下载PDF
Delivering the World’s Slimmest Gesture-Controlled Smart Band
技术
- 可穿戴设备 - 手表/手套/腕上电脑
适用行业
- 消费品
适用功能
- 产品研发
- 销售与市场营销
用例
- 零售店自动化
服务
- 硬件设计与工程服务
- 系统集成
挑战
Titan Company was focused on developing a unique wearable to address the demand in the urban youth market through their Fastrack brand. Since the product was targeted at youth, cost targets were challenging for the project to be viable. Also, the 9mm slimness meant that the entire assembly of the band had to be done in a very controlled environment with plenty of technical expertise.
关于客户
Titan Company Limited, a joint venture between the TATA Group and the Tamil Nadu Industrial Development Corporation (TIDCO) commenced operations in 1984 under the name Titan Watches Limited. Titan Company is the fifth largest integrated own-brand watch manufacturer in the world. With a retail footprint of over 1,400 stores, Titan Company has India’s largest specialty retail network spanning over 240 towns. Today, Titan Company Limited is TATA’s largest consumer company, and India’s leading producer and retailer of watches, jewelry, eyewear and accessories. Titan is one of the few players to launch a smart wearable for the Indian market.
解决方案
With vast experience in designing and building products for an intelligent world, we offered optimized solutions in both engineering and manufacturing processes for Reflex Wav. In the product development stage, PCBA design saw circuit boards, metal parts and battery packs integrated to lower materials cost and ease scalability. Along with other optimization efforts, we provided prototyping, process analysis/development, testing, validation and integration services in ensuring seamless transition to production. Our GPSC team also extended support in procuring parts and components at faster pace and optimum prices. This has enabled Titan Company to stay within production costs, schedules and expectations. In manufacturing the Reflex Wav, we provided expertise in PCB assembly, test and advanced engineering, NPI, pilot and volume ramping, process reliability tests and failure analysis. At the same time, we also facilitated continuous lean activities to maximize yield. The final product is then delivered to customers via a robust logistics network.
运营影响
相关案例.
.png)
Case Study
Improving Vending Machine Profitability with the Internet of Things (IoT)
The vending industry is undergoing a sea change, taking advantage of new technologies to go beyond just delivering snacks to creating a new retail location. Intelligent vending machines can be found in many public locations as well as company facilities, selling different types of goods and services, including even computer accessories, gold bars, tickets, and office supplies. With increasing sophistication, they may also provide time- and location-based data pertaining to sales, inventory, and customer preferences. But at the end of the day, vending machine operators know greater profitability is driven by higher sales and lower operating costs.
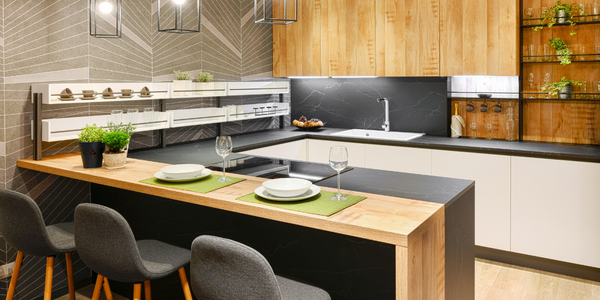
Case Study
Series Production with Lot-size-1 Flexibility
Nobilia manufactures customized fitted kitchens with a lot size of 1. They require maximum transparency of tracking design data and individual processing steps so that they can locate a particular piece of kitchen furniture in the sequence of processes.
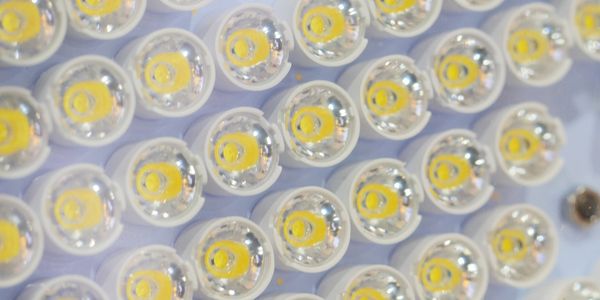
Case Study
American Eagle Achieves LEED with GE LED Lighting Fixtures
American Eagle Outfitters (AEO) was in the process of building a new distribution center. The AEO facility management team decided to look at alternate options for lighting layout that could provide energy and maintenance savings. AEO would need a full-time maintenance employee just to replace burned-out fluorescent tubes.
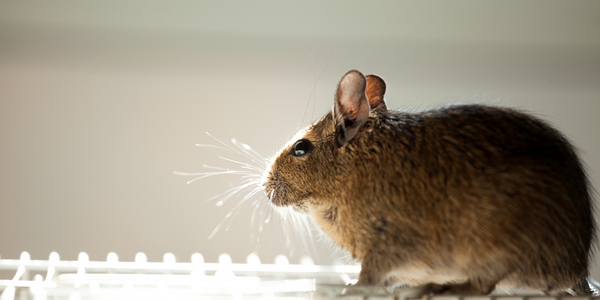
Case Study
Revolutionizing Rodent Control
From pet- and child-safe traps, to touch-free and live-catch rodent control solutions, Victor continues to stay committed to producing superior products that meet the varying needs of today’s pest control professionals. And, with a long standing history supporting customers in the food processing, service, and retail settings, Victor knew that strict regulations were costing organizations thousands of dollars in excess overhead trying to manage their rodent-control solutions. Trap inspections in these environments are often difficult and time consuming, requiring personnel to manually check a trap’s status multiple times per day, amounting to over six hours of manual labor. Victor is looking for an innovative way to increase operational efficiencies with the use of technology.