下载PDF
Delivering Better Buildings: the RACE to BIM
技术
- 分析与建模 - 预测分析
- 功能应用 - 远程监控系统
适用行业
- 医疗保健和医院
- 建筑与基础设施
适用功能
- 设施管理
- 质量保证
用例
- 预测性维护
- 远程资产管理
- 数字孪生
服务
- 软件设计与工程服务
- 系统集成
- 培训
挑战
The Design Büro faced the challenge of transitioning to Building Information Modeling (BIM) to meet the UK government's mandate for all government buildings to be delivered using BIM by 2016. The firm needed to upgrade its software and adopt a BIM workflow to continue working on government-funded projects. The transition was crucial as The Design Büro specializes in creating health and social care facilities, and they needed to ensure their designs met the clinical goals of their clients while maintaining sustainability, practicality, and budget constraints. The firm tested Vectorworks Architect software with a traditional 2D process on The Tamarind Centre project before fully committing to BIM.
关于客户
The Design Büro is an architectural firm founded in 1991 in Warwickshire, United Kingdom. The firm specializes in creating health and social care facilities that contribute to the wellbeing of individuals. The designers at The Design Büro believe that environments play a significant role in the healing process, and they work closely with the people who will use their buildings to ensure the designs meet their clinical goals. The firm focuses on the needs of patients, their families, and staff members to provide supportive, inspiring, and flexible environments. The Design Büro has a strong reputation for delivering sustainable, practical, and budget-conscious projects, making them successful in their field.
解决方案
The Design Büro's first large-scale BIM project was the Pathology Department building for the Ysbyty Glan Clywd Hospital in North Wales. The firm used Vectorworks Architect software to transition from a 2D to a 3D workflow. They set up parallel design teams, with one group working in 2D and the other in 3D. The 3D team quickly outpaced the 2D team, leading to the entire project being moved to 3D. The firm collaborated closely with key stakeholders and specialist subcontractors, utilizing BIM for cost, speed, and health and safety benefits. The Design Büro implemented a new business management strategy in January 2014, defining the workflow for staff members to follow when completing projects using 3D with BIM. They also enlisted the help of Computers Unlimited for training and improved their collaborative abilities through Industry Foundation Classes (IFC) testing. The firm relied on tutorials from the Vectorworks YouTube page for training new employees, helping them become comfortable with the workflows quickly.
运营影响
数量效益
相关案例.
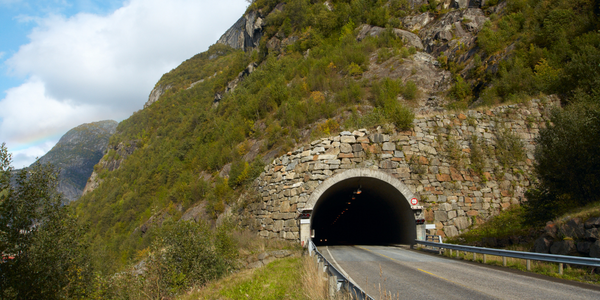
Case Study
IoT System for Tunnel Construction
The Zenitaka Corporation ('Zenitaka') has two major business areas: its architectural business focuses on structures such as government buildings, office buildings, and commercial facilities, while its civil engineering business is targeted at structures such as tunnels, bridges and dams. Within these areas, there presented two issues that have always persisted in regard to the construction of mountain tunnels. These issues are 'improving safety" and "reducing energy consumption". Mountain tunnels construction requires a massive amount of electricity. This is because there are many kinds of electrical equipment being used day and night, including construction machinery, construction lighting, and ventilating fan. Despite this, the amount of power consumption is generally not tightly managed. In many cases, the exact amount of power consumption is only ascertained when the bill from the power company becomes available. Sometimes, corporations install demand-monitoring equipment to help curb the maximum power demanded. However, even in these cases, the devices only allow the total volume of power consumption to be ascertained, or they may issue warnings to prevent the contracted volume of power from being exceeded. In order to tackle the issue of reducing power consumption, it was first necessary to obtain an accurate breakdown of how much power was being used in each particular area. In other words, we needed to be able to visualize the amount of power being consumed. Safety, was also not being managed very rigorously. Even now, tunnel construction sites often use a 'name label' system for managing entry into the work site. Specifically, red labels with white reverse sides that bear the workers' names on both sides are displayed at the tunnel work site entrance. The workers themselves then flip the name label to the appropriate side when entering or exiting from the work site to indicate whether or not they are working inside the tunnel at any given time. If a worker forgets to flip his or her name label when entering or exiting from the tunnel, management cannot be performed effectively. In order to tackle the challenges mentioned above, Zenitaka decided to build a system that could improve the safety of tunnel construction as well as reduce the amount of power consumed. In other words, this new system would facilitate a clear picture of which workers were working in each location at the mountain tunnel construction site, as well as which processes were being carried out at those respective locations at any given time. The system would maintain the safety of all workers while also carefully controlling the electrical equipment to reduce unnecessary power consumption. Having decided on the concept, our next concern was whether there existed any kind of robust hardware that would not break down at the construction work site, that could move freely in response to changes in the working environment, and that could accurately detect workers and vehicles using radio frequency identification (RFID). Given that this system would involve many components that were new to Zenitaka, we decided to enlist the cooperation of E.I.Sol Co., Ltd. ('E.I.Sol') as our joint development partner, as they had provided us with a highly practical proposal.
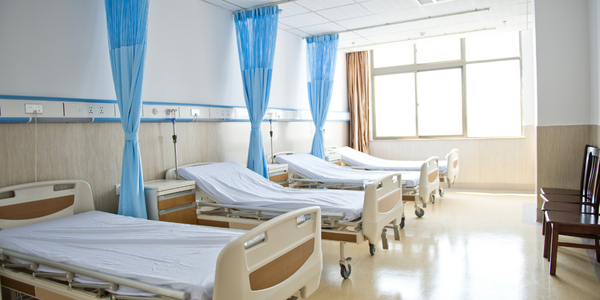
Case Study
Hospital Inventory Management
The hospital supply chain team is responsible for ensuring that the right medical supplies are readily available to clinicians when and where needed, and to do so in the most efficient manner possible. However, many of the systems and processes in use at the cancer center for supply chain management were not best suited to support these goals. Barcoding technology, a commonly used method for inventory management of medical supplies, is labor intensive, time consuming, does not provide real-time visibility into inventory levels and can be prone to error. Consequently, the lack of accurate and real-time visibility into inventory levels across multiple supply rooms in multiple hospital facilities creates additional inefficiency in the system causing over-ordering, hoarding, and wasted supplies. Other sources of waste and cost were also identified as candidates for improvement. Existing systems and processes did not provide adequate security for high-cost inventory within the hospital, which was another driver of cost. A lack of visibility into expiration dates for supplies resulted in supplies being wasted due to past expiry dates. Storage of supplies was also a key consideration given the location of the cancer center’s facilities in a dense urban setting, where space is always at a premium. In order to address the challenges outlined above, the hospital sought a solution that would provide real-time inventory information with high levels of accuracy, reduce the level of manual effort required and enable data driven decision making to ensure that the right supplies were readily available to clinicians in the right location at the right time.
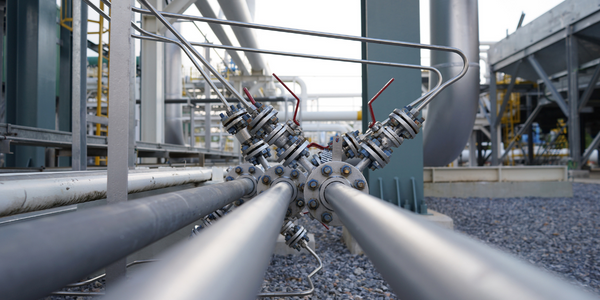
Case Study
Gas Pipeline Monitoring System for Hospitals
This system integrator focuses on providing centralized gas pipeline monitoring systems for hospitals. The service they provide makes it possible for hospitals to reduce both maintenance and labor costs. Since hospitals may not have an existing network suitable for this type of system, GPRS communication provides an easy and ready-to-use solution for remote, distributed monitoring systems System Requirements - GPRS communication - Seamless connection with SCADA software - Simple, front-end control capability - Expandable I/O channels - Combine AI, DI, and DO channels
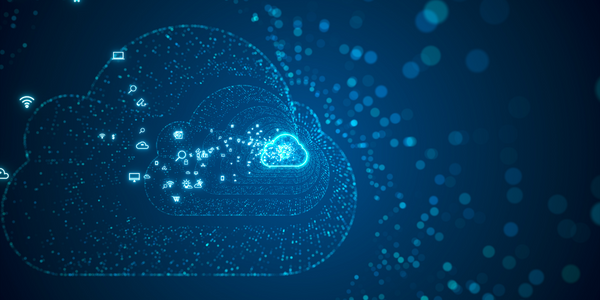
Case Study
Splunk Partnership Ties Together Big Data & IoT Services
Splunk was faced with the need to meet emerging customer demands for interfacing IoT projects to its suite of services. The company required an IoT partner that would be able to easily and quickly integrate with its Splunk Enterprise platform, rather than allocating development resources and time to building out an IoT interface and application platform.
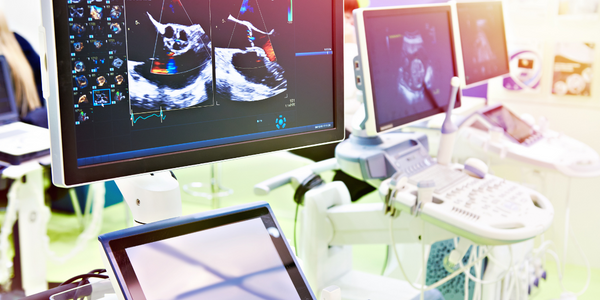
Case Study
Driving Digital Transformations for Vitro Diagnostic Medical Devices
Diagnostic devices play a vital role in helping to improve healthcare delivery. In fact, an estimated 60 percent of the world’s medical decisions are made with support from in vitrodiagnostics (IVD) solutions, such as those provided by Roche Diagnostics, an industry leader. As the demand for medical diagnostic services grows rapidly in hospitals and clinics across China, so does the market for IVD solutions. In addition, the typically high cost of these diagnostic devices means that comprehensive post-sales services are needed. Wanteed to improve three portions of thr IVD:1. Remotely monitor and manage IVD devices as fixed assets.2. Optimizing device availability with predictive maintenance.3. Recommending the best IVD solution for a customer’s needs.