plasma solutions. 2) Improve patient outcomes by increasing the efficiency of blood supply flows. 3) Navigate and satisfy a complex web of global regulatory compliance requirements. 4) Reduce costly and labor-intensive maintenance procedures.
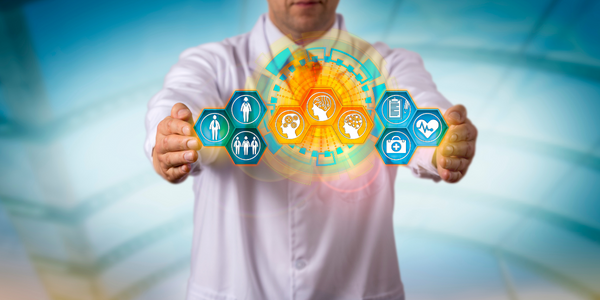
Case Study
Harnessing real-time data to give a holistic picture of patient health
Every day, vast quantities of data are collected about patients as they pass through health service organizations—from operational data such as treatment history and medications to physiological data captured by medical devices. The insights hidden within this treasure trove of data can be used to support more personalized treatments, more accurate diagnosis and more advanced preparative care. But since the information is generated faster than most organizations can consume it, unlocking the power of this big data can be a struggle. This type of predictive approach not only improves patient care—it also helps to reduce costs, because in the healthcare industry, prevention is almost always more cost-effective than treatment. However, collecting, analyzing and presenting these data-streams in a way that clinicians can easily understand can pose a significant technical challenge.